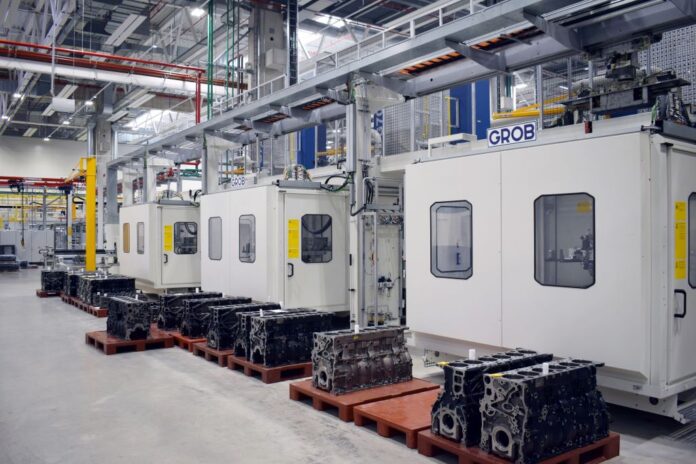
MAN hat Anfang 2025 in Nürnberg eine Motorenfertigungslinie für den klassischen 6-Zylinder eröffnet. Die Produktion von Zylinderköpfen, Zylinderblöcken und Nockenwellen in Fertigungsanlagen, die rund 100 Werkzeugmaschinen umfassen, ist effizient automatisiert verkettet und auf hohe Taktraten sowie maximale Präzision ausgelegt. Die komplexen Fertigungsprozesse – von der Minimalmengenschmierung über Trockenstaub bis zur Nassbearbeitung (KSS) stellen dabei hohe Anforderungen an die Filtertechnik. Absolent Air Care GmbH installierte insgesamt 14 Absauganlagen mit vollständiger Verrohrung und einer Gesamtleistung von 104.000 m³/h zur Absaugung und Filtration der Aerosole.
Der Standort Nürnberg ist das Kompetenzzentrum für Antriebstechnologie des weltweit führenden Herstellers von Nutzfahrzeugen. Hier werden Motoren und auch Antriebskomponenten für die konzerneigenen Lkw und Busse gefertigt. Darüber hinaus bedient die Antriebssparte externe Kundenanwendungen mit leistungsstarken Motoren wie dem V12 für Blockheizkraftwerke, maritime Einsätze und den Agrarsektor.
Mit einem starken Fokus auf Zukunftstechnologien entsteht am Standort derzeit eine Batteriefabrik, die künftig bis zu 100.000 Batteriepacks jährlich für die eigenen Nutzfahrzeuge produzieren wird. Neben der Fertigung ist Nürnberg auch Forschungs- und Innovationszentrum für Antriebstechnik. Aktuell bildet der 6-Zylinder-Reihenmotor das Hauptgeschäft. Für die Fertigung der Kernkomponenten des künftigen D30 Motors wurde eine moderne Fertigungsinfrastruktur geschaffen, inklusive einer neuen Produktionshalle.
Moderne Fertigung mit Fokus auf Präzision und Kapazität
Das hochmoderne Gebäude umfasst 15.000 m² Fläche für dieProduktion von Zylinderköpfen, Zylinderblöcken und Nockenwellen. Fertigungsprozesse und Linienbearbeitung wurden in Zusammenarbeit mit GROB definiert und anschließend vor Ort umgesetzt. Die Produktionslinien sind effizient verkettet und auf maximale Präzision ausgelegt. Zylinderköpfe und -blöcke werden fast ausschließlich auf GROB-Maschinen bearbeitet, wobei die Rohteile aus der Gießerei bei Scania von Schweden angeliefert werden.
„Unsere Fertigungslinien sind hochautomatisiert – vom Logistikkonzept und dem Zufluss der Rohteile bis hin zur Produktion der Fertigteile“, so Fabrikplanungsexperte Johannes Weiss.
Motorenfertigung hochautomatisiert
Absaugung hatte, wurde in der neuen Motorenfertigung bewusst auf zentrale
Absaugstränge gesetzt. Dies erleichtert die Wartung und verbessert die Zugänglichkeit. Bild: PRX
In der modernen Produktionshalle sind rund 100 Maschinen im Einsatz. Die Gussrohteile werden vollautomatisch an die Linien angeliefert, von Paletten entnommen und mit Linearportalladern den GROB-Maschinen zugeführt. Die Linien integrieren zudem Waschtechnik und Montagestationen, an denen beispielsweise Komponenten in Zylinderköpfe und Motorblöcke eingepresst werden. Die Fertigung ist außerdem ergonomisch eingerichtet: Alle drei Linien sind U-förmig angeordnet, um kurze Wege für das Bedienpersonal zu gewährleisten und eine direkte Kommunikation zu ermöglichen. Dabei besteht die Hauptaufgabe der Mitarbeitenden in der Qualitätssicherung und Störungsbeseitigung. In der Fertigung beginnt der Prozess mit der Bearbeitung von Gussrohlingen. Zunächst werden Referenzpunkte gefräst, um die Bauteile für die weiteren Schritte in der Produktion spannbar zu machen. Anschließend durchlaufen die Komponenten die hochautomatisierten und verketteten Transferlinien. Die Anlagen
des schwedischen Herstellers sind für die Luftfiltration und Absaugung in der neuen Fertigungshalle im Einsatz.
Absaugspezialist mit MAN-Erfahrung
Bereits 2018 hatten die Luftreinhaltungsexperten der Absolent Deutschland eine erste Fertigungslinie bei MAN in Nürnberg mit Lüftungstechnik versorgt. Damals war Maschinenhersteller GROB als Generalunternehmer auch für das Absaugsystem zuständig. Schon in dem ersten gemeinsamen Projekt konnte Absolent den Nutzfahrzeughersteller durch die herausragende Qualität seiner Filteranlagen überzeugen.
Dies bestätigt die Leistungsfähigkeit und Effizienz der Absolent-Lösungen im anspruchsvollen industriellen Einsatz. Die Systeme garantieren eine zuverlässige Filtration nach H13-Standard und zeichnen sich durch ihre außergewöhnlich lange Standzeit aus. „Prinzipiell war es dasselbe Konzept, nur in einer wesentlich größeren Dimension und unser Auftraggeber war direkt MAN“, betont Hartmut Enderle, Vertriebsleiter bei der Absolent Air Care GmbH in Sprockhövel.
Hierbei übernahm Absolent als Generalunternehmer die Planung, Lieferung und Montage von insgesamt 14 Absauganlagen mit Filtertechnik. Während des gesamten Projekts arbeiteten die Teams von MAN und Absolent eng zusammen, um alle Anforderungen zu erfüllen und individuelle Lösungen zu entwickeln.
„Besonders haben wir die Flexibilität seitens Absolent bei der Anpassung an unsere spezifischen Herausforderungen und die reibungslose Kommunikation geschätzt, was bei solchen Mammutprojekten keineswegs immer der Fall ist“, erläutert Manfred Fries, der als Fabrikplaner bei MAN Truck & Bus über viele Jahre an Erfahrung verfügt.
Mammutprojekt im Griff
Ein solches Mammutprojekt benötigt natürlich seine Zeit. Bereits 2022 hatte der Nutzfahrzeughersteller deshalb bei Absolent Deutschland wegen Absaugtechnik angefragt. MAN plante damals in Nürnberg eine letzte Motorenfertigungslinie für den klassischen 6-Zylinder, weitere Linien waren parallel bei Scania in Schweden und in Brasilien geplant, eine weitere soll noch in den USA folgen.
„Bereits in anderen Produktionshallen hatten wir Absolent-Absauganlagen im Einsatz und schätzten die langen Wartungsintervalle zwischen den Filterwechseln – ein entscheidender Faktor, der zur erneuten Wahl von Absolent führte“, erinnert sich Manfred Fries an den Planungsprozess. Geplant war, in Nürnberg 16 Fertigungslinien mit Absaugtechnik auszustatten. „Das Lastenheft umfasste mehrere Hundert Seiten von Filter- und Absaugtechnik über Anlagensteuerung bis zum letzten Rohranschluss“, weiss Hartmut Enderle noch genau.
Dabei wurden mehrere GROB-Maschinen zu sogenannten Insellösungen usammengefasst; die kleinste Insel mit einer erforderlichen Absaugleistung von 4.000 Kubikmetern, die größte mit aktuell 12.000 Kubikmetern. „Schließlich konnten wir die Fertigungsplanung nochmals optimieren, sodass insgesamt 14 Absauganlagen installiert wurden“, präzisiert Hartmut Enderle. Durch zentrale Absaugstränge anstelle einzelner Maschinenabsaugungen wurde die Wartungsfreundlichkeit zusätzlich deutlich verbessert. „Eine lange Standzeit der Filter und die überzeugende CO₂-Bilanz unterstreichen die Nachhaltigkeit der Lösung“, ist der MAN-Experte überzeugt.
Effizient abgesaugt
In der neuen Antriebsfertigung setzt MAN auf maßgeschneiderte Absaugtechnik, um den unterschiedlichen Anforderungen der Bearbeitungsprozesse gerecht zu werden. Zunächst kommen verschiedene Schmier- und Bearbeitungssysteme zum Einsatz – von der Trockenbearbeitung, bei der hauptsächlich Staub entsteht, über Minimalmengenschmierung (MMS) bis hin zur Nassbearbeitung mit Kühlschmierstoffen (KSS).
Gleichzeitig sorgt bei der Grobzerspanung (Schruppbearbeitung) die Kühlung des Maschinenbetts dafür, dass Wärme über den Kühlschmierstoff effizient abgeführt wird und die Prozessgenauigkeit stabil bleibt. Das Kühlsystem basiert auf einer zentralen Anlage, die KSS mit konstanten Temperaturen bereitstellt, um gleichbleibende Bedingungen an den Bearbeitungszentren sicherzustellen. „Das ist entscheidend für die Qualität, Prozesssicherheit und hohe Taktzeiten“, betont Fabrikplaner Fries. Besonders bei Minimalmengenschmierung (MMS), bei der feine Ölnebel mit Partikelgrößen unter 1 μm entstehen, sind die Anforderungen an die Filtertechnik besonders hoch. Hier kommt die A.smoke-Serie von Absolent zum Einsatz, die speziell für die Filtration feinster Ölpartikel entwickelt wurde.
Absauganlagen: „Wir haben an MAN 14 Absauganlagen, einschließlich Filtertechnik
und kompletter Montage mit Verrohrung, geliefert. Es war das größte Projekt in der
Geschichte unseres Unternehmens.“ Bild: PRX
Bei der klassischen Nassbearbeitung mit Kühlschmierstoffen (KSS) setzt MAN hingegen auf die Mist-Serie, die für die gängigsten Emulsionsnebel ausgelegt ist. Absolent-Absaugspezialist Hartmut Enderle erläutert: „Wir garantieren eine Standzeit von einem Jahr im Drei-Schicht-Betrieb. Da kann man nicht einfach einen Filter für alle
Zerspanungsaufgaben verwenden. Sollte es zu Abweichungen kommen, können wir die Filtermedien immer anwendungsspezifisch anpassen.“ Während der Inbetriebnahme werden die Filter anhand von Messwerten geprüft und gegebenenfalls optimiert. Austausch und Wartung der Filter können direkt vor Ort während der Instandhaltung übernommen werden. Für die Absaugtechnik spielte schließlich die Aerosolbelastung der unterschiedlichen Bearbeitungsprozesse eine zentrale Rolle. Nach den von GROB definierten Vorgaben wurde mit Absolent eine passgenaue Lösung erarbeitet: Die Absauganlagen arbeiten mit getrennten Filtersystemen, um die unterschiedlichen Arbeitsprozesse voneinander zu trennen. Das optimiert die Filtration und stellt eine saubere sowie effiziente Fertigungsumgebung sicher.
Optimale Verrohrung mittels 3D
Eine maßgeschneiderte Verrohrung minimiert Energieverluste, indem weite Wege vermieden werden. Die 3D-Planung und optimierte Verrohrung waren ebenfalls entscheidend, um eine präzise und effiziente Verlegung der Rohrleitungen sicherzustellen. Hierfür hat das Planungsteam von Absolent Step-Dateien von GROB erhalten, die zur Auslegung der einzelnen Linien in die 3D-Software integriert wurden. Im Vorfeld wurden alle Rohrverläufe detailliert in 3D geplant und aufeinander abgestimmt, bevor die Beauftragung erfolgte. Durch den Einsatz von Frequenzumrichtern und eine durchdachte Auslegung der Verrohrung, unter anderem durch Abzweige mit einem Winkel von weniger als 45 Grad anstelle von T-Stücken, konnte eine optimale Strömungstechnik erreicht werden. Auch die Platzierung der Filteranlagen wurde bereits in der Projektierungsphase in enger Abstimmung zwischen MAN und Absolent definiert.
Ziel war es, die Absaugung möglichst nah an der Entstehungsquelle zu positionieren, um lange Verrohrungswege zu vermeiden. Dies reduzierte zusätzliche Druckverluste und minimierte somit effektiv die Energieverluste. Hartmut Enderle erklärt das Vorgehen: „Wir haben das gesamte Rohrlayout im Vorfeld in 3D geplant und die Verrohrung schrittweise dimensioniert – ähnlich wie bei Wasserleitungen im Hausbau. Je mehr Maschinen an die Hauptleitung angeschlossen sind, desto größer muss der Rohrquerschnitt sein, um einen
gleichbleibenden Volumenstrom und geringen Energieverbrauch zu gewährleisten.“
Insgesamt wurden für die 14 Absauganlagen 700 Meter Rohrleitungen verlegt, die ein Gesamtvolumen von 104.000 m³/h absaugen. Die Anlagen selbst verfügen über Kapazitäten zwischen 4.000 und 12.000 m³/h. Anhand des 3D-Layouts konnten schließlich die benötigten Rohrteile, Anschlüsse, Dichtmanschetten und andere Komponenten bestellt sowie der Montageaufwand exakt geplant werden. Bei der Auswahl der Systeme wurde besonderer Wert auf hochwertige Materialien gelegt. Beispielsweise wurden keine Wickelfalzrohre verwendet, da diese langfristig zu Leckagen führen könnten. Energieeffiziente Industrie-Absaugung: 50% weniger Verbrauch „Eine optimale Absaugtechnik ist für uns außerordentlich wichtig. Die durchdachte Lösung von Absolent erfüllte all diese Anforderungen und passte zudem perfekt zu unserer Vision von Effizienz und Nachhaltigkeit“, erklärt Fabrikplaner Manfred Fries.
So lag der Fokus weniger auf den Investitionskosten, sondern vielmehr auf den Energiekosten und der Lebensdauer der Anlagen. Absolent habe ihn mit technischem Know-how, innovativer Filtertechnik und einer außergewöhnlichen Wartungsfreundlichkeit überzeugt. Ausschlaggebend für die Wahl der Absaugtechnik waren neben der hohen Energieeffizienz (50 % weniger Energieverbrauch als ursprünglich erwartet) auch die Lebenszykluskosten (TCO). Bei der Betriebsübergabe wurden die prognostizierten Energieverbrauchswerte detailliert überprüft.
Zudem tragen die langlebigen H13-HEPA-Filter dazu bei, die Betriebs- und Wartungskosten über den gesamten Lebenszyklus hinweg zu minimieren. Ein wesentlicher Aspekt ist außerdem die Integration intelligenter Steuerungstechnik. Sobald eine Maschine außer Betrieb ist, schließt sich automatisch eine Abluftklappe, wodurch der Unterdruck ansteigt und die Absauganlage ihre Leistung reduziert. „Diese Regelungstechnik sorgt dafür, dass die Absaugleistung immer optimal bleibt und gleichzeitig die Filterstandzeit verlängert wird“, erklärt Manfred Fries. Ein weiteres Highlight ist die Wärmerückgewinnung der Filteranlagen. Während im Sommer die warme Abluft nach außen geführt wird, nutzt MAN im Winter die aufbereitete Abluft zur Hallenbeheizung. Das spart nicht nur Energie, sondern verbessert auch das Raumklima.
Ein besonderes Augenmerk liegt zudem auf der Luftqualität in der Fertigungshalle. Die H13-HEPA-Filter stellen sicher, dass keine Mikropartikel in die Umluft gelangen, wodurch der Schutz der Mitarbeitenden gewährleistet wird. Gleichzeitig verhindert die saubere Fortluft Ablagerungen in den Wärmetauschern, die langfristig zu einem schleichenden Wirkungsgradverlust führen könnten. „Mit absolut sauberer Luft verhindern wir diesen Effekt und sichern die Effizienz der gesamten Anlage“, ergänzt Hartmut Enderle.
Lärmschutz nicht vergessen
Auch der Lärmschutz war ein wesentlicher Aspekt bei der Planung. Schallmessungen ergaben, dass an allen Messpunkten die geforderten 65 Dezibel unterschritten wurden. Neben der technischen Umsetzung spielte die Bedienerfreundlichkeit der Anlagen eine große Rolle. Schulungen für das Instandhaltungspersonal stellten sicher, dass Wartungsarbeiten und Filterwechsel effizient durchgeführt werden können. Der letzte Meilenstein war Ende November die interne Abnahme und Inspektion.
„Gemeinsam mit allen Betreibern, der Instandhaltung und natürlich unseren Experten für Arbeitssicherheit und Umweltschutz haben wir die neue Fabrikanlage inspiziert, so dass wir im Januar 2025 den Echtbetrieb aufnehmen konnten“,
zeigt sich Manfred Fries zufrieden mit dem gelungenen Projekt. Und das Fazit: Dank der durchdachten Kombination aus Layout-Planung, intelligenter Steuerung und angepasster Filtertechnik konnte MAN die Energieverbräuche signifikant reduzieren und die Prozesse gleichzeitig stabil und effizient gestalten.
Zusammenfassend lässt sich sagen, dass MAN durch präzise Planung, hochwertige Absaugtechnik und effiziente Wärmerückgewinnung eine zukunftsweisende Antriebsfertigung geschaffen hat, die sowohl die Gesundheit der Mitarbeitenden schützt als auch die eigenen Nachhaltigkeitsziele erfüllt.
Kontakt: