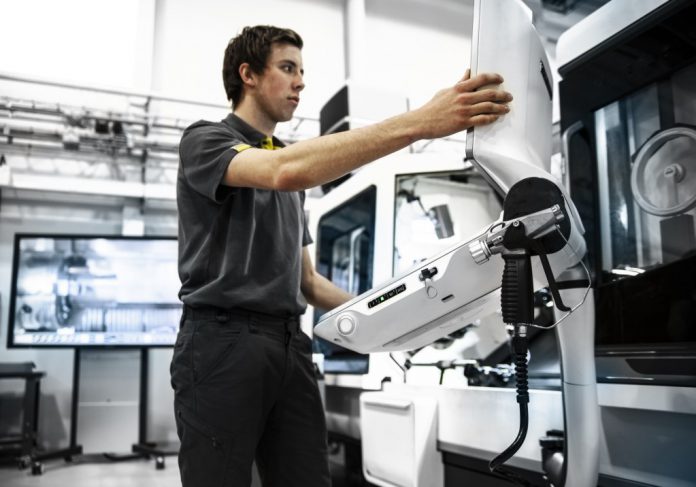
In vielen Industriebereichen wird die Erhebung und Nutzung von Daten zum Zweck der Optimierung längst als Mittel der Wertschöpfung angesehen. Auch in der Fertigungsindustrie wird die Technologie intensiv genutzt – insbesondere für die Überwachung des Bearbeitungsprozesses. Durch zunehmende Konnektivität und die Möglichkeit, Daten zu visualisieren und mit anderen Anwendern zu teilen, kann die Technologie nun auf ein neues Level gehoben werden.
Bislang war es möglich, einzelne Maschinen zu überwachen. Im nächsten Schritt können die erhobenen, detaillierten Prozessdaten mit anderen geteilt werden, sodass Vergleiche und Bewertungen möglich werden. Das heißt: Wir können der Werkzeugmaschine “zuhören“, Daten sammeln und interpretieren sowie visualisieren, was in der Maschine passiert: Ist das Werkzeug verschlissen? Ist der Prozess zu schnell bzw. zu langsam? Gibt es unerwartete Abweichungen? Auf diese Weise können Fehler erkannt und sofort korrigiert werden. Außerdem kann der Bearbeitungsprozess so lange verbessert werden, bis der optimale Zustand erreicht ist.
Lange Zeit herrschte der Silo-basierte Ansatz mit einem einzelnen Prozessüberwachungssystem pro Maschine vor – ohne Konnektivität und ohne die Möglichkeit, das System bei Bedarf aufzurüsten. Nach Ansicht von Sandvik Coromant ist es jedoch notwendig, Maschinen miteinander zu verbinden, zumal die Überwachung der Bearbeitungsprozesse eine wichtige Rolle bei der Interaktion mit der Werkzeugmaschine spielt. Bei vernetzten Maschinen können sämtliche Upgrades hinsichtlich der Überwachungssysteme nahtlos über die Cloud oder das Firmennetzwerk installiert werden.
Mit diesem Grad an Konnektivität, mit der Fähigkeit, Daten zu teilen und mit einem skalierbaren Ansatz zur Bearbeitungsüberwachung verfügen Fertigungsunternehmen über eine Lösung für viele Probleme. So können sie unter anderem ungeplante Ausfallzeiten infolge unerwarteter Kollisionen reduzieren, Werkzeug- und Reparaturkosten durch die Überwachung von Werkzeugüberlastung oder Werkzeugbruch senken sowie Leerlaufzeiten aufgrund fehlender Werkzeuge verhindern. Gleichzeitig können sie erhebliche Produktivitätssteigerungen erzielen und profitieren von einer gleichbleibenden Qualität der Komponenten. Überdies erhalten sie präzisere Set-up-Limits für Werkzeuge. Diese Vorteile tragen dazu bei, die herkömmliche Prozessüberwachung maßgeblich zu erweitern und zu verbessern.
Vielfältige Technologien und Fertigungssysteme
Um Produktivität, Sicherheit und Qualität mithilfe der Prozessüberwachung zu steigern, müssen Anwender eine Vielzahl von Technologien einsetzen. Zum einen, um die verschiedenen Aspekte des Bearbeitungsprozesses zu überwachen, zum anderen, um mehrere Systeme miteinander zu verbinden – inklusive unterschiedlicher Netzwerkgeräte, Software- und Cloud-Lösungen etc. Ein derart hohes Maß an Konnektivität erfordert entweder eine vollständige Standardisierung der Verbindungen – die es derzeit noch nicht gibt – oder ein sehr hohes Integrationslevel.
Unabhängig davon, ob vollkommen störungsfreie Produktionsprozesse irgendwann Wirklichkeit werden, verschiebt Sandvik Coromant mit seinen neu entwickelten Systemen bestehende Grenzen. Die Lösungen des schwedischen Werkzeugherstellers ermöglichen es Fertigungsunternehmen, mithilfe der Bearbeitungsüberwachung und einer effektiven Datennutzung Wettbewerbsvorteile zu erzielen. Dank seines Erfahrungsschatzes in puncto Werkzeugtechnologie kann Sandvik Coromant bei der Definition und Überwachung von Grenzwerten für Werkzeuge oder Bearbeitungszyklen unterstützen, sodass Anwender nicht selbst aktiv werden müssen – ein echter Mehrwert im Überwachungsprozess.
Wer hat die exaktesten, schnellsten Reaktionszeiten und gleichzeitig die geringste Anzahl von Fehlalarmen während des Produktionsprozesses? Das ist ein wichtiges Differenzierungsmerkmal in der wettbewerbsintensiven Fertigungsindustrie. Denn das Anhalten des Bearbeitungsprozesses ohne begründeten Anlass verursacht enorme Kosten. Dennoch war dies bei der Metallbearbeitung alltäglich, weil Algorithmen zur Interpretation der Maschinensignale fehlten.
Um Signale innerhalb von Millisekunden sammeln und interpretieren zu können, bedarf es vieler Fähigkeiten – in der Regel muss dies der Anwender übernehmen. Doch selbst wenn er über genügend Expertise verfügt, um seine Prozessüberwachung auf eine höhere Stufe zu bringen, bedarf es jahrzehntelanger Erfahrung, um zu verstehen, wo die Grenzwerte überhaupt liegen.
Echtzeitüberwachung und Nachhaltigkeit
Ein Mehrwert der Bearbeitungsüberwachung ist die Möglichkeit, Werkzeuge bis zum individuellen Standzeitende zu nutzen, was wiederum die Qualität der Komponenten erhöht und die Durchlaufzeiten verkürzt. Ein weiterer Vorteil ist, dass der Energieverbrauch reduziert wird – das macht Echtzeit-Prozessüberwachung zu einer umweltverträglichen Technologie. Gleichzeitig profitieren Anwender dank einer verbesserten Kontrolle von geringeren Kosten.
Ohne solch ein hohes Kontroll-Level kann es im Bearbeitungsprozess leicht zu Störungen kommen, beispielsweise zu falschen Werkzeugkorrekturwerten, falschen Bauteilmaßen oder zu einer inadäquaten Werkzeugwechselposition. Diese wiederum können zu Energie- und Ressourcenverschwendung führen. Lose gespannte Bauteile, eine falsche Bauteilausrichtung, eine ungeeignete Programmauswahl, unentdeckter Werkzeugbruch oder falsche Werkzeugmaße können ebenfalls Probleme verursachen. Gelingt es, eines dieser Probleme zu beheben, wird sich die Produktivität unweigerlich verbessern. Gelänge es, all diese Schwierigkeiten zu beseitigen, wäre dies ein Quantensprung in puncto Effizienz.
Eine permanent hohe Prozesskontrolle löst nicht nur Probleme, sie erhöht auch Prozesssicherheit sowie Bauteilqualität und ermöglicht einen optimalen Werkzeugeinsatz ohne vorzeitige Werkzeugwechsel. Ein System zur Prozessüberwachung stellt sicher, dass das richtige Werkzeug zur Stelle ist, dass es nicht defekt ist und dass der Prozess innerhalb der korrekten Parameter abläuft. Das System nimmt bei Bedarf Korrekturmaßnahmen vor, sendet Warnmeldungen, um Verschleiß und Bruch zu vermeiden, und stoppt den Bearbeitungsvorgang, wenn ein Werkzeug bricht oder fehlt. Das reduziert den Ausschuss – was aufgrund der kostspieligen Materialien insbesondere in Branchen wie der Luftfahrtindustrie enorm wichtig ist.
Basierend auf maschinenseitigen Prozessüberwachungsdaten können Anwender Kollisionen vorhersagen und vermeiden sowie auf Basis gewonnener Verschleißinformationen die Wartungskontrolle verbessern – für eine erhöhte Lebensdauer der Maschinenteile. Die Überwachung auf Komponentenebene hilft, eine gleichbleibende Qualität der gefertigten Bauteile zu erreichen. Die Werkzeugüberwachung ermöglicht eine optimale Werkzeugnutzung, präzisere Prognosen zu den Kosten pro Bauteil sowie eine korrekte Bestandssteuerung. Zudem bewirkt sie eine höhere Maschinenauslastung.
Schlussfolgerung
In der Metallbearbeitung gehören geringe Prozesssicherheit sowie suboptimale Bauteilqualität und Werkzeugnutzung bald der Vergangenheit an. Denn die kontinuierliche Prozesskontrolle durch Bearbeitungsüberwachung bringt mehr Effizienz und reduziert so die Kosten. Die Überwachung des Werkzeugzustands trägt ebenfalls zu einer optimalen Werkzeugnutzung sowie zur korrekten Erfassung der Werkzeugverbräuche zum Zwecke einer richtigen Bestandsplanung bei. So ermöglicht sie eine genauere Vorhersage der Komponentenkosten sowie eine höhere Maschinenauslastung.
Indem ungeplante Maschinenstopps minimiert werden, ermöglicht Sandvik Coromants Ansatz zur Prozessüberwachung eine 85-prozentige Maschinenauslastung. Gleichzeitig kann mit Sandvik Coromants Machine-Learning-Verfahren eine Zerspanungseffizienz von 95 Prozent erzielt werden. Zum Vergleich: Bei der konventionellen Fertigung werden meist nur 80 Prozent erreicht.
Wie bei vielen anderen Fertigungsprozessen gibt es auch bei der Zerspanung inhärente Ursachen für Instabilität. Doch dagegen wirkt die Überwachung des Zerspanungsprozesses. Sie ermöglicht den Anlagenbetreibern, zu „hören“, was im Bearbeitungsprozess geschieht und detailliert zu überprüfen, ob alles planmäßig läuft und ggf. korrigierend einzugreifen.
Indem sie Instabilität auf ein absolutes Minimum reduziert, wird die Überwachung des Zerspanungsprozesses zum Katalysator für signifikante Veränderungen in der verarbeitenden Industrie.
Kontakt: