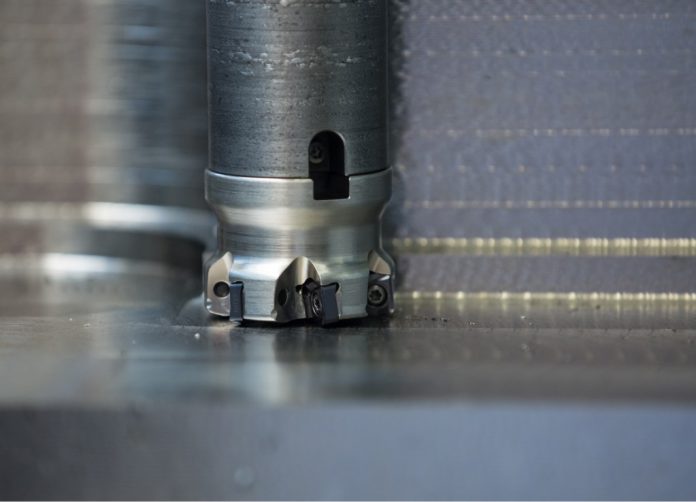
Von Maschinenteilen und entsprechenden Baugruppen, Vakuumtechnik zur Display-Beschichtung, Forschung und Entwicklung von Elektronenbeschleunigern, über Straßenbahnschienen oder Achterbahnen bis hin zu Aufträgen für die Luft- und Raumfahrt sowie die Kerntechnik – sämtliche Märkte bedient Kinkele in Sachen Schweißbau, Zerspanung, Lackierung und Montage oder gleich alles zusammen.
„Sollten wir einen Auftrag ablehnen müssen, dann scheitert es höchstens am Gewicht von maximal 60 Tonnen oder der Größe – keinesfalls an den Materialien oder der Bearbeitung. Dafür sind unsere Mitarbeiter viel zu versiert in den unterschiedlichsten Werkstoffen, seien es Norm- oder Edelstähle, Guss oder Duplexwerkstoffe“, erläutert Ernst Bayer, Leiter Auftragsleitstand bei der Kinkele GmbH & Co. KG.
Arbeit für Mutige
Eine intensive Ausbildung wird bei Kinkele besonders gepflegt, was 60 Azubis bei knapp 400 Mitarbeitern belegen – und das nicht ohne Grund. Dazu Hermann Stegmaier, Werkzeugtechnologe bei Kinkele: „Bei uns stehen die jungen Leute an einer Maschine, die schon per se eine Million kostet, und sollen dann Bauteile bearbeiten, die einen Werkstoffwert von 60.000 bis 100.000 Euro haben. Da ist eine Menge an Selbstvertrauen, Verantwortung und Qualifikation vom Mitarbeiter gefragt!“
Schneller zum Span
Ernst Bayer und Hermann Stegmaier kalkulieren, wie viel Zeit und Material für die meist Einzelaufträge oder Kleinserien angesetzt werden müssen: „Im Vorfeld wenden wir uns an die Werkzeughersteller, welche Tools sie für die jeweilige Bearbeitung vorschlagen. Um die Hauptzeiten stetig zu reduzieren, suchen wir seit rund einem Jahr noch intensiver unsere Zulieferer aus.“
Unter anderem hat die Einführung des Hochvorschubfräsens (HPC = High Performance Cutting) der Zerspanungsabteilung enormen Antrieb verschafft. „Gerade als wir unsere Zerspanungsstrategien mit klassischem Planfräsen und Rundplatten auf den Prüfstand gestellt hatten, kam ein Vertriebsmitarbeiter von Tungaloy mit der DoFeed-Reihe als neuem Produkt zu uns. Da wir es oftmals mit labilen Schweißkonstruktionen zu tun haben, sprach uns die Werkzeugserie zum HPC mit geringen Schnittkräften und Zustellungen von rund 1 Millimeter direkt an“, so Hermann Stegmaier.
Das Tempo-Plus, das sich durch die neue Bearbeitungsmethode erreichen lässt, überrascht die Profis immer wieder aufs Neue. „HPC ist die wirtschaftlichste Anwendung für uns. Sind wir früher in diversen Stahlsorten einen 500er Vorschub gefahren, machen wir jetzt locker zwischen 8 und 16 Meter, also teils das 30-fache! Selbst in Edelstahl können wir zwischen 3 und 8 Metern Vorschub geben“, erklärt Hermann Stegmaier begeistert.
DoFeed-Werkzeugserie bis 250 mm Durchmesser
Werkzeugdurchmesser, die in den meisten Industriesparten problemlos ausreichen, wirken bei Kinkele oftmals etwas verloren. „Herr Stegmaier regte beispielsweise an, die damaligen Größen unserer DoFeed-Reihe von maximal 100 mm auszubauen. Mittlerweile haben wir standardmäßig 125 mm, 160 mm, 200 mm und sogar 250 mm im Programm. Wir nennen das intern gerne die ‚Kinkele-Erweiterung‘“, bemerkt Markus Feldhaus, Produktmanager Bohren/Fräsen bei Tungaloy, mit einem Augenzwinkern.
Um die Material- und Bearbeitungsvielfalt ideal abzudecken, kommen bei Kinkele alle möglichen Schneidstoffsorten aus dem Tungaloy DoFeed-Programm auf die Maschinen: von der Allroundsorte AH725 über AH3035 für den unterbrochenen Schnitt von Stahl bis hin zu AH130 für Titanlegierungen, rostfreien Stahl und Stahl oder AH120 für Eisengusswerkstoffe.
Hoher Vorschub, lange Standzeiten
Galten Standzeiten von beispielsweise 20 Minuten vor einiger Zeit noch als guter Standard, ist heute problemlos das Doppelte zu erreichen. „Mit HPC in normalem Stahl schaffen wir sogar schon zwei Stunden!“, so Hermann Stegmaier. Dabei seien die Schneidplatten auch weniger komplett verschlissen sondern eher durch Vibration gebrochen oder ausgebröselt. „Früher kam das bei rund der Hälfte der Werkzeuge vor. Dank qualitativ hochwertiger Ultrafeinstkorn-Substrate und optimierter Beschichtungen sind derart hohe Ausfallquoten mittlerweile Vergangenheit.“
HPC kappt die Hauptzeiten
Da bei den Rüstzeiten durch die meist extrem großen und schweren Werkstücke kaum Zeit einzusparen ist, liegt der Fokus auf optimierten Zerspanvorgängen. „Jede Maschine wird von einem Spanntechniker eingerichtet, was bereits einen Hauptteil der Vorbereitung in Anspruch nimmt – oftmals acht Stunden zum Spannen und Ausrichten. Da ist schnell eine ganze Schicht aus unserem Drei-Schicht-Betrieb weg“, erläutert Kurt Kinkele, Mitglied der Geschäftsführung bei Kinkele. Hermann Stegmaier ergänzt: „Um so wichtiger ist es, zuverlässige und leistungsfähige Werkzeuge einzusetzen, die uns den entscheidenden Zeitvorteil verschaffen.“
Einzigartiger Service von Tungaloy
Der Name Tungaloy steht bei Kinkele hauptsächlich für HPC, Schruppbearbeitung, großen Abtrag und hohes Spanvolumen – nicht zuletzt auch für Service. Kurt Kinkele betont: „Wir pflegen langjährige Partnerschaften mit unseren Kunden, aber auch mit Lieferanten! So können wir sicher sein, dass sich im Falle eines Problems innerhalb kürzester Zeit jemand vor Ort darum kümmert.“
So ist es für Jürgen Schmidt, Anwendungstechnik bei Tungaloy und seit 14 Jahren für Kinkele zuständig, normal, sogar abends in den Betrieb zu kommen oder bei Versuchen und beim Einfahren neuer Werkzeuge dabei zu sein. „Dieses Engagement ist schon außergewöhnlich und nicht bei jedem selbstverständlich“, findet Ernst Bayer.
Dirk Amend, technische Beratung & Vertrieb bei Tungaloy, hält es für wichtig zu wissen, wie Kinkele arbeitet, die Bauteile sowie das Großteilmetier zu kennen, um es erfolgreich weiterzuentwickeln. „Mit einem Schlagwort zusammengefasst: Wenn es brennt, drehen wir auf dem Heimweg für die Firma Kinkele auch mal um!“
Schon beim ersten Schuss ins Schwarze treffen
Werkzeugtests können nur am Bauteil, das auch das Endprodukt darstellt, gemacht werden. Ernst Bayer: „Anders als in der Serienproduktion müssen wir daher vom ersten Schnitt an nah am Optimum sein!“ Zu solchen Tests stellt Tungaloy oftmals ausgesuchte Werkzeuge zur Verfügung. „Eine perfekte Synergie: Indem wir unsere Werkzeuge bei Kinkele testen können, bekommen wir die Erfahrung und Kinkele somit das beste Werkzeug von uns“, so Jürgen Schmidt.
Projektvielfalt mit Zukunft
Viele namhafte Projekte in der ganzen Welt tragen die Handschrift der Kinkele GmbH & Co. KG. Unter anderem am Bau der „Pioneering Spirit“, dem mit 382 Meter Länge und 124 Meter Breite größten Arbeitsschiff der Welt war das Ochsenfurter Unternehmen beteiligt. Damit Containerschiffe die weltgrößte Hubbrücke, die Botlekbrücke im Rotterdamer Hafen, durchfahren können, wird die Brücke von 16 Seiltrommeln angehoben – gefertigt von Kinkele.
„Mit solchen Aufträgen präsentieren wir uns immer wieder als kompetente Problemlöser. Dank perfekt ausgebildeten Mitarbeitern und zuverlässigen Partnern wie Tungaloy erwarten wir mit Spannung neue Projekte. Aber wie sagte es mein Vater einmal treffend: ‚Die neue Fräsmaschine wird auf der alten Fräsmaschine hergestellt!‘“, fasst Kurt Kinkele zusammen.
Kontakt: