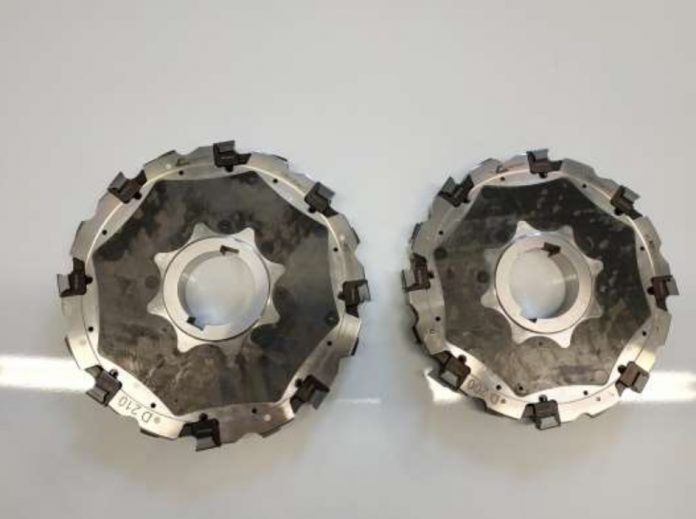
Ursprünglich wurde das ehrgeizige Ziel verfolgt, die Gesamtverarbeitungszeit um 50 % zu senken. Das endgültige Design übertrifft diese Zielvorgabe sogar! Das Vierscheiben-Hybridwerkzeug halbiert die Schnittzeit und erhöht den Vorschub. Das Ergebnis: ein Hochleistungs-Hybridfräsgerät, das am gleichen Fräszentrum 78 % schneller betrieben werden kann als ein normaler Zweischeibenfräser.
Der neue Vierscheibenfräser bietet laut des Herstellers die folgenden Vorteile:
- Niedriger Trägheitsmoment, was zu einem niedrigeren Energieverbrauch führt und Kosteneinsparungen ermöglicht
- Niedrigere thermomechanische Belastung auf Fräsgeräte
- Bessere schwingungsdämpfende Eigenschaften, was die Verarbeitungspräzision von Langlöchern erhöht.
- Reibungsloserer Maschinenbetrieb, was eine hochwertiger Oberflächenveredelung ermöglicht
- Beträchtlich höhere Ausgaberaten und Produktivität
Für Hersteller bietet sich ein weiterer Kostenvorteil: Die Schneide des neuen Hybrid-Werkzeug mit den 40 zusätzlichen Wendeschneidplatten (WSP) ist fast fünf Mal langlebiger.
Erwartungen übertroffen
Den Anstoß für das Kooperationsprojekt für ein neues Fräswerkzeug gab HOFMEISTER s.r.o.. Anlass war eine Anfrage eines führenden europäischen Kettenherstellers nach einem Vierscheiben-Fräswerkzeug, mit dem der Leistungssatz verbessert und die Produktionskosten gesenkt werden sollten. Im Entwurf und in der Produktion kam die Karbonfaser-Technologie von CompoTech zum Einsatz.
So entstand einen neues Hybrid-Fräswerkzeug aus einem leichten Karbonfaser-Verbundstoff und Stahl mit zwei zusätzlichen Schneidescheiben. Das neue Vierscheiben-Hybridwerkzeug liegt unter dem zugelassenen Höchstgewicht von 25 kg für die vorgegebene Doosan Mecatec HM63H Doppelpaletten-Bearbeitungsmaschine. Mit vier normalen Metallscheibenschneidern mit einem Einzelgewicht von 7,93 kg wäre dies nicht möglich gewesen.
Um die Verarbeitungsleistung noch weiter zu steigern, wurden beim Entwurf des neuen Hybrid-Werkzeugdesigns noch zusätzliche WSP pro Scheibe eingebaut. Das Hybrid-Fräswerkzeug verfügt über insgesamt 64 WSP auf vier Scheiben, wobei normale Zweischeiben-Fräsgeräte im Vergleich dazu nur 24 WSP aufweisen. Das Ergebnis ist eine erhebliche verbesserte Verarbeitungsleistung, die die Verarbeitungszeit eines Kettenelements aus Schmiedestahl von 45 auf 10 Sekunden reduziert und somit die Erwartungen weit übertrifft.
Bewährte Zusammenarbeit in Forschung und Entwicklung
HOFMEISTER ist ein Maschinenbaubetrieb in Privatbesitz in der Tschechischen Republik. Er spezialisiert sich auf die Entwicklung von vollständigen Verarbeitungstechnologien, was auch Programmierung, Entwurf und Herstellung der Standard- und Spezialwerkzeuge umfasst. HOFMEISTER – Innovation ist die Forschungs- und Entwicklungsabteilung des Unternehmens.
normalen Zweischeiben-Fräsers aus Metall. (Bildnachweis: Hofmeister)
HOFMEISTER – Innovation und CompoTech arbeiten schon seit langem erfolgreich an der gemeinsamen Entwicklung und Herstellung von leichten Hybrid-Werkzeugen der nächsten Generation. In die bewährte Zusammenarbeit zwischen den Forschungs- und Entwicklungsteams der beiden Unternehmen fließt die Expertise von CompoTech im Bereich Karbonfaser-Verbundtechnologie und Produktionskenntnisse ebenso ein wie die umfangreichen Spezialkompetenzen von HOFMEISTER, das die Werkzeugspezifikationen, Technologie und Präzisionsherstellung des fertigen Werkzeugs bereitstellt.
Die Anlagen von CompoTech befinden sich im Südwesten der Tschechischen Republik, in der Nähe der HOFMEISTER-Betriebe in Pilsen. Das Unternehmen blickt auf eine gute Erfolgsbilanz beim Ersatz von traditionellen Metallteilen an automatisierten Montagelinien und Industriesystemen zurück. In den letzten 15 Jahren hat sich CompoTech auf die Entwicklung und Produktion von Karbonfaserträgern für Roboterfertigungslinien im Automobilsektor sowie von Karbonfasersträgern für Schwermetallschneidegeräte konzentriert.
In den letzten Jahren wurde der strategische Fokus auch auf zugehörige Komponente wie rotierende Wellen, Spindeln und Werkzeuge und Werkzeughalter aus Karbonfaser ausgeweitet. Auf diese Weise möchte das Unternehmen die Leistung von Verarbeitungswerkzeugen ergänzend und ganzheitlich verbessern. In den letzten Jahren erfolgten wichtige Investitionen in 6-Achsen-Fibre-Placement-Technologie und schnelle betriebseigene Werkzeugherstellungskapazitäten anhand von 3D-Drucken. Beides hat es CompoTech ermöglicht, den Entwurf und die Entwicklung von innovativen Karbonfaser-Werkzeugen zu beschleunigen.
Leichtes Hybrid-Design aus Verbundstoffen
Das neue Hybrid-Werkzeug nutzt ein Epoxy-Komposit mit Ultra-high Modulus Karbonfasern für das Innenteil der einzelnen Frässcheiben. Der von CompoTech entwickelte betriebseigene kontinuierliche Faserherstellungsprozess ermöglichte die Produktion von voll integrierten hybriden Frässcheiben mit einem Außenrand, der aus 16 Metall-WSP besteht.
Der Leiter der analytischen Designabteilung von CompoTech, Ing. Dr. Robin Poul erklärt: „Wir konnten eine Lösung für die Scheibenschnittstelle aus Karbonfaserverbund zwischen der Stahlnabe und dem Stahlring finden, mit der die Belastung während dem Fräsen transferiert wurde und trotzdem ausreichend Steifheit gegeben war. Dies wurde anhand einer Kombination aus Verzahnungen und Stahlbolzen erreicht.“
Die halbfertigen Karbonfaserverbundteile für die Hybridscheibe wurden von CompoTech mit halbfertigen Stahlteilen von HOFMEISTER hergestellt und montiert. HOFMEISTER übernahm auch den letzten Schliff für jede Hybrid-Schneidescheibe sowie die Montage des vollständigen Hybrid-Fräsgeräts. Der gesamte Hybrid-Vierscheibenfräser wiegt nur 16,25 kg, was weit unter dem maximal zugelassenem Werkzeuggewicht für BT50 L 150 mm Hauptdorn an der Doosan Mecatec HM63H liegt.
Werkzeugleistung überzeugt
Das Test-Fräsen des Vierscheiben-Hybridwerkzeugs mit einem Durchmesser von 200 mm erfolgte an einem Verbindungsglied aus hochfestem Schmiedestahl anhand der Doosan Mecatec HM63H Bearbeitungsmaschine. Der Fräsvorgang, um die Seiten und Unterseiten des geschmiedeten Verbindungsglied präzise innerhalb der Toleranzen zu schneiden, war mit dem neuen Hybrid-Vierscheibenfräser in 10 Sekunden abgeschlossen, 35 Sekunden schneller als mit dem Zweischeibenfräser aus Metall.
Die Messungen an den vc– und vf-Raten für beide Fräswerkzeuge zeigten, dass der hybride Vierscheibenfräser aus Karbonfaser eine 50 % schnellere Schneidegeschwindigkeit und eine 54 % höhere Zufuhrrate aufwies. Außerdem wurden Daten über die Standzeit des Werkzeugs erfasst. Für den Zweischeibenfräser betrug sie sich auf ungefähr 250 bearbeitete Teile vor dem Werkzeugwechsel, während sie beim neuen hybriden Vierscheibenwerkzeug bei über 1200 Teilen (>4,8 fach) lag.
Im Vergleichstest
Der Vergleichstest im Projekt hat eindeutig gezeigt, dass der neue Hybrid-Vierscheibenfräser auf genau die gleiche Weise zum Verarbeiten genutzt werden kann wie ein konventioneller Zweischeibenfräser aus reinem Metall, jedoch eine höhere Verarbeitungsgeschwindigkeit bietet und langlebiger ist. Diese erheblichen Vorteile machen die Einkaufskosten für den neuen Hybrid-Fräser schnell wieder wett. HOFMEISTER schätzt, dass sich die Einkaufkosten für einen Massenproduzenten innerhalb von nur drei Monaten auszahlen. Tabelle 1 zeigt die beiden Fräswerkzeuge im technischen, betrieblichen und wirtschaftlichen Vergleich.
Ing. Dr. Pavel Kožmín, Leiter der Forschung und Entwicklung bei HOFMEISTER s.r.o., kommentiert: „Dies war eine weitere hervorragende Zusammenarbeit zwischen den Forschungs- und Entwicklungsteams beider Unternehmen. Wir haben ein Fräsgerät entwickelt, dass unsere ursprünglichen Erwartungen übertrifft. Zu verdanken ist dies dem einzigartigen Karbonfaser-Epoxy-Komposit-Design und den Produktionskapazitäten von CompoTech. Das neue Hybrid-Fräsprojekt hat mit seinen betrieblichen und wirtschaftlichen Vorteilen die Erwartungen unserer Kunden überschritten.“
Der neue Hybrid-Vierscheibenfräser bietet Herstellern die Möglichkeit, Zeit und Geld zu sparen, indem bei vorhandenen CNC-Bearbeitungsgeräten erheblich höhere Einheitsproduktionsraten bei gesenkten Gesamtproduktionskosten erzielt werden. Das neue Hybrid-Werkzeug vermeidet Engpässe, erhöht die Rentabilität und verzögert oder vermeidet den Bedarf an weiterer Kapitalinvestition, um Wachstumsziele zu erreichen – Vorteile, die alle Unternehmen zu schätzen wissen.
Kontakt: