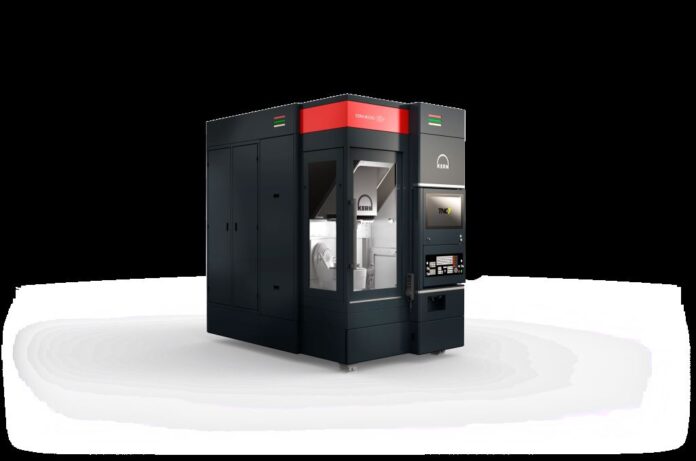
Stanzen ist das effizienteste Verfahren zur Massenproduktion von kompakten Bauteilen aus Blech. Folgeverbundwerkzeuge mit Formeinsätzen aus verschleißfestem Material bilden dabei die entscheidende Basis. Für die Herstellung der Formeinsätze setzen innovative Werkzeug- und Formenbauer zunehmend auf fünfachsige Highend-Bearbeitungszentren wie die Kern Micro HD+. Damit lassen sich in einer Aufspannung beste Ergebnisse in puncto Genauigkeit und Oberfläche erzielen.
Während aktuell viele Branchen mit sinkenden Absatzzahlen zu kämpfen haben, wächst der Bedarf für kleine und große Elektromotoren stetig um sieben bis neun Prozent per anno. Prognosen zufolge soll dies auch mindestens die nächsten fünf Jahre so weitergehen. Dabei spielt die Anwendung in zahllosen Consumerprodukten eine ebenso große Rolle wie jene in medizin- und energietechnischen Produkten. Die Automatisierung in der Industrie und E-Mobilität forciert das Wachstum zusätzlich.
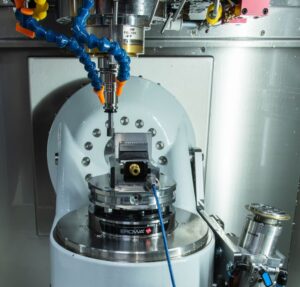
Für diese zukunftsträchtigen Produkte werden massenhaft Blechkleinteile wie Steckverbinder und ähnliches benötigt. Ein perfektes Einsatzgebiet für Stanztechnik. Um die Fertigung der Bauteile in Hochlohnländern wirtschaftlich abbilden zu können, sind einerseits automatisierte Stanzzentren gefragt. Zum anderen müssen die Folgeverbundwerkzeuge samt Formeinsätze höchste Ansprüche erfüllen.
Zur Herstellung der Formeinsätze aus hochfesten Stählen oder Hartmetall gehen Fertigungsbetriebe unterschiedliche Wege. Laut Branchenexperten übernehmen Fräsmaschinen noch immer häufig „nur“ die präzise Vorfertigung.
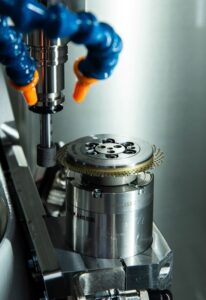
Die weitere Verarbeitung und das Finish passiert dann auf Schleifmaschinen und in aufwendiger Handarbeit durch Polieren o. ä. Mit diesem mehrstufigen Ablauf gehen jedoch einige Nachteile einher, denn jedes Umspannen birgt Risiken für die Genauigkeit.
Nicht zu vergessen: Auch Produktivität und Wirtschaftlichkeit leiden unter lange dauernder und teurer Handarbeit. Darüber hinaus hängt das Ergebnis stark von der Tagesform des Mitarbeiters ab und lässt sich dadurch nie genau reproduzieren. Sebastian Guggenmos, Vice President bei Kern Microtechnik, ergänzt: „Am Ende des Tages ist jedes produzierte Folgeverbundwerkzeug ein bisschen anders.“ Ein Problem, das umso größere Bedeutung hat, wenn Formeinsätze nachgefertigt werden. Dann sollten sie exakt dem Vorgänger entsprechen, ansonsten fallen die Endprodukte ebenfalls unterschiedlich aus.
Innovative Lösung: Formeinsätze in einer Aufspannung fertigen
Bei fortschrittlichen Unternehmen der Branche setzt sich daher sukzessive eine andere Lösung durch. Sie arbeiten mit hochpräzisen Bearbeitungszentren, die Formeinsätze in einer Aufspannung fertigen – ohne händische Nacharbeit. Ideale Voraussetzungen bietet dafür das fünfachsige Bearbeitungszentrum Kern Micro HD+. Die von der KERN Microtechnik GmbH, Eschenlohe, entwickelte und produzierte Maschine ist in der Lage, sämtliche Bearbeitungsschritte mit absolut gleichbleibender Qualität vollautomatisch durchzuführen.
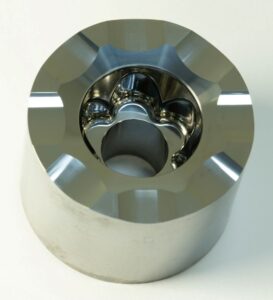
Das heißt: Im ersten Schritt erledigen günstige Schleifstifte durch Konturschleifen diverse Schruppaufgaben. Im zweiten und dritten Schritt gilt es, durch fünfachsiges trochoidales Konturfräsen die Profile und via Pendelhubschleifen die Mantelflächen zu schlichten. Finales Polieren ist dank der höchstpräzisen Schlichtvorgänge überflüssig.
Um die mit einer Kern Micro HD+ erzielbare, hohe Qualität sowie die kurzen Bearbeitungszeiten nachzuweisen, hat der Eschenloher Maschinenbauer mehrere komplexe Formeinsätze im Testverfahren hergestellt – jeweils in einer Aufspannung. Um nur ein Beispiel zu nennen: Der Hartmetall-Schmiedestempel für einen Pentalob Schraubenkopf wurde entsprechend produziert und anschließend vermessen. Das Bauteil stellt besonders hohe Anforderungen an Formgenauigkeit und Oberflächenrauheit der Konturen und Kegelflächen.
Hartmetall-Schmiedestempel: Rekordqualität in Rekordzeit
Nun der Reihe nach. Zu allererst wird die Kontur in einem Schruppvorgang vorgeschliffen. Zeitbedarf: fünf Minuten. Nach dem wenige Sekunden dauernden Werkzeugwechsel auf eine passende Schleifscheibe, beginnen bereits die Schlichtvorgänge. Das Pendelhubschleifen an den Mantelflächen war nach 17 Minuten erledigt, so dass zu guter Letzt noch fünfachssimultane Fräsenarbeiten für die anspruchsvolle Konturbearbeitung des spröden Materials anstanden. Mit Diamantwerkzeugen gelang dies innerhalb von einer Stunde und 13 Minuten.
„Wenn ein solcher Hartmetallstempel im Standardprozess mit zwei oder drei Maschinen und finaler Handarbeit hergestellt wird, dauert das ein Mehrfaches der hier in Summe benötigten gut eineinhalb Stunden“, ist sich Guggenmos sicher.
Nicht zu vergessen, die mit der Kern Micro HD+ erzielten, reproduzierbaren Ergebnisse sind unvergleichbar. So liegt die mit einem Zeiss Prismo (taktiles Messverfahren) nachgewiesene Genauigkeit der Formkontur bei <4 µm und jene der Mantelfläche bei <1,5 µm. Ebenso interessant sind die erzielten Oberflächengüten. Das nach SIM-CLSM-Messverfahren arbeitende Confovis Duo Vario bestätigte ein Rauheitsprofil von Ra<0,015 µm und eine Flächengenauigkeit von Sa<0,02 µm.
Voraussetzung: stabiles und dynamisches Fünfachszentrum
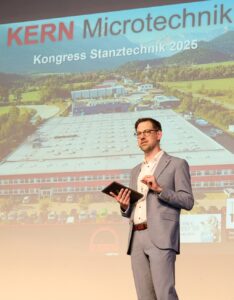
Solche Ergebnisse lassen sich nur erreichen, wenn die eingesetzte Maschine extrem steif und gleichzeitig ausnehmend dynamisch ist. Die Kern Micro HD+ vereint diese Eigenschaften mit thermischer Stabilität, Genauigkeit und Verschleißfreiheit in einmaliger Weise. Entscheidend dafür sind unter anderem die eingesetzten Linearmotoren sowie die auf der patentierten Microspalthydrostatik basierende Lagertechnik, die in allen Linear- und Rundachsen zum Einsatz kommt. Dank dieser Technologie werden einmalige Steifigkeitswerte erreicht, die letztlich höchste Präzision und Dynamik ermöglicht.
Nicht zuletzt aufgrund der genannten technischen Highlights gilt Kern Microtechnik als Technologieführer der Branche. Sebastian Guggenmos freut sich darüber. Er freut sich aber noch mehr über das, was er mit seinem Team aktuell entwickelt, über das er aber nur soviel sagen darf: „Wir dringen ständig in neue Dimensionen der Präzision vor und lieben es, Grenzen zu verschieben. Das liegt in unserer DNA.“
Kontakt: