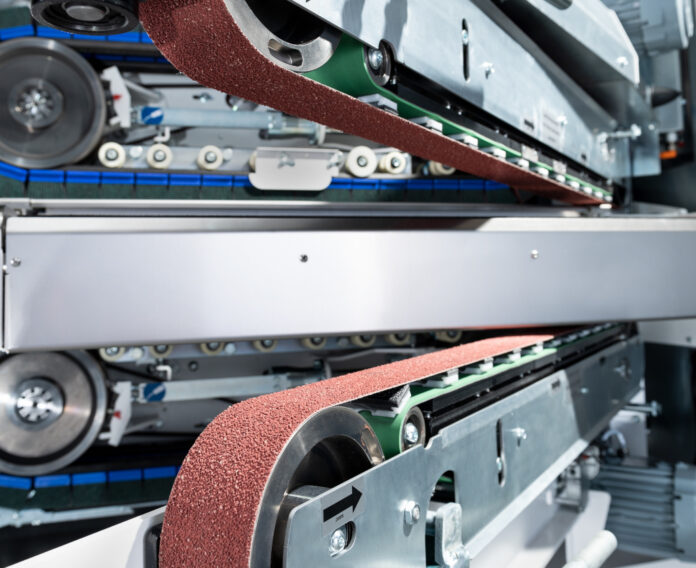
Die Kompetenzen der Wiechmann Ketten- und Kettenräderbau GmbH aus Edewecht liegen in zwei Bereichen. Zum einen ist dies die Kettenfertigung. Hier werden Verschleißteile für Grabenfräsen und sonstige Einsatzbereiche hergestellt, beispielsweise Fräsketten, Kettenräder oder Grabwerkzeuge. Im zweiten Kompetenzbereich – der Blechbearbeitung – dreht sich alles um Laserschneiden, Umformen sowie die Entgratung, das Kantenverrunden und Schleifen.
Im Jahr 1963 wurde das Unternehmen vom heutigen Senior Otto Wiechmann gegründet und startete mit der Herstellung von Verschleißteilen für Grabenfräsen für die landwirtschaftliche Drainage, später kam die Kettenfertigung dazu und im Jahr 1999 die Blechfertigung. Heute beschäftigt Wiechmann 55 Mitarbeiter. Etwa die Hälfte davon arbeitet in der Blechfertigung. Hier wird für unterschiedlichste Branchen gefertigt, so beispielsweise für die Lebensmittel- oder die Verpackungsindustrie. Etwa 10 Prozent der lasergeschnittenen Teile werden für die eigenen Produkte in der Kettenfertigung benötigt.
Qualität, reproduzierbare Ergebnisse und Effizienz
Für Andre Wiechmann, den Geschäftsführer des Unternehmens, spielt das Thema Sicherheit eine wichtige Rolle. „Wir wollten von der Handentgratung weg. Die Verletzungsgefahr sollte minimiert werden. Außerdem sind die Qualitätsanforderungen unserer Kunden in den letzten Jahren immer weiter gestiegen. Ein geringer Stromverbrauch und eine hohe Effizienz standen im Mittelpunkt der Überlegungen“, sagt er.
Auch für Hinrich Böhlje, der im Jahr 2015 zu Wiechmann kam, sind die Kriterien wichtig. Der Produktionsleiter für die Blechfertigung sagt rückblickend: „Wir hatten zu diesem Zeitpunkt die SBM-M 1000 S2 von Lissmac im Haus, die bereits im Jahr 2006 angeschafft wurde, sowie zwei andere Maschinen zum Kanten verrunden. Die beiden anderen Anlagen verbrauchten sehr viel Strom. Zudem hatten diese nicht die Option zur beidseitigen Bearbeitung der Teile. Es war also immer eine Nachbearbeitung oder ein zweiter Arbeitsgang notwendig. Und mit der damaligen Lissmac-Anlage war lediglich die Bearbeitung von Blechen mit einer tausender Breite möglich. Wir schneiden aber auch Teile bis zwei Meter Breite.“
Es fiel also die Entscheidung, in neue Anlagentechnik zu investieren. Im Fokus des Vorhabens stand die höhere Effizienz durch eine beidseitige Bearbeitung, die Abdeckung eines breiteren Teilespektrums sowie natürlich ein geringerer Stromverbrauch.
Von der verlässlichen Technik des Bad Wurzacher Unternehmens waren Geschäftsführer Andre Wiechmann und Hinrich Böhlje bereits überzeugt. Im Jahr 2017 wurde für die Bearbeitung von Kleinteilen eine SBM-XS 300 angeschafft – ausgelegt mit einem Vakuumband für Teile aus Edelstahl und Aluminium.
Und so stand der Maschinenbauer aus Oberschwaben auch auf der Auswahl -Liste, als es um die Neuinvestitionen ging. Zudem kannte Produktionsleiter Böhlje aus einer früheren Tätigkeit weitere Lissmac-Anlagen.
Schnelle Entscheidung und angepasster Projektierungsprozess
Im Frühjahr 2018 wurde es für Andre Wiechmann, der die Unternehmensverantwortung 1996 von seinem Vater übernommen hatte, nach einem Messebesuch konkret. Er nahm Kontakt mit Lissmac auf und das Projektierungsprozedere konnte starten.
„Wir haben eine Vielzahl von Teilen für Versuche zu Lissmac nach Bad Wurzach geschickt. Und wir waren auch selbst vor Ort. Generell sind wir mit all unseren Produkten sehr nah am Kunden und das wollten wir auch mit den neuen Maschinen sein“, sagt er.
Etwa ein Jahr dauerten der Prozess sowie die darauf abgestimmte Projektierung der Anlage. Im Ergebnis wurden zwei Schleif- und Entgratmaschinen SMB-L 1500 G1S2 gekauft, jeweils mit einem Zulauf- und Ablaufband. So können auch Teile bis vier Meter Länge beidseitig bearbeitet werden. Mit der Anschaffung der beiden SMB-L 1500er Anlagen wurde die SMB-M 1000 S2 dann verkauft und auch die anderen beiden Schleifmaschinen wurden abgegeben.
„Die Entscheidung für Lissmac-Technik ist relativ schnell gefallen“, sagt Produktionsleiter Böhlje. „Zum einen war die positive Erfahrung mit einer vergleichbaren Anlage ja bereits da. Zum anderen gab es nicht so viele Hersteller, die die beidseitige Bearbeitung anbieten. Und nicht zuletzt zeichnen sich die Anlagen durch eine hohe Flexibilität aus.“ Würden sich also die Produkte bei Wiechmann ändern, könnten schnell und unproblematisch die Aggregate gewechselt werden.
Durch die Möglichkeit, ein zweites Bearbeitungsaggregat zuzuschalten, werden nun 50 Prozent Bearbeitungszeit eingespart. Dazu kommt, dass nur noch eine Absaugung für beide Anlagen erforderlich ist. Zudem verfügt die SMB-L 1500 über ein vorgeschaltetes Aggregat mit Schleifpapier. Neben der nun möglichen beidseitigen Bearbeitung trägt auch dies dazu bei, effiziente Prozessabläufe sicher zu stellen.
Wichtig sind für Geschäftsführer Wiechmann außerdem die Materialtrennung und somit eine sortenreine Bearbeitung in der Fertigung. So wird eine der neuen Schleif- und Entgratmaschinen nur für Edelstahl verwendet und die andere für Baustahl. „Mit der maschinellen Entgratung können wir nun Effizienz in der Bearbeitung sicherstellen und reproduzierbare Bearbeitungsergebnisse gewährleisten. Das sind auch wichtige Verkaufsargumente in der Blechfertigung“, sagt er.
Aluminiumbearbeitung und Explosionsschutz
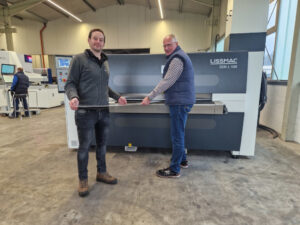
Im Juni 2019 wurden die beiden SMB-L 1500 geliefert. Und mit Blick auf die Aluminiumbearbeitung wurde im September 2022 auch noch eine dritte baugleiche SMB-L 1500 für die Aluminiumbearbeitung angeschafft. Die Geschichte, die hinter dieser dritten Kleinteilemaschine steckt, erzählt Hinrich Böhlje: „Für einen Kunden sollten wir kantenverrundete Aluminiumblechteile herstellen. Bisher wurden diese nur gelasert. Da das Handling bei genau diesen Teilen jedoch sehr hoch ist, mussten sie verrundet werden. Wir brauchten also sehr schnell eine Maschine zum Aluminiumverrunden.“
Dirk Schürstedt, Gebietsverkaufsleiter Metal Processing bei der Lissmac Maschinenbau GmbH, setzt fort: „Ja, das war wirklich eine Herausforderung für uns. Von der Idee zur Anschaffung einer neuen Anlage bis hin zur Lieferung waren es sechs Wochen. Alles lief sehr fokussiert ab. Selbst ein Abstimmungsthema zu nötigen Förderwalzen konnte in drei Stunden geklärt werden. Das war beeindruckend für alle Beteiligten.“
„Wir mussten bei der Aluminiumbearbeitung den Explosionsschutz beachten. Für die entstehenden Stäube war eine Nassabsaugung erforderlich. Die Anschaffung einer separaten Absaugung und ein damit immer wieder notwendiger Umbau einer vorhandenen Anlage erschien uns zu aufwendig. Und so haben wir uns entschieden, eine weitere Maschine anzuschaffen, diese in einem separaten Raum unterzubringen und so sowohl alle Sicherheitsaspekte zu beachten als auch effiziente Prozessabläufe sicher zu stellen“, begründet Andre Wiechmann die Entscheidung.
Alle drei SBM-L-Schleif- und Entgratmaschinen haben im Wesentlichen die gleiche Ausstattung und die gleiche Bedienoberfläche. Wichtig war für Wiechmann bei der Ausstattung der Anlagen war dabei auch eine automatische Verschleißkompensation der Bearbeitungsaggregate. Wenn sich auf Grund der Laufzeit also das Schleifbild verändert, stellt sich die Maschine automatisch nach. So kann die Qualität einmal verlässlich eingestellt werden. Das heißt auch, dass Kunden die Schleifqualität beziehungsweise das Schleifbild individuell beauftragen können.
Das Rundum-Paket stimmt
Die Investition in die neue Anlagentechnik hat sich für das Unternehmen Wiechmann gelohnt: Die Schleifprozesse laufen wesentlich effizienter ab und es können größere Teile bearbeitet werden. Bei verrundeten Teilen hält der Lack zudem besser, Folien auf dem Blech müssen nicht entfernt werden und Gravuren sind besser zu erkennen. Ein weiterer, sehr wichtiger Punkt: Die neuen Maschinen benötigen deutlich weniger Strom.
Viele der Wiechmann-Kunden wissen das maschinelle Kantenverrunden zu schätzen und nehmen die Leistung gern an. Und durch die neue Anlagentechnik hat sich noch ein weiteres Geschäftsfeld aufgetan. „Wir haben Kunden, die selbst Blechteile herstellen und diese zum Kantenverrunden zu uns bringen“, sagt Wiechmann.
Und ein Punkt ist für den Geschäftsführer des Ammerländer Unternehmens besonders wichtig: die Arbeit auf Augenhöhe. „In der Zusammenarbeit mit Lissmac gibt es keine komplizierten und langwierigen Prozesse. Wir müssen kein Ticket ziehen, wenn wir im Alltagsbusiness eine schnelle Antwort auf unsere Frage benötigen. Wir können uns jederzeit auf den guten Service und den guten Maschinenbau verlassen. Fest steht: Wir werden als Kunde einfach ernst genommen.“
Kontakt: