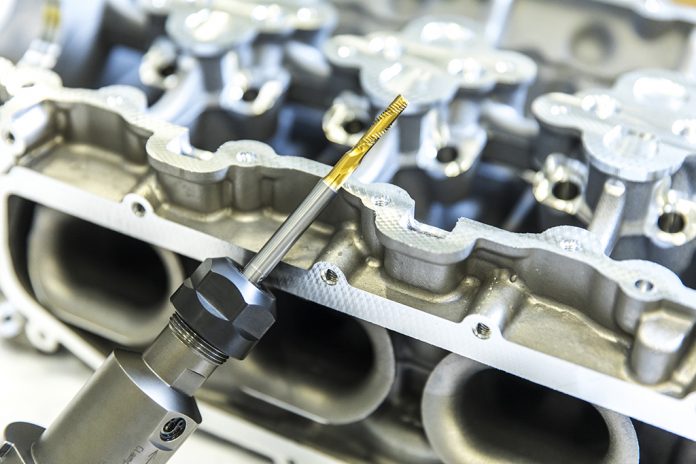
Rund zwei Millionen Antriebe und fast 165.000 Automobile hat die Audi Hungaria Zrt. im Jahr 2019 produziert. Allein 70 % der Antriebe waren Drei- und Vierzylinder-Otto- und -Dieselmotoren, die Sechszylinder-Otto- und Dieselmotoren machen zusammen circa 20 % der Fertigung aus. Die vorrangig für Sportmodelle eingesetzten Fünf-, Acht- und Zehnzylindermotoren liegen zusammen bei etwa 2 %.
Darüber hinaus stellen die elektrischen Achsantriebe mit mittlerweile 8 % einen nicht unerheblichen Teil der Produktion in Ungarn dar. Damit produzierte Audi Hungaria 2019 fünf verschiedene Otto- und drei verschiedene Dieselmotorvarianten sowie eine E-Antriebfamilie mit einem Leistungsspektrum von 63 bis 470 kW. Zu den aktuell in Györ gefertigten Modellen gehören der Audi TT Coupé und der Audi TT Roadster sowie der Audi Q3 und Audi Q3 Sportback. Seit 2019 produziert das Unternehmen die Modelle Q3 mit elektrifiziertem Antriebstrang (Hybrid-Technologie).
In neuer Linie verankert
Teil der Produktpalette von Audi Hungaria ist ein 3-Liter-V6-Benzinmotor, der zuerst im Audi S5 und RS5 eingesetzt wurde, mittlerweile aber auch im Porsche Macan, VW Touareg und diversen S- und RS-Modellen von Audi verbaut wird. Die Produktion dieses TFSI-Motors startete 2016 auf einer komplett neu konzipierten Fertigungslinie. Als ein Bearbeitungsschritt wurde in diese Fertigungsumgebung von Beginn an auch das Gewindeformen mit dem Punch-Tap-Zyklus von Emuge-Franken eingebaut.
Der Integration des Verfahrens in die neue Linie waren detaillierte Untersuchungen zum Verfahren vorausgegangen. Nachweise zur Qualität sowie zur statischen, dynamischen und Dauerfestigkeit gehörten ebenso dazu wie Untersuchungen zur Montierbarkeit und Montagefestigkeit bis hin zu den Laufeigenschaften und der Freigabe des kompletten Motors.
Spanlos und MMS-fähig gewinden
Dass Gewinde heute in Györ bevorzugt geformt werden, gehört zu den grundsätzlichen Fertigungsstrategien der Audi Hungaria Zrt. Zugleich wird im Unternehmen zunehmend mit Minimalmengenschmierung (MMS) gearbeitet. Die Hauptgründe, dass Audi die Punch-Tap-Technologie in die Linie integriert hat, waren die Spanfreiheit des Verfahrens, aber auch die Zeit- und Energieeinsparung.
Speziell beim Punch Tap kommt hinzu, dass der Werkzeugweg im Vergleich zum klassischen Gewindeformen oder -schneiden deutlich kürzer ist und so mit dem Werkzeug massiv Zeit eingespart wird. Aufgrund des kurzen Werkzeugwegs werden zudem im Gewindezyklus bis zu 90 Prozent Energieeinsparung erzielt.
200 Gewinde pro Motor
Bearbeitet werden mit dem Punch Tap die beiden Zylinderköpfe sowie das Zylinderkurbelgehäuse des V6. Beide Bauteilgruppen bestehen aus Gussaluminium, jedoch aus unterschiedlichen Legierungen. Während es sich bei den Zylinderköpfen um AlSi7Cu0,5Mg handelt, werden die Kurbelgehäuse aus AlSi8Cu3 gefertigt. Zu formen sind an Zylinderkopf und Kurbelgehäuse überwiegend M6-Gewinde. Am kompletten Motor beläuft sich ihre Zahl auf nahezu 200.
Für beide Bauteilgruppen gibt es eine separate Fertigungslinie, in die das Gewinden auf Grob-G320- und G520-Bearbeitungszentren mit Siemens-Steuerung eingetaktet ist. Wie allgemein beim Gewinden, ist hierbei eine Flankentoleranz von 6H sicherzustellen, der Gewindekern ist in 7H umzusetzen.
Beide Vorgaben werden mit dem Punch Tap sicher eingehalten, was auch für die Anforderungen an die Oberflächenqualität gilt. Dabei steht für das Formen der unterschiedlich tiefen Gewinde eine nutzbare Gewindetiefe bis zu 3 x D zur Verfügung. In jedem Fall ist das Werkzeug stabil aufzuspannen, weshalb Emuge-Franken für den Punch Tap den speziellen Werkzeughalter PT-Synchro entwickelt hat.
Neue Dimension der Produktivität
Die Punch-Tap-Technologie stellt neben dem klassischen Gewindebohren, -formen und -fräsen eine weitere originäre Technologie zur Herstellung von Innengewinden dar. Vergleicht man den Werkzeugweg des Punch Tap mit dem Weg herkömmlicher Gewindebohrer oder -former, fällt er bei einem M6-Gewinde mit 15 mm nutzbarer Gewindetiefe circa 15-mal kürzer aus. Daraus resultiert eine Zeiteinsparung im Gewindezyklus von bis zu 75 Prozent.
Der Punch Tap fährt dafür im ersten Schritt helikal in das Werkstück ein und erzeugt vor dem eigentlichen Gewinden eine Helikalnut bei simultaner Einführung des Werkzeugs auf Gewindetiefe. Im zweiten Schritt wird dann durch die spezielle Zahngeometrie über eine halbe Drehung in einem Schritt das Gewinde geformt, bevor das Werkzeug im dritten Schritt wieder herausfährt. So ergibt sich im Vergleich zu konventionellen Gewindeverfahren eine Verkürzung des Werkzeugweges um 90 Prozent.
Die letztlich realisierte Zeitersparnis hängt vom konkreten Gewinde ab. „Bei Audi haben wir pro Gewinde 0,7 s im Vergleich zum konventionellen Gewindeformen eingespart“, berichtet Attila Bugár, bei Audi Hungaria Zrt. im Bereich Technologieentwicklung tätig sowie mit der Entwicklung der PunchTap-Technologie und der Standzeitoptimierung in den Fertigungslinien befasst. „Je nach Gewindetiefe wurde die Prozessdauer von 1,3 auf 0,6 oder 1,2 auf 0,5 s reduziert.“
Stete Optimierung
2016 hatte Audi auf der AMB bekanntgegeben, dass man die Fertigung des V6 mit dem Punch Tap startet. Seither wurden das Werkzeug wie auch die Prozessführung systematisch optimiert. Zum Beispiel die Warmbehandlung des Schnellschneidstahls, um so die Härte und Zähigkeit zu harmonisieren.
„Optimiert wurden aber auch die Geometrie, die Beschichtung und das Finishing. Beschichtungstests etwa hatten belegt, dass die AlSi8Cu3- und AlSi7Cu0,5Mg-Legierungen ein abweichendes Verschleißverhalten zeigen. Für die Zylinderkopfbearbeitung wurde daher in der Folge eine TiN-Beschichtung zum Einsatz gebracht, für das Kurbelgehäuse eine TiAlN-Schicht mit speziellem Finish“, so Christian Beer von Emuge-Franken, der als Entwicklungsingenieur mit der Entwicklung und Optimierung von Punch Tap verbunden ist.
Mit der Implementierung des Punch Tap in die neue Fertigungslinie machte Emuge-Franken den Prozess vor allem auch MMS-sicher. War das Verfahren bis dahin vor allem mit Emulsion praktiziert worden, sollte die junge Technologie nun erstmals mit Minimalmengenschmierung in Serie aufgesetzt werden.
„Für den Punch Tap benötigen wir eine gute Schmierung, weil alle Gewindezähne zugleich im Eingriff sind und folglich ein hohes Drehmoment auftritt“, nennt Peter Kopton, Erfinder der Punch-Tap-Technologie und im Bereich Fertigungstechnologie Antriebe bei der Audi AG tätig, den Knackpunkt. „Schnell stellte sich jedoch heraus, dass der Punch Tap auch unter diesen Bedingungen prozesssicher arbeitet. Das Fazit insgesamt war: Der Punch Tap funktioniert mit MMS sehr robust in der Serie und bringt hohe Standmengen.“
Die Erklärung dafür sei, dass das Werkzeug einen sehr kurzen Arbeitsweg zurücklegt. Bei dieser halben Gewindedrehung würden keine Aufschweißungen an den Gewindezähnen entstehen. Zugleich sei der Druck auf den einzelnen Zahn sehr hoch, sodass sich eine große Umformzone ausbildet, was Aufschweißungen zusätzlich entgegenwirkt.
Der nächste Schritt
Seit mittlerweile vier Jahren wird in Györ der V6-Motor in Serie gefertigt, in der von der ersten Stunde an auch der Punch Tap läuft. Prozesssicher und mit ausgereifter Standzeit. Aktuell werden mit einem Werkzeug im Zylinderkopf 200.000 Gewinde geformt, beim Zylinderkurbelgehäuse sind es 90.000. „Und das mit einem HSS-Werkzeug“, betont der technische Berater von Emuge-Franken Hungaria, Nándor Nárai. „Das ist schon ein Highlight.“
Das Ende der Entwicklung sei das allerdings nicht. Gegenwärtig sei für das Zylinderkurbelgehäuse ein Schritt von 90.000 auf 120.000 Gewinde im Gespräch. Die Versuche dazu wurden bereits abgeschlossen, und es ist sicher, dass sich 120.000 Gewinde formen lassen. „Die Diskussion ist momentan, ob die Linie dafür umgestellt wird“, berichtet Zsolt Hulik, der für die Optimierung der Werkzeugstandzeit an der Fertigungslinie Zylinderkurbelgehäuse V6 Otto EA839 zuständig ist.
Ergänzend fügt Csaba Bittmann hinzu: „Im Zylinderkopf jedenfalls sind Spitzenstandzeiten von 250.000 Gewinden keine Ausnahme.“ Seit einigen Jahren begleitet er die Absicherung der Werkzeugstandzeit an der parallelen Fertigungslinie für Zylinderköpfe.
Der Partner als Inspiration
Als innovatives Verfahren eingeführt, hat sich Punch Tap als hocheffiziente Technologie für die Massenproduktion erwiesen, die unter anspruchsvollen Bedingungen prozesssicher läuft und lange Standzeiten bringt. „Das Verfahren ermöglicht die genannten Zeit- und damit Investitionseinsparungen, und der laufende Betrieb verursacht keine höheren Kosten als ein konventionelles Werkzeug“, schätzt Kopton ein. Nach vier Jahren in der Serie präsentiere sich das PunchTap –Verfahren aktuell mit einem deutlich höheren Technologiestatus.
Den Weg dahin hat Emuge-Franken von Beginn an vor Ort begleitet. Bis heute ist ein Techniker in Györ direkter Ansprechpartner für die Technologieoptimierung. Kopton benennt den Rahmen für die gemeinsame Entwicklung von Audi und Emuge: „Die enge Zusammenarbeit zeigt sich auch in einer Entwicklungspartnerschaft, bei der wir neue Bohr- und Gewindeverfahren entwickeln. Aktuelles Beispiel ist Taptor, eine neue Gewindetechnologie, die einen Spiral- mit einem Gewindebohrer vereint und so eine massive Einsparung an Bearbeitungszeit ermöglicht“.
Ergänzend stimmt Dietmar Hechtle, Leiter Technisches Büro bei Emuge-Franken, zu: „Die enge Partnerschaft und Offenheit hat diese Technologieentwicklung überhaupt erst ermöglicht. Der Kunde ist unsere Inspiration. Er zeigt uns, welche Bauteile in den nächsten fünf bis zehn Jahren bearbeitet und welche Werkzeuge dafür benötigt werden. Bei Audi führte diese Zusammenarbeit zu einer innovativen Technologieentwicklung.“
Kontakt: