Sonnenschirme auf dem Parkplatz, Sonnenschirme am Eingang, Sonnenschirme im Treppenhaus, Sonnenschirme im Besprechungsbereich, Sonnenschirme im Showroom, Sonnenschirme in der Montagehalle. Ein Besuch der Bahama GmbH in Reichshof in Nordrhein-Westfalen lässt keinen Zweifel daran, was hier produziert wird: Sonnenschirme. Allerdings geht es dabei nicht um gewöhnliche Sonnenschirme, sondern um sehr hochwertige Produkte vorzugsweise für Gastronomie und Hotellerie, die sich mit ihren Qualitätsmerkmalen und der eingesetzten Technik vom Wettbewerb und erst recht von Sonnenschirmen aus dem Baumarkt deutlich abheben.
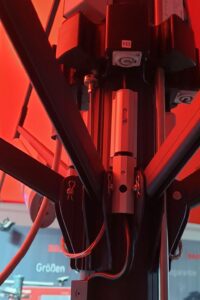
Hervorgegangen ist Bahama aus der Becher Textil- und Stahlbau GmbH, die 1950 mit der Herstellung von Planen für Lastwagen und Zeltdächer für das Schaustellergewerbe angefangen hatte. Großschirme stehen seit den 80er-Jahren im Mittelpunkt, das Know-how für Sonnensegel holte sich Bahama 2018 mit in Haus. In Reichshof sind 75 Mitarbeiter tätig.
Sonnenschirme im Windkanal
Die robusten, langlebigen Schirme spenden nicht nur Schatten sondern bieten auch Schutz vor Wind und Wetter. Um eine Windgarantie geben zu können, hat Bahama sie bei Mercedes-Benz im Windkanal getestet. Das Ergebnis: Stationär montierte Schirme können nahezu das ganze Jahr über offen bleiben und halten Windgeschwindigkeiten von bis zu 130 km/h stand.
Die kleinsten Sonnenschirme von Bahama messen 2 x 2 m, die größten decken mit 12 x 12 m eine Fläche von über 140 Quadratmetern ab. Pro Jahr stellt Bahama mehrere tausend Schirme her, Tendenz steigend. Kunden finden sich weltweit, vor allem in Ländern mit viel Sonnenschein. Die meisten Schirme bleiben aber in Deutschland. Am häufigsten verkauft sich der 4 x 4 m große Jumbrella.
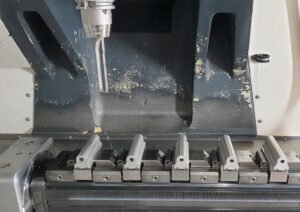
Ein Schirm setzt sich je nach Typ aus 150 bis 180 Einzelteilen zusammen. Gut 80 Prozent davon sind Aluminiumbauteile, die das Unternehmen auf sieben CNC-Maschinen drei- oder vierachsig bearbeitet. Stahl, Edelstahl und Kunststoff machen einen geringen Anteil aus. Die Hauptsäule in der Mitte und die Streben sind aus Stranggussprofilen gearbeitet. Das Material ist keine Massenware, sondern wird mit speziellen Werkzeugen eigens für Bahama gepresst. Grund dafür sind spezielle Funktionen, die der Hersteller in den Bauteilen integriert.
Wer beim Begriff „Vollausstattung“ nur an den Autokauf denkt, hat die Zubehörliste von Bahama noch nicht gesehen. Von Seitenwänden und Diebstahlsicherung ist über LED-Beleuchtung, Heizstrahler, WLAN, USB-Ladebuchsen und Lautsprecher bis hin zum TV-Bildschirm fürs Public Viewing alles möglich. Die Wunschkonfiguration liefert Bahama bereits ab einer Stückzahl von einem Schirm.
Werkzeuge statt neuer Maschine
Die Verbindung zum Werkzeughersteller INGERSOLL kam eher zufällig zustande. Als eine neue Maschine für die Zerspanung gekauft werden sollte, bestand die Möglichkeit, sich das entsprechende Modell zuvor im INGERSOLL TechCenter in Haiger anzuschauen. Der Maschinenkauf wurde zwar vorläufig zurückgestellt, doch dabei kamen die Techniker von Bahama in Kontakt mit den Werkzeugspezialisten von INGERSOLL, für die auch schnell eine Aufgabe gefunden war.
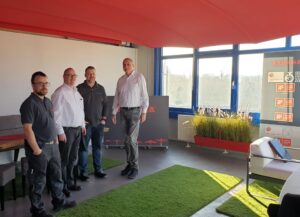
„Beim Zerspanen eines bestimmten Bauteils hatten wir immer wieder Probleme und fragten daher bei INGERSOLL nach, ob mit einem Sonderwerkzeug die Bearbeitungszeit verkürzt, vor allem aber die Prozesssicherheit erhöht werden kann“, berichtet Sven Altmann, Leiter CNC / Schlosserei bei Bahama. Das 84 mm lange Aluminiumteil dient als Haltekonsole für einen elektrischen Schalter. Er schaltet mit einer Gleitbuchse beim Öffnen und Schließen des Schirms die LED-Beleuchtung automatisch ein und aus. Für jeden Schirm mit Licht werden vier dieser Elemente verbaut. Ursprünglich hat Bahama das Bauteil mit drei HSS-Werkzeugen gefertigt und stieg dann auf Hartmetallfräser um. Die Ergebnisse blieben aber unbefriedigend.
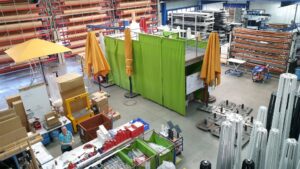
„Da Reichshof nicht weit von Haiger entfernt ist, haben wir uns das einfach mal vor Ort angeschaut“, erklärt Christopher Hees, Anwendungstechniker bei INGERSOLL. Der Rohling für das Bauteil wird von einer Profilstange heruntergesägt. Je nach Charge kommt es beim Material zu Abweichungen von 1/10 bis 4/10 mm. Beim Stranggussprozess entstehen immer gewisse Toleranzen. Bei der überwiegenden Zahl seiner Teile kommt Bahama damit ganz gut zurecht und kann sie berücksichtigen.
Stranggussteil stellt Herausforderungen
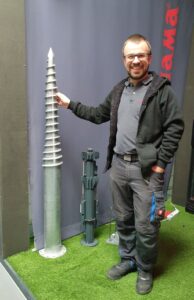
Bei dieser Haltekonsole gelang das nicht. „Bei dem Stranggussteil hatten wir oft Schwierigkeiten, genau die Mitte für die Bohrung zu finden“, erläutert Altmann. Neben der Mittigkeit der 72 mm tiefen Bohrung mussten auch enge Passmaße eingehalten werden. Hinzu kamen Probleme mit der Prozesssicherheit, da hier ein unterbrochener Schnitt verlangt war. Die Bohrung verläuft durch ein bereits vorhandenes Langloch, das an der fertigen Komponente später einen Gewindestift zur Führung des Schalters aufnimmt.
Von dem relativ aufwändig herzustellenden Bauteil produziert Bahama mehrere Tausend Stück pro Jahr. Christopher Hees hat mögliche Fertigungszeiten und Werkzeugtechnologien miteinander verglichen und kam zu der Einschätzung, dass sich dafür der Einsatz eines Sonderwerkzeugs rentiert. Nach einigen Überlegungen wählte INGERSOLL ein Tool mit einem Träger aus Vollhartmetall, eingelöteten PKD-Schneiden und langen Führungsleisten.
Johannes Post, Produktmanager PKD-CBN bei INGERSOLL, erläutert die Bedeutung des Systems für die Prozesssicherheit: „Das Werkzeug ist mit einer geringfügig ausgeführten Verjüngung versehen. Wenn es in den unterbrochenen Schnitt kommt, wird es immer noch ordentlich geführt im hinteren Bereich, der zuvor gebohrt wurde. Durch die Führungsleiste besteht bis zum Austritt aus dem unterbrochenen Schnitt eine sichere Führung.“
Spänebildung wird ausgebremst
Die Vorbohrung des Rohteils kann immer etwas variieren. Um dem entgegenzuwirken und möglichst wenig Radialkräfte zu bekommen, hat sich INGERSOLL für eine 180°-Schneide an der Spitze entschieden. Das Werkzeug ist als Stufenbohrer ausgeführt, der mit einer weiteren, seitlich angebrachten Schneide auch gleich einen zweiten Durchmesser erzeugt. Um bei dem Werkstoff AlMgSi05 mit seinem geringen Siliziumanteil möglichst kurze Späne zu bekommen, bedurfte es neben dem richtigen Werkzeug und den von INGERSOLL eingestellten Schnittparametern auch einer geeigneten Bearbeitungsstrategie. Mit einer Vielzahl unmerklich kurzer Stopps des Vorschubs werden die Späne immer wieder gebrochen, bevor sie Probleme verursachen können.
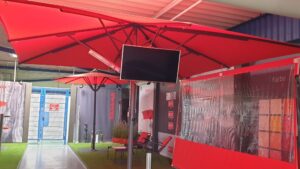
„Die Zusammenarbeit mit INGERSOLL hat uns schon in der Planungsphase gut gefallen und mit den beiden gelieferten Werkzeugen waren wir sehr zufrieden“, versichert Sven Altmann. Hatte man mit dem zuvor eingesetzten Hartmetallwerkzeug zweieinhalb Minuten pro Bohrung benötigt, so ist das Bauteil jetzt in knapp 20 Sekunden fertig. Der Zugewinn an Prozesssicherheit ist Bahama auch deshalb wichtig, weil auf der DMG CMX 1100 V immer gleich 16 Teile aufgespannt und nacheinander bearbeitet werden. Würde zu Beginn ein Werkzeug brechen, wären auch die restlichen Teile Ausschuss.

Obwohl der Bedarf an diesen Bauteilen sehr groß ist, fertigt Bahama immer nur Losgrößen von maximal 500 Stück. Die Fertigung setzt hier auf einen kontinuierlichen Prozess, um die Teileversorgung für alle Schirme zu gewährleisten. Fast täglich sind daher andere Bauteile auf den Maschinen. Die eigene Teilefertigung macht es möglich, bei Bedarf zwischendurch auch Ersatzteile für ältere Produkte herzustellen. Oft werden die Sonnenschirme des Unternehmens jahrzehntelang genutzt.
Gut möglich, dass die Fertigung zu einem passenden Zeitpunkt vom Profil- auf Vollmaterial umsteigt. Manche anderen Teile werden bereits heute aus Aluminiumklötzen gefräst. Der Stufenbohrer könnte auch nach einer Umstellung weiter benutzt werden. Sven Altmann kann sich vorstellen, in der Produktion zukünftig noch weitere Sonderwerkzeuge von INGERSOLL einzusetzen – um die bestehende Fertigung noch weiter zu optimieren oder um bei neu entwickelten Produkten gleich mit einer optimalen Bearbeitung an den Start zu gehen.
Kontakt: