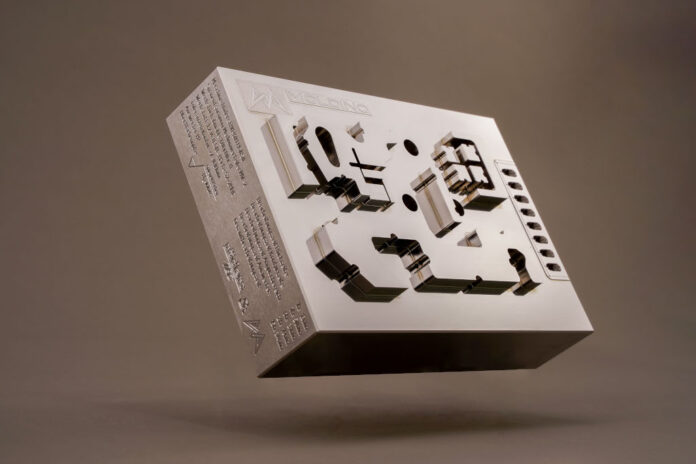
Das Thema Prozessoptimierung durch Komplettbearbeitung hat MOLDINO zum Anlass genommen, in Zusammenarbeit mit Röders deutschlandweit eine Workshop-Reihe zu starten. Zur Auftaktveranstaltung bei Röders in Soltau hatte sich Prozessoptimierer und Anwendungstechniker Mark Rotzoll vom japanischen Präzisionswerkzeughersteller MOLDINO Tool Engineering zusammen mit seinem Herforder Kollegen Andreas Schadeck etwas ganz Besonderes einfallen lassen:
Ein speziell für diese Veranstaltung konstruiertes, praxisnahes Konturwerkstück, dessen 3D-CAD-Daten einigen ausgewählten langjährigen MOLDINO-Kunden im Vorfeld ausgehändigt werden sollten. Verbunden war dies mit der Bitte, dieses Beispielteil mit den in ihrem Haus üblichen Technologien zu fertigen und die benötigten Bearbeitungszeiten sowie alle damit verbundenen Liege- und Transportzeiten zu dokumentieren. Das auf 52 HRC gehärtete und geschliffene Rohmaterial wurde mitgeliefert.
Die Konstruktion aus Warmarbeitsstahl 1.2343 ESU (X37CrMoV5-1 ESU) bot einige Herausforderungen: So galt es für die Auswerfer 37 Durchgangsbohrungen mit Toleranz H7 in den Durchmessern 0,6 mm, 0,8 mm, 1 mm, 1,5 mm sowie 2 mm herzustellen. Bei drei weiteren Passungen mit 6 mm Durchmesser betrugen die Toleranzvorgaben 0 bis +3 µm.
Auch die seitlichen Dichtbereiche des Formeinsatzes waren anspruchsvoll, insbesondere bezüglich der hohen Anforderungen an die Zylindrizität. Dies traf auch auf die drei zu fertigenden optischen Flächen (Spiegelflächen) mit einem geforderten Mittenrauwert von Ra 0,025 µm zu. Deshalb wurde für das Beispielwerkstück die Werkstoffausführung Elektroschlacke umgeschmolzen (ESU) gewählt, weil diese sich sehr gut für das Herstellen von Hochglanzflächen eignet.
Ansonsten betrug die Toleranz der Kontur- und Bodenflächen +/- 0,01 mm, die für entsprechende Spritzgussformeinsätze typisch ist. „Die ausgewählten Teilnehmer hatten das Teil also mit der ihnen jeweils zur Verfügung stehenden Fertigungstechnik hergestellt, alle Schritte dokumentiert und zum Workshop mitgebracht“, erläutert Schadeck.
Was ist dabei herausgekommen? Es gab unter den Kunden niemand, der den Benchmark-Formeinsatz auf einer einzigen Maschine komplett gefertigt hat. Doch genau dies hatten Rotzoll und Schadeck gemacht, 5-achsig in zwei Aufspannungen. Und zwar auf einer RXP 601 DS im Technikum von Röders.
Die meisten Bearbeitungsbeispiele wurden im Vorfeld des Workshops hergestellt. Alle diese Schritte sind dann bei der Präsentation detailliert erläutert worden. Dabei ging es auch um Grundsätzliches wie die Vor- und Nachteile der Hartbearbeitung, insbesondere des Hartschruppens. Oder wann und bei welchen Randbedingungen nach heutigem Stand auf das Senk- und Drahterodieren verzichtet werden kann und wann nicht.
„Die gesammelten Daten der Kunden haben wir anonymisiert und hieraus einen Durchschnitt sowie den Besten ermittelt“, beschreibt Rotzoll die Vorgehensweise. „Ohne diese Werte im Vorfeld zu kennen, haben wir uns mit dem identischen und mit unseren Technologien gefertigten Formeinsatz dem Benchmarking gestellt.“
Alle Werkstücke wurden kontur- und auswerferseitig komplett vermessen. „Wir haben alle Durchmesser der H7-Passungen gebohrt.“ Alle Kunden hatten hingegen die Startlöcher per Elektrode hergestellt und das Endmaß dann klassisch drahterodiert. „Wir waren mit allen Bohrungen stets in der Toleranz, viele Kunden auch, einige hingegen nicht.“ Es sollte damit keinesfalls die Botschaft ankommen, sie könnten alles besser, betont Rotzoll. „Es ging uns vielmehr darum zu zeigen, wir können die Toleranz halten – und das in einem Bruchteil der Zeit.“
Wie lautet das Fazit des Benchmarks? „Bei der reinen Bearbeitungszeit sind wir bei diesem Teil von rund 28 Stunden, die von unseren Kunden im Durchschnitt ohne Elektrodenfräsen benötigt wurden, auf knapp 10,5 Stunden herunter gekommen“, bringt Schadeck den Unterschied auf den Punkt. „Mit der von uns entwickelten Vorgehensweise hatten wir im Mittelwert also eine Zeitersparnis von rund 60 Prozent erreicht.“ Rechnet man die Liegezeiten von durchschnittlich 300 Stunden mit ein, wird der Unterschied bei der Gesamtdurchlaufzeit noch dramatischer.
Kollege Rotzoll weist auf einen weiteren Aspekt hin: „Werkzeuge dieser Größe haben in der Regel 4-fach-, 8-fach- oder 16-fach-Formen. Darum wurde von uns der Prozess hinsichtlich der benötigten Werkzeuge für acht Einsätze ausgelegt.“ Mit einem Werkzeugsatz ließen sich also acht Einsätze herstellen. Dieser Punkt ist extrem wichtig, auch im Hinblick auf einen Kostenvergleich zu alternativen Fertigungsverfahren. „Denn wenige fertigen im Tagesgeschäft nur einen Einsatz.“
Diesen Aspekt berücksichtigt auch die zum Abschluss des Workshops präsentierte Hochrechnung: Danach betrugen die bisherigen Fertigungskosten des Benchmark-Einsatzes im Mittelwert für eine angenommene 8-Fach-Form hochgerechnet 6.832 Euro. Nach der Production50-Optimierung, also durch Komplettbearbeitung auf einer einzigen Maschine, nur noch 3.400 Euro. Das bedeutet eine Ersparnis von 3.432 Euro oder 49,8 Prozent.
Kontakt: