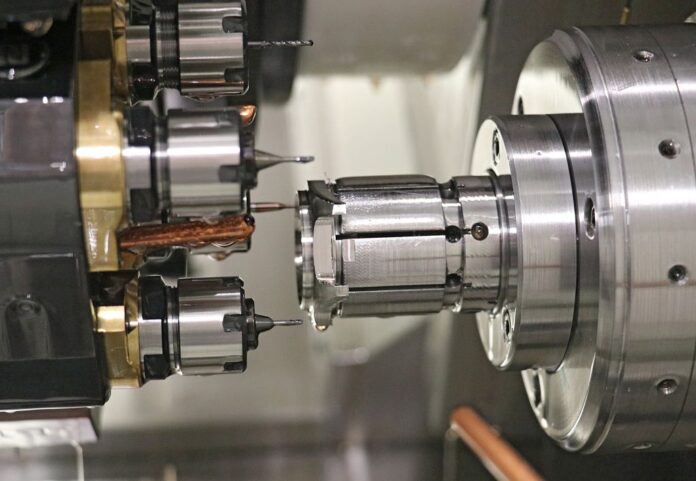
Uhrgehäuse entstehen nicht nur von der Stange, sondern auch aus Schmiederohlingen. Um diese wirtschaftlich herzustellen, nutzt die RP-Uhrgehäuse GmbH ein von teamtec, Alzenau, konzipiertes BIGLIA Drehzentrum B 620YS mit roboterautomatisiertem Teilehandling. Der 15-fach-Revolver ist mit über 30 Werkzeugen bestückt. Bis zu vier angetriebene Vierfach-Halter ermöglichen umfangreiche Fräs- und Bohroperationen, so dass die Gehäuse komplettzerspant aus der Maschine kommen.
Wo würden Sie den Standort eines deutschen Unternehmens mit dem Namen RP-Uhrgehäuse GmbH vermuten? Genau, in Pforzheim, dem Zentrum der deutschen Schmuck- und Uhrenindustrie. Rolf Koch ist seit 2011 Inhaber und Geschäftsführer der Firma, die auf eine über 85jährige Geschichte zurückblicken kann. Er selbst sammelte erst im Sondermaschinenbau Berufserfahrung, bevor er in die Welt der Armbanduhren eintauchte und eine anhaltende Begeisterung dafür entwickelte.
„Armbanduhren sind so viel mehr, als nur Zeitansager“, betont Rolf Koch. „Meine Liebe gilt den besonderen Uhren, die kleine Kunstwerke sind und denen man die bei der Herstellung investierte Leidenschaft ansieht. Wir produzieren Uhrgehäuse aus Edelstahl, Titan, Silber, Bronze, Platin oder Gold, die maßgenau, formschön und so hochwertig verarbeitet sind, dass man sie ohne Weiteres in die Schmuckschatulle legen könnte. Wirkliche Kunstwerke.“
Moderne Maschinen sorgen für Aufschwung
Mit entsprechendem Engagement ging Rolf Koch nach der Übernahme den Umbau des Uhrgehäuse-Herstellers an. Er erinnert sich: „Der Maschinenpark war veraltet und eignete sich nicht mehr, um unsere anspruchsvollen Produkte in Deutschland wirtschaftlich zu fertigen.“
Um diese auch in kleinen Serien besser und schneller herstellen zu können, investierte Rolf Koch gleich zu Beginn in ein BIGLIA Drehzentrum B 565YS – ausgestattet mit Y-Achse, angetriebenen Werkzeugen, zwei C-Achsen und Gegenspindel sowie einem 3-Meter-Stangenlader und einer Bauteilabführung über ein Förderband. „Die Maschine bot bei Vergleichen mit anderen Fabrikaten das beste Preis-Leistungsverhältnis und wurde mir als ausgesprochen zuverlässig empfohlen. Auch die räumliche Nähe zum Lieferanten teamtec war für uns ein wichtiger Entscheidungsfaktor“, sagt Rolf Koch.
Mit dem BIGLIA Drehzentrum B 565YS und einer ebenfalls neu gekauften Schweizer 5-Achs-Schleifmaschine kam die RP-Uhrgehäuse GmbH in die Erfolgsspur. Heute beliefert das Unternehmen namhafte Uhrenhersteller vor allem in Deutschland und Europa, aber auch darüber hinaus. Einen wesentlichen Anteil am Erfolg spricht Rolf Koch seinen 36 Mitarbeiterinnen und Mitarbeitern zu: „Von der Produktentwicklung, über die Maschinenprogrammierung bis hin zu den finalen Polieraufgaben leisten diese wirklich glänzende Arbeit.“
Ein Drehzentrum für die Komplettbearbeitung
Zu den Leistungsträgern zählt Hajian S., der die BIGLIA B 565YS seit 2013 betreut und damit komplexe Teile mit Hinterschneidungen, mit Fräsungen und Bohrungen erzeugt. Laut Firmenchef Rolf Koch programmiert und bedient er die Maschine mit einer Akribie, so dass sie höchste Präzision erreicht und kaum Toleranzschwankungen auftreten. Dank der Automatisierung mit Stangenlader und Abführtransportband läuft die Maschine rund um die Uhr, auch am Wochenende. Und sie liefert heute noch Bearbeitungsergebnisse in einem Toleranzfeld von unter 0,01 mm.
Auf diesen Erfahrungen aufbauend entschied sich Rolf Koch im Jahr 2024, ins Nachfolgemodell – eine BIGLIA B 620YS – zu investieren. Er erklärt: „Besonders hochwertige Gehäuse stellen wir aus geprägten oder gestanzten Rohlingen aus Edelstahl, Titan und Bronze her. Für die automatisierte Bearbeitung solcher Einlegeteile hat uns bisher noch eine geeignete Maschine gefehlt.“
Schmiederohlinge schneller und effizienter zerspanen
Die Fertigung der Schmiederohlinge ist eine Kompetenz, die neben RP nur wenige Uhrgehäusehersteller besitzen. Die endkonturnahen Rohlinge entstehen in einem mehrfachen Schmiede- und Prägevorgang mit einer Presskraft von 160 Tonnen. Sie weisen eine hochverdichtete, lunkerfreie Struktur auf, ideal für die später perfekt polierten Oberflächen.
Für die Präzisionszerspanung dieser Rohlinge benötigte RP-Uhrgehäuse früher bis zu fünf Aufspannungen auf drei Maschinen fürs Drehen, Fräsen und Schleifen.
„Dieser Aufwand muss sich verringern lassen“, war Rolf Koch überzeugt. Ihm schwebte eine weitgehende Komplettbearbeitung auf einer Maschine vor, mit automatisiertem Handling der Roh- und Fertigteile.
Eine solche Lösung konnte ihm schließlich Claudio Lista, Vertriebsleiter von teamtec, bieten: „Unsere BIGLIA B 620YS ist ein Drehzentrum, das sich ideal für anspruchsvolle Stangen- und Futterbearbeitung eignet. Ihre hochdynamischen Motorspindeln und der 15-fach-Werkzeugrevolver ermöglichen sowohl eine leistungsstarke Dreh- als auch Fräsbearbeitung.“
Lista hebt insbesondere den Revolver hervor, der einen semidirekten Antrieb enthält, also mit nur einer Anflanschung und ohne weitere Umlenkung auskommt. Der wassergekühlte Motor verfügt über eine integrierte Öl-/Luft-Minimalmengenschmierung und treibt mit 6000 min-1 die Werkzeuge an. „Wir können die Werkzeugplätze mit angetriebenen Mehrfachhaltern ausrüsten, so dass dem Anwender eine große Anzahl verschiedener Fräs- und Bohrwerkzeuge zur Verfügung stehen. Damit kann er beide Seiten der Gehäuse an Haupt- und Gegenspindel zerspanen.“
Alles aus einer Hand
teamtec ist seit über 25 Jahren als Generalvertreter des italienischen CNC-Drehmaschinenherstellers BIGLIA in Deutschland tätig. Doch die Alzenauer Zerspanungsspezialisten fokussieren nicht nur die Maschine, sondern den vollständigen Fertigungsprozess.
So boten sie als Systempartner – ergänzend zum Drehzentrum – eine angedockte Automatisierungszelle an, in der ein Roboter das Teilehandling inklusive Wasch- und Messaufgaben übernimmt. Claudio Lista betont: „Von uns bekommt der Kunde alles aus einer Hand – von der Beratung bei der Maschinenwahl über die Optimierung der Bearbeitungsstrategie bis zur automatisierten Fertigungsanlage, inklusive Schulungen und Service.“
Für Rolf Koch und sein Zerspanungsteam passte das Angebot perfekt. Sie entschieden sich für die BIGLIA B 620YS quasi in Vollausstattung – mit Y-Achse, Gegenspindel und weiteren Details wie einer Absaugung und Feuerlöschanlage, da sie mit Ölschmierung betrieben wird. Für die Reinigung und Temperierung des Öls sorgt eine KNOLL-Aufbereitungsanlage. „Die war uns aus zwei Gründen wichtig“, sagt Rolf Koch.
„Für unsere Präzisionsbearbeitung muss die Maschine eine konstante Temperatur aufweisen. Nach Stillständen erreichen wir diese schneller durch ein vorgewärmtes Schmiermedium. Und der Filter entfernt selbst feinste Späne aus dem Öl, was sich in verbesserten Oberflächen bemerkbar macht.“
Angetriebene Mehrfachhalter meistern umfangreiche Bohr- und Fräsoperationen
Ein Highlight ist die Ausstattung des Revolvers mit Mehrfachhaltern für angetriebene Werkzeuge, die speziell für RP-Uhrgehäuse entwickelt wurden. „Wir haben unsere Anforderungen mit teamtec diskutiert und in Mehrfachhaltern eindeutige Vorteile erkannt“, erklärt Rolf Koch. „Je nach Anwendungsfall nutzen wir im Revolver bis zu vier Werkzeughalter, die mit jeweils vier angetrieben Spindeln ausgestattet sind.
Das erleichtert dem Bediener das Einrichten und erhöht die Präzision.“ Laut Hajian S., der neben der BIGLIA B 565 nun auch die neue B 620 betreut, hat sich dieses Konzept für Uhrgehäuse und die erforderliche Schnittleistung bewährt. „Wenn ich das Zentrieren, Bohren, Gewinden und Ausspindeln auf vier Einheiten in einem Halter verteile, dann habe ich ganz kurze Wege und keinen Wärmegang.“
Automatisierung – einfach, robust, zuverlässig
Besonders effizient arbeitet die BIGLIA B 620YS durch die vom teamtec-Partner ND Technik, Faulbach, realisierte Automatisierung, die den bedienerarmen Betrieb über Nacht und am Wochenende ermöglicht. Kernelement ist ein Gelenkarmroboter, der in einer angedockten Automatisierungszelle platziert ist. Er belädt die Maschine mit Rohlingen, die auf einem Förderband in die Zelle transportiert werden.
Zudem übernimmt er den Wechsel von Vorder- zur Rückseitenbearbeitung und legt schließlich das fertig bearbeitete Teil auf einem aus der Zelle führenden Band ab. Auch das Waschen und Messen der Teile gehört zu seinen Aufgaben. „Das System ist mit robusten mechanischen Elementen gestaltet und funktioniert äußerst zuverlässig“, bestätigt Hajian S.. „Auch den Umgang mit dem Roboter habe ich schnell gelernt. Eineinhalb Tage Schulung und ein bisschen Übung, dann ist das kein Problem.“
Rolf Koch ist überzeugt, dass sich seine Investition in kurzer Zeit amortisiert. „Diese Fertigungszelle schafft neue Möglichkeiten bei der Bearbeitung von komplexen Einlegeteilen, wodurch wir unser Angebotsspektrum erweitern können. Zudem erreichen wir eine sehr hohe Präzision und Oberflächengüte, was nicht nur unsere Polierer total happy macht. Und im Endeffekt erfreut es die Kunden, die von uns ein perfektes Schmuckstück fürs Handgelenk bekommen.“
Kontakt: