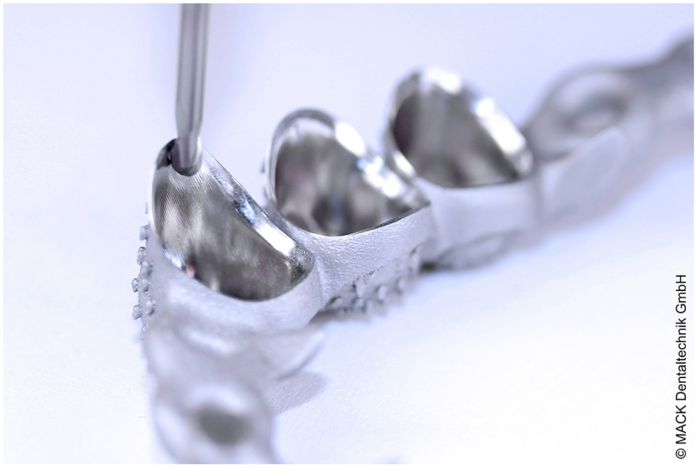
Das BMBF-geförderte Forschungsprojekt TempoPlant trägt zur erheblichen Beschleunigung von Konformitätsbewertungsverfahren mittels der Dokumentation von Fertigungsdaten durch Smart Contracts im Rahmen der neuen Medical Device Regulation (MDR) bei. Ein Forschungsteam des Instituts für Fertigungstechnik und Werkzeugmaschinen (IFW) der Leibniz Universität Hannover entwickelt und erforscht in diesem Zusammenhang eine teilautonome Fertigungszelle für die effiziente Produktion orthopädischer Implantate.
Gestiegene Anforderungen an die Fertigung von Medizinprodukten durch die MDR
Die Produktion medizinischer Implantate stellt im Vergleich zu konventionellen Fertigungsprodukten eine schwierige Aufgabe dar. Herausforderungen sind u.a. schwer zu bearbeitende Materialien, geringe Stückzahlen bis hin zu einer patientenspezifischen Fertigung mit der Losgröße eins und hohe Anforderungen an die Fertigungstoleranzen. Neben fertigungstechnischen Herausforderungen, müssen Hersteller von Medizinprodukten zur Markteinführung zusätzlich großen Aufwand betreiben.
Bevor ein Unternehmen in Europa ein Medizinprodukt auf den Markt bringen darf, müssen einige Schritte durchlaufen werden. Bei der technischen Auslegung des Medizinprodukts muss der Hersteller die Zweckbestimmung des Produkts festlegen und die spezifischen Anforderungen für alle mit dem Produkt zusammenhängenden Prozesse in einem Anforderungskatalog ermitteln.
Im Anschluss an eine klinische Bewertung und Prüfung muss das Konformitätsbewertungsverfahren durchlaufen werden, in dem durch eine benannte Stelle überprüft wird, ob das Produkt alle gesetzlichen Voraussetzungen erfüllt. Nach Erhalt einer Konformitätserklärung kann das Medizinprodukt bei der Europäischen Datenbank für Medizinprodukte (EUDAMED) registriert werden.
Sind diese Schritte erfolgreich durchlaufen, kann das Medizinprodukt in Verkehr gebracht werden. Nach der Markteinführung ist zusätzlich eine Überwachung (Post Market Surveillance) des Produkts vorgeschrieben. So ist der Hersteller zum Beispiel verpflichtet, schwerwiegende Vorkommnisse, die in Zusammenhang mit dem Medizinprodukt stehen, zu melden. Dies können zum Beispiel Implantatdefekte während oder nach der Operation oder negative Reaktionen des Körpers auf das Implantat sein.
Seit dem 26. Mai 2021 wird der Prozess des Inverkehrbringens eines Medizinprodukts von der Auslegung bis zur Überwachung europaweit von der neuen MDR geregelt. Dadurch kommt es beim Prozess des Inverkehrbringens von Medizinprodukten zu einigen tiefgreifenden Veränderungen. Unter anderem fordert die neue MDR eine umfangreichere technische Dokumentation. Dabei sollen Anforderungen an die Auslegung und Herstellung der Produkte, wie die Oberflächenbeschaffenheit und die mechanischen Eigenschaften der eingesetzten Werkstoffe dokumentiert werden.
Die Erfüllung der umfangreicheren technischen Dokumentation hat einen enormen Aufwand zur Folge, wodurch Neuentwicklungen erheblich erschwert werden. Laut einer Umfrage des Bundesverbands Medizintechnologie im September 2021 gaben 55 % der 88 befragten Unternehmen an, dass bisherige Lieferanten unrentabel gewordene Geschäftstätigkeit aufgrund der harten Auflagen der neuen MDR bereits eingestellt haben.
Über 70 % der befragten Unternehmen haben aus demselben Grund bereits einzelne Medizinprodukte oder ganze Produktlinien eingestellt. Rund 60 % aller befragten Unternehmen berichten über einen Anstieg der Kosten und der Dauer eines Konformitätsbewertungsverfahrens, wobei sich die Kosten für das Verfahren verdoppelt haben.
Zur Beschleunigung des Konformitätsbewertungsverfahrens und Verringerung der Kosten für das Verfahren wurde im Projekt TempoPlant eine Fertigungszelle entwickelt, die in der Lage ist, die von der MDR geforderte technische Dokumentation automatisiert direkt nach Abschluss des Fertigungsprozesses bereit zu stellen.
Teilautonome Fertigungszelle für Implantate
Am Beispiel von orthopädischen Implantaten und Dentalbrücken erforscht ein Forschungsteam des Instituts für Fertigungstechnik und Werkzeugmaschinen der Leibniz Universität Hannover zusammen mit fünf Industriepartnern eine teilautonome Fertigungszelle zur wirtschaftlichen Herstellung von medizinischen Produkten. Realisiert wird dies durch eine Kombination des Fertigungssystems und der Messtechnik zur Qualitätskontrolle sowie durch die digitale Anbindung aller Teilsysteme zur durchgängigen Dokumentation der relevanten Fertigungsdaten.
Für die Herstellung der Implantate erforschen die Projektmitarbeitenden Methoden der Digitalisierung sowie innovative Fertigungstechnik und wenden sie entlang der gesamten Prozesskette an. Die Digitalisierung beginnt beim Einsatz von Produkt- und Fertigungsinformationen (PMI), die technische Zeichnungen in der Arbeitsvorbereitung obsolet machen. Ein Automatisierungsroboter übernimmt das Bauteilhandling. Dabei wird das Bearbeitungszentrum DMG MORI Milltap 700 mit Rohteilen be- und den fertigen Bauteilen entladen.
Ein Messroboter, welcher mit einem optischen Messsystem ausgestattet ist, führt die Geometriemessung unmittelbar nach der Fertigung durch. Geometrieelemente des Bauteils, die optisch nicht prozesssicher erfasst werden können, werden im Bearbeitungszentrum zusätzlich taktil gemessen.
Zu einer Qualitätskontrolle im Anschluss an die Fertigung findet automatisiert ein Soll-Ist-Vergleich zwischen den gemessenen und gewünschten Formabweichungen statt. Dabei werden für die gewünschten Formabweichungen die PMI-Daten aus der Arbeitsvorbereitung verwendet. Alle Fertigungs- und Messdaten werden zu Dokumentationszwecken eindeutig jedem Implantat zugeordnet und zusammen mit allen weiteren prozessbegleitenden Daten dokumentiert.
Vollautomatische Dokumentation zur Beschleunigung von Konformitätsbewertungsverfahren
Die Grundlage für das Konformitätsbewertungsverfahren zum Inverkehrbringen von Medizinprodukten stellt die technische Dokumentation dar. Laut MDR gehören zur technischen Dokumentation vollständige Informationen zu den Herstellungsprozessen, den Prozessvalidierungen, den verwendeten Hilfsstoffen, den laufenden Überwachungen und den Prüfungen des Endprodukts.
Im Projekt TempoPlant werden alle Daten, die das Medizinprodukt betreffen, aus den einzelnen Prozessschritten der Fertigung, von der Produktionsvorbereitung bis hin zur Qualitätskontrolle, gespeichert. Die Daten werden automatisiert, transparent und nachvollziehbar abgelegt. Dadurch entfällt eine manuelle Dokumentation. Die Überprüfung durch eine benannte Stelle, ob das Produkt alle gesetzlichen Voraussetzungen erfüllt, wird erheblich vereinfacht.
Im Forschungsprojekt werden die Fertigung von Dentalprothesen und Handgelenksendoprothesen als Anwendungsfälle für Medizinprodukte betrachtet. In diesen Szenarien startet der Fertigungsprozess und die Dokumentation bei Auftragsbeginn mit dem Anlegen einer Auftragsnummer bzw. der sog. Unique Device Identification (UDI). Die UDI ist eine einzigartige Identifikationsnummer, die es erlaubt das Medizinprodukt vom Hersteller bis zum Anwender während des ganzen Produktlebenszyklus zu verfolgen.
Ein Software Dokumentations-Agent legt daraufhin eine bestimmte Ordnerstruktur für den Arbeitsauftrag an. In dieser Struktur werden gleichzeitig Verknüpfungen zu den relevanten Dokumenten angelegt, die nicht auftragsspezifisch sind. Das betrifft beispielsweise die Implantat-Produktakte mit Informationen zur vorausgegangenen Implantatentwicklung, zum Gebrauch und der Risikoklasse des Implantats oder Daten zur Validierung der Mess- und Herstellungsverfahren, die bereits vor dem Fertigungsprozess vorliegen.
Während der Fertigungsprozess durchlaufen wird, werden Daten manuell oder automatisiert aus der Produktionsvorbereitung, der Auftragsplanung, dem Fertigungsprozess und der Qualitätskontrolle in die entsprechenden Ordner gespeichert.
Der Abschluss eines jeden Prozessschritts wird vom Bearbeitungszentrum durch einen Trigger mit einem M30 Befehl im G-Code ausgelöst. Damit wird nach jedem Prozessschritt ein sog. Smart Contract erzeugt, der mit Hilfe der Microsoft Azure Blockchain Workbench implementiert wurde. Smart Contracts sind Computerprotokolle, die nachfolgende Prozessschritte nur auslösen, wenn definierte Bedingungen erfüllt sind. Mit Hilfe der Blockchain wird die Struktur der dokumentierten Daten fälschungssicher nachverfolgt. Damit wird jede Änderung transparent und nachvollziehbar dargestellt.
Nach dem Ende eines Fertigungsauftrags wird der letzte Smart Contract ausgelöst, woraufhin die vollständige Dokumentation für die jeweilige Auftragsnummer abgeschlossen ist. Ein großer Vorteil in der Struktur mit einzelnen Smart Contracts zwischen den Teilprozessen ist die Möglichkeit zur Skalierung. Während im nachfolgenden Bild beispielhaft eine kleine Prozesskette dargestellt ist, kann der Prozess auch aus mehreren Teilschritten bei verschiedenen Firmen und Zulieferern bestehen.
Fazit
Digitale Technologien bergen ein großes Potenzial, den erschwerten regulatorischen Anforderungen in der Medizintechnikbranche gerecht zu werden. Das vorgestellte Forschungsprojekt TempoPlant erleichtert mit Hilfe einer automatisierten technischen Dokumentation das Verfahren der Konformitätsbewertung für Hersteller medizinischer Produkte.
Damit ist eine wirtschaftliche Fertigung auch kleiner Losgrößen möglich, was zu einer bestmöglichen und schnellen Versorgung der Patienten beiträgt. Dies gelingt mit Hilfe einer teilautonomen Fertigungszelle, die mittels Blockchain-Technologie die Daten aller Prozessschritte mit einer höchstmöglichen Transparenz speichert.
Autoren
Prof. Dr.-Ing. Berend Denkena, IFW, Hannover | Dipl.-Ing. Heinrich Klemme, IFW, Hannover | M. Eng. Sebastian Kaiser, IFW, Hannover | Dipl.-Ing. (FH) Martin Winkler, IFW, Hannover | Dipl.-Ing. Maruan Shanib, DMG MORI Digital GmbH
Kontakt: