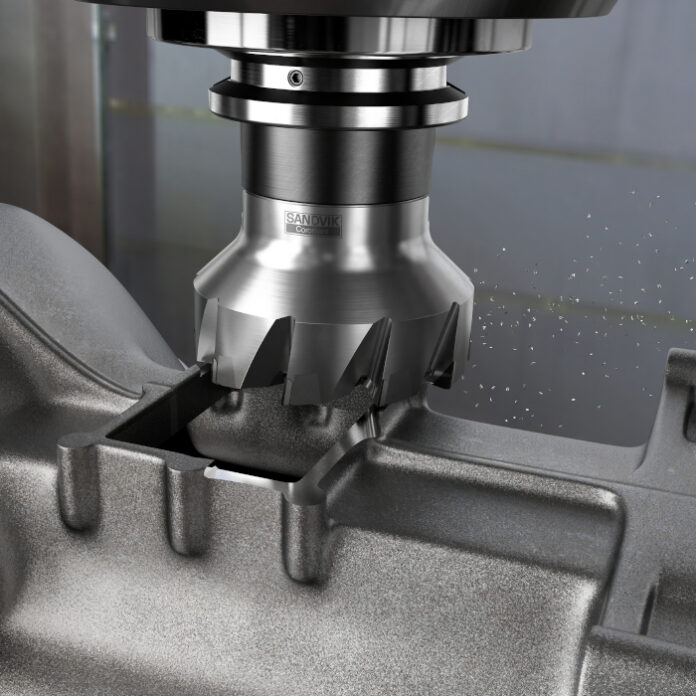
Batteriesysteme werden sich in den kommenden Jahren weiterentwickeln und neue Entwicklungen und Designs notwendig machen. Für OEMs bedeutet das, dass sie Batteriesystemkomponenten herstellen müssen, die auf komplexeren Designs basieren. Die Bearbeitung dieser Konstruktionen erfordert effiziente und leichtere Zerspanungswerkzeuge, um die Auswirkungen auf die Werkzeugmaschine zu minimieren und sicherzustellen, dass das Bauteil seine Form behält.
McKinsey führt die veränderte Rolle der OEMs hin zu einer stärkeren Beteiligung an der Batterieproduktion auf die „Rückwärtsintegration der OEMs von Batteriepacks und -modulen hin zur Zellproduktion“ zurück. Gleichzeitig findet ein Wettlauf um leichtere und effizientere Elektrofahrzeuge (EVs) statt, die längere Strecken mit maximaler Reichweite pro Ladung zurücklegen können.
Darüber hinaus müssen die Unternehmen die komplexeren Bauteile in höchster Qualität und mit hoher Produktivität herstellen. Doch wie kann man dies erreichen und gleichzeitig die Kosten pro Bauteil niedrig halten? Die Antwort liegt in effizienteren Zerspanungswerkzeugen, die gut zugänglich und möglichst leicht sind, um einen schnellen Werkzeugwechsel zu ermöglichen.
CO2-Emissionen reduzieren
Um Pkw und Lkw mit geringerem Gewicht, besserem Kraftstoffverbrauch und Fahrverhalten zu bauen, setzen die Fahrzeughersteller auf Leichtbau.
McKinsey berechnet in der Studie Lightweight, heavy impact, dass Leichtbau-Maßnahmen zu einer gewissen Reduktion der CO2-Emissionen beitragen können (ca. 0,08 g CO2 pro eingespartem Kilogramm). „Gelingt es einem OEM, das Fahrzeuggewicht um 100 kg zu reduzieren, spart er etwa 8,5 g CO2 pro 100 km“, so die Schlussfolgerung der Studie.
Als eines der leichtesten Metalle der Welt ist Aluminium ein bewährter Leichtbauwerkstoff. Aluminium ist fast dreimal leichter und hat eine geringere Festigkeit als Eisen, ist aber dennoch sehr stabil und korrosionsbeständig. Aus konstruktionstechnischer Sicht hat sich herausgestellt, dass das Gesamtgewicht des Motorblocks um bis zu 40 bis 55 % reduziert werden kann, wenn herkömmliche Gussteile durch Aluminiumlegierungen ersetzt werden.
Ein weiterer Vorteil von Aluminium ist, dass es sehr gut recycelbar ist und ohne Beeinträchtigung oder Veränderung seiner mechanischen Eigenschaften eingeschmolzen und wiederverwendet werden kann. Ungefähr 75% des jemals produzierten Aluminiums wird heute noch verwendet, was die Relevanz dieses Materials für die Nachhaltigkeitsstrategien von OEMs unterstreicht.
Kleinere Oberflächen
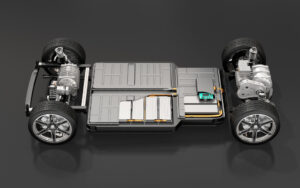
Der Antriebsstrang eines europäischen Pkw enthält in der Regel rund 80 Kilogramm Aluminium, weshalb gerade diese Teile – Motor, Getriebe, Aufhängungsteile, Gehäuse – ein Bereich sind, in dem sich Maßnahmen zur Gewichtsreduzierung anbieten. Auch in den Batterien selbst kann Aluminium eingesetzt werden. So empfiehlt die EU-China Energy Cooperation Platform (ECECP) Aluminium-Luft-Batterien (AI-air) als „kostengünstige, leichte und leistungsstarke“ Alternative zu Lithium-Ionen-Batterien (Li-Ion).
Batteriegehäuse aus Aluminium haben im Allgemeinen kleinere Oberflächen mit mehr Gewinden, Bohrungen und anderen Merkmalen. Ein weiterer wichtiger Bereich sind Batteriegehäuse für Lkw – insbesondere für größere Modelle, die nicht in Ballungsräumen eingesetzt werden – mit einer Länge von bis zu zwei Metern haben.
Bei der Fertigung von Batteriegehäusen werden eine Reihe von Werkzeugen und Anwendungen, wie z. B. Fräsen oder Entgraten, eingesetzt. Selbst größere Batteriegehäuse werden nicht mit großen Werkzeugen bearbeitet, da sie kleinere Oberflächen mit mehr Details, Gewinden und Bohrungen aufweisen. Dies erfordert Eck- und Planfräser oder Reibahlen, mit denen die Teile in der geforderten Qualität und mit den geforderten Toleranzen hergestellt werden können.
Vibrationen beseitigen
Sandvik Coromant empfiehlt für die Bearbeitung der Batteriegehäuse den Einsatz seiner M5-Fräser für die Automobilindustrie, darunter den Planfräser M5F90, der für eine Bearbeitung ohne Grate, Kratzer oder Ausbrüche entwickelt wurde. Der Fräser ist für die Bearbeitung von dünnwandigen Aluminiumteilen konzipiert und dafür mit einem kleineren Fräskörper von 25 bis 80 mm Durchmesser ausgestattet. Er ist mit gelöteten PKD-Schneiden ausgestattet, erfordert keine Einstellung und garantiert einen sehr geringen Rundlauf. Dadurch ermöglicht der M5F90 hohe Vorschubgeschwindigkeiten ohne Vibrationen.
In einem konkreten Anwendungsfall wurde der neue Planfräser eingesetzt, um bei der Fertigung eines Aluminium-Batteriegehäuses die Oberflächen des neu gegossenen Aluminiumteils in einem Arbeitsgang gratfrei zu bearbeiten.
Die Abmessungen betrugen ca. 980 x 600 x 130 mm. Bei der Bearbeitung des Bauteils kamen insgesamt 48 Werkzeuge zum Einsatz, darunter Vollhartmetallbohrer und -fräser, HSS-Gewindebohrer, PKD-Reibahlen und -Fräser sowie der M5F90. Das Aluminiumteil wurde auf einem 5-Achs-Bearbeitungszentrum bearbeitet, das mit einem Hochgeschwindigkeitswerkzeughalter HSK 63 ausgestattet war.
Die gelöteten PKD-Wendeschneidplatten des M5F90 haben sowohl radial als auch tangential abgestufte Schneidkanten. Diese Eigenschaft reduziert die Leistungsaufnahme und ermöglicht das Fräsen mit höheren Schnittgeschwindigkeiten, wodurch Gratbildung und Vibrationen während der Bearbeitung reduziert werden. Vor allem letztgenannter Vorteil trägt zu einer zuverlässigen Leistung mit verbesserter Werkzeugstandzeit bei und erhöht die Anzahl der gefertigten Bauteile.
Bei der Fertigung der Batteriegehäuse zeigte sich ein entscheidender Vorteil der M5F90. Durch das zeitsparende Schruppen und Schlichten in nur einer Aufspannung konnte das Bauteil in 20,3 Minuten bearbeitet werden. Mit dieser verbesserten Werkzeugperformance können OEMs verstärkt in die Produktion von Batteriesystemen einsteigen und sich gleichzeitig vom Wettbewerb differenzieren.
Kontakt: