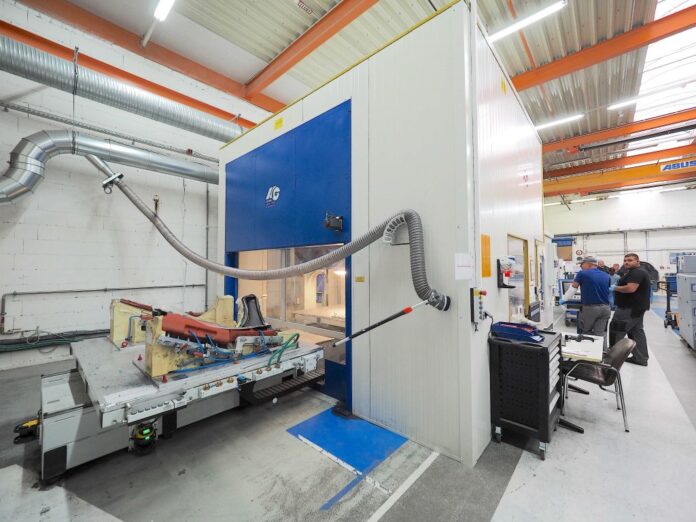
Der TIER 1-Lieferant fertigt überwiegend carbonfaserverstärkte Kunststoffteile für automobile Premiumhersteller. Sie beziehen von ihm vor allem Sichtteile in Class-A-Qualität und Strukturbauteile aus CFK, deren Konturen und Beschnitte vor dem Lackieren gefräst werden müssen. Hierzu setzt das Unternehmen vom Bodensee drei 5-Achs-CNC-Portal-Fräsanlagen des Typs P-S-F (20-25)/S von HG GRIMME SysTech ein.
Einfacher Wechsel zwischen baugleichen Maschinen
Die baugleichen Bearbeitungszentren mit jeweils zwei Tischen und Shuttle sowie Siemens 840d sl-Steuerung hat ACE zwischen 2016 und 2024 erworben. Eine einheitliche Bedienung und Maschinentische mit demselben Bohrbild mit einem festen Nullpunkt tragen ebenfalls zu kurzen Rüstzeiten bei. Außerdem kann ACE die CFK-Teile auf allen Maschinen von HG GRIMME SysTech abwechselnd und ohne Qualitätseinschränkungen nachbearbeiten.
CFK-Stäube werden abgesaugt
Die Fräsanlagen sind für Werkstücke mit Außenmaßen bis 2.000 x 2.500 x 650 mm geeignet, die dank Eilganggeschwindigkeiten von 80 m/min in X/U/Y und 30 m/min in Z ausgesprochen dynamisch bearbeitet werden können.
Doppeltische und Shuttle sorgen für eine Maschinenlänge von knapp 11 Metern und eine Breite von etwas unter sechs Metern. Das bietet gleichzeitig ausreichend Raum für eine gute Zugänglichkeit von Maschinentisch und Fräskopf von allen Seiten.
Die zu bearbeitenden Bauteile sind bis zu 2.000 x 2.500 mm groß, bei Dicken zwischen 1 und 3 mm, die Losgrößen variieren meist zwischen 500 und 10.000 Stück.
Rund zwei Drittel der Produkte sind Sichtteile, überwiegend für PKW-Karosserien, insbesondere Kotflügel und Motorhauben. Bei den übrigen handelt es sich um Strukturteile wie Monocoques für den Antriebsstrang, Batteriemulden für Elektrofahrzeuge und Verkleidungen für B-Säulen und Mittelstege.
Angesichts der starken Staubentwicklung beim CFK-Fräsen sind CNC-Bearbeitungszentren von HG GRIMME SysTech komplett eingehaust, eine Absauganlage beseitigt viele Schwebepartikel bereits in der Kabine. Darüber hinaus werden die Bauteile nach der Bearbeitung noch einmal von Hand mit Hochdruck gereinigt.
CFK-Komponenten fertigt ACE meist im geschlossenen RTM-Verfahren
ACE fertigt neunzig Prozent der CFK-Komponenten und -Baugruppen im geschlossenen RTM-Verfahren. Hierbei werden textile Preforms zugeschnitten und zu Gelegen vorbereitet, die dann in Pressen eingelegt, mit Harz injiziert und zu Schalen gebacken werden. Die Ränder der zwei oder seltener drei Schalen müssen noch gefräst werden, bevor sie anschließend zum Carbonteil verklebt werden.
Nach dem Kontur- und Beschnittfräsen werden die verklebten und lackierten Komponenten geprüft, bevor sie ACE an die Montagebänder seiner Kunden liefert. Hierzu gehören bekannte Marken wie Lamborghini, Porsche und Aston Martin, Bugatti, BMW, Mercedes, AMG, Audi und Volkswagen. Die wichtigsten Abnehmer aus der Luftfahrt sind Airbus und Boeing.
Lob für Solidität, Zuverlässigkeit und Kompetenz
Peter Klaus Gröschl, Fertigungsleiter und einer der Geschäftsführer von ACE, lobt neben der Solidität und Zuverlässigkeit der Anlagen auch den Service von HG GRIMME SysTech. Sein Fazit: „Bei HG GRIMME verstehen sie etwas vom Verarbeiten von Verbundwerkstoffen, die Kommunikation ist auf Augenhöhe. Das Unternehmen ist bodenständig. Wir arbeiten gerne zusammen.“
Kontakt: