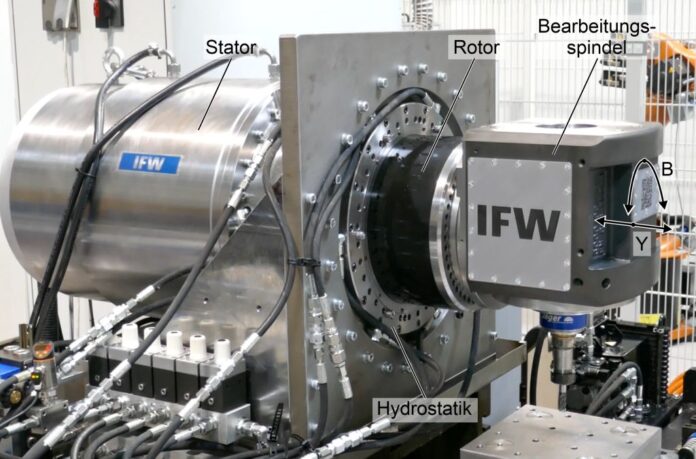
Für eine kombinierte Bewegung in mehreren Freiheitsgraden werden in Werkzeugmaschinen bislang einzelne Achsen in einer seriellen Anordnung verschaltet. Durch die serielle Struktur trägt die unterlagerte Achse die auf ihr angeordnete Achse. Dadurch steigt der Platzbedarf und die erreichbare Dynamik und Präzision werden begrenzt.
„Um diesen Nachteilen zu begegnen, haben wir einen neuartigen Mehrkoordinatendirektantrieb entwickelt“, erläutert IFW-Mitarbeiter Henning Buhl. Die Neuheit des Antriebes besteht darin, dass ohne eine serielle Kinematik in linearer- und rotatorischer Achsrichtung mit nur einer Maschinenkomponente (Rotor) verfahren werden kann. Um auch bei einer hoch produktiven Zerspanung die Tragfähigkeit der Rotorlagerung zu gewährleisten, wurde hierfür extra eine hydrostatische Lager- und Klemmeinheit konzipiert.
Der Mehrkoordinatendirektantrieb in Aktion
Die Eignung des Mehrkoordinatendirektantriebes für zerspanende Prozesse wurde am Institut erfolgreich nachgewiesen. Buhl erläutert: „Unsere Fräsversuche bestätigen, dass verschiedene Geometrien im Voll- und Halbschnitte prozessstabil gefräst werden können.“ Eine Abdrängung der Achsposition durch die Bearbeitungskräfte wurde selbst bei Eingriffstiefen von 5 mm nicht festgestellt. Das Fräsen war mit einer stabilen Achsreglung und Achsposition möglich. In Aktion ist der Antrieb unter folgendem Link als Video zu sehen (www.youtube.com/watch?v=7m4gLaebbMY).
Mit dem kombinierten Antrieb wurden Verfahrweg entlang der Y-Linearachse um ± 100 mm und entlang der B-Rotationsachse um ± 120 ° erreicht. Diese gleichen den Verfahrwegen eines konventionellen Dreh-Fräszentrums. Es wurde zudem ein maximales Drehmoment von 1.471,6 Nm und eine Vorschubkraft von 4.893,7 N erzielt. Neben der Eignung für die Fräsbearbeitung weist der Mehrkoordinatenantrieb eine hohe Positioniergenauigkeit auf, sodass hochgenau im einstelligen μm-Bereich verlässlich positioniert werden kann. Gegenüber der konventionellen Kinematik ermöglicht der kombinierte Antrieb einen bis zu 16 % kompakteren Bauraum. Zusätzliche Vorteile sind die um 82 % geringere bewegte Masse in Y-Achsrichtung sowie die im geklemmten Achszustand erhöhte Steifigkeit gegenüber einer seriellen Kinematik.