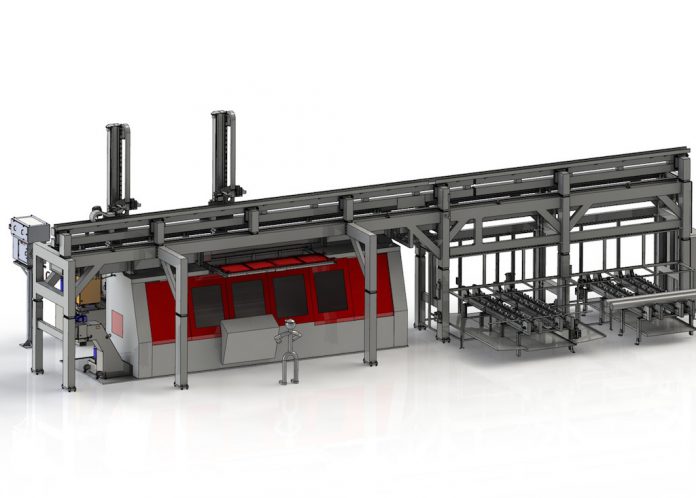
Ein bekanntes Unternehmen aus dem Druckmaschinenbau hatte die Mittenantriebsdrehmaschine CM 704 von WMS Sinsheim im Jahr 2003 gekauft. Seither tat sie klaglos ihren Dienst und fertigte Walzen für die Druckindustrie. Doch im Lauf der Jahre änderten sich die Anforderungen des Marktes. Das Teilespektrum erweiterte sich in Richtung größerer – vor allem längerer – Teile. Zudem standen ein höherer Automatisierungsgrad und schnellere Bearbeitung auf der Wunschliste.
Damit stellte sich die Frage: Eine neue Maschine kaufen oder die vorhandene überholen und modernisieren lassen? Neben dem Preisvorteil von zirka 400.000 Euro bei der Retrofit-Variante überzeugte den Kunden auch die umfassende Beratungs- und Engineering-Leistung der WMS-Experten.
Ausgehend von den Anforderungen des Kunden in Sachen Automatisierung und erweitertes Werkstückspektrum entwarfen die Maschinenbau- und Elektrokonstrukteure sowie die Softwareentwickler von WMS ein Komplettpaket: Von der Überholung und der Erweiterung der Maschine um zusätzliche Elemente über die nötigen Werkzeuge und die Bearbeitungsstrategie bis zur Software für die Herstellung der geplanten Produkte erhielt der Kunde alles aus einem Guss – und aus einer Hand.
Portalroboter, Werkstückmagazin und eine Fräsachse steigern Automatisierungsgrad und Bearbeitungstempo
Im konkreten Fall wurde die Maschine zunächst komplett zerlegt, um festzustellen, welche Teile erneuert oder aufgearbeitet werden mussten. Beim Wiederaufbau wurden schließlich die maßgeschneidert konstruierten neuen Features integriert. Um den Automatisierungsgrad zu steigern, erhielt die Maschine einen Portalroboter für die automatische Beladung. Ergänzt wurde zudem ein Werkstückmagazin, das zehn Werkstücke mit Längen zwischen 800 und 3.000 mm sowie mit bis zu 200 mm Durchmesser und 250 kg Gewicht aufnehmen kann. Dank dieses Vorrats kann die Maschine nun zwei bis drei Stunden vollautomatisch arbeiten.
Die optimale Bearbeitung sehr langer Teile wird nun durch zwei neu eingebaute, selbstzentrierende Lünettenschlitten ermöglicht. Aus der reinen Drehmaschine wurde im Rahmen der Modernisierung zudem eine Dreh-Fräsmaschine. Dafür wurden eine zusätzliche Y-Achse und angetriebene Werkzeuge integriert. So können zusätzlich zum Drehen auch Fräs- und Bohrbearbeitungen in einer Aufspannung durchgeführt werden.
Auch hinsichtlich Kühlung und Schmierung bei der Bearbeitung gab es große Verbesserungen. Zum einen wurde eine Hochdruckkühlschmierstoffeinrichtung integriert. Zum anderen wurde die Maschine erstmalig mit einer Aufbereitungsanlage für die Kühlschmierstoffe ausgestattet. Dank dieser Filteranlage kann nun ein großer Teil der Kühlschmierstoffe in einem Kreislaufsystem wiederverwendet werden, was die Kosten für neue KSS und die Entsorgung verbrauchter merklich reduziert.
Neueste Steuerungstechnik
Um all die neuen mechanischen Möglichkeiten optimal nutzen zu können, wurde die Maschine mit einer neuen Steuerung ausgestattet. Mit der Siemens 840d Solution Line lässt sich die von acht auf 16 verdoppelte Anzahl der Achsen und Spindeln problemlos steuern und dank Netzwerkanbindung sowohl lokal als auch aus der Ferne warten. Der Ethernet-Anschluss ermöglicht zudem die Einbindung der Maschine in eine verkettete Fertigungslinie. Mit der neuen Steuerung hielt auch das Siemens-Konzept Safety Integrated Einzug in die Maschine, das die Sicherheitstechnik in die Standardautomatisierung integriert.
Die Auslieferung und Inbetriebnahme ist im Juli erfolgt. Zusammen mit der Maschine erhielt der Kunde auch eine umfangreiche Dokumentation der insgesamt neun Monate dauernden Überholungs- und Modernisierungsarbeiten.
Kontakt: