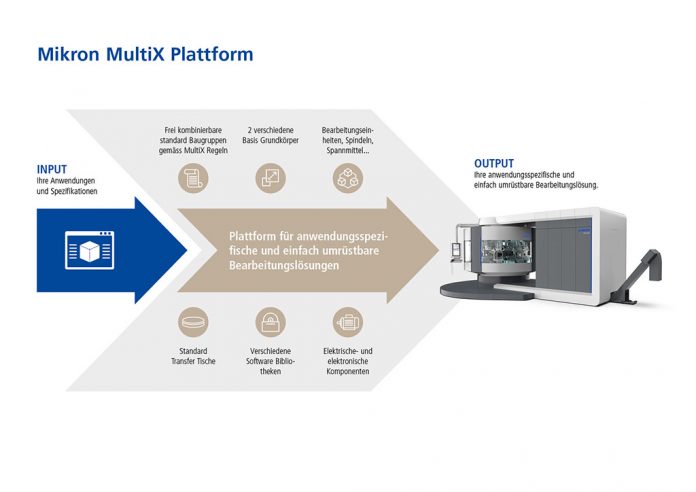
Unter den derzeitigen Marktbedingungen steht der Fertigungsbetrieb immer stärker vor der Forderung, sowohl Hochvolumenproduktionen als auch kleinere Losgrößen gleichzeitig herzustellen. Die MultiX, eine Neuentwicklung der Mikron Machining, bietet ihm die Möglichkeit, auf einer Plattform aus einem Baukasten seine maßgeschneiderte Lösung zu konfigurieren.
Die Plattform schafft damit den Spagat für die leistungsfähige Produktion von 50 bis fünf Millionen Bauteilen. Der modulare Aufbau ermöglicht rasches anwendungsorientiertes Rekonfigurieren der Maschine im Werk des Anwenders. Dadurch erspart sich dieser erhebliche Investitionskosten.
Bei der Rekonfiguration steht ein umfassendes Spektrum von Werkstückspannmöglichkeiten, Bearbeitungseinheiten und Spindeln zur Auswahl. Alle Bearbeitungs- und Spanneinheiten sowie Spindelvarianten sind über alle MultiX-Typen austauschbar. Die sofortige exakte Positionierung der Bearbeitungseinheiten durch ein zum Patent angemeldetes Nullpunktspannsystem trägt erheblich zum schnellen Umrüsten bei.
Breit angelegtes Fertigungsspektrum durch modulares Konzept
Basis der Maschine ist der im Zentrum angeordnete Grundkörper aus einem feststehenden und einem drehbaren Teil. Je nach Anforderungen an die Produktivität, Präzision, Steifigkeit, Rekonfigurierbarkeit, Größe der zu fertigenden Teile etc. wird aus einer der zwei Typen ausgewählt.
Am ausgewählten Maschinenkörper wird je nach Produktionsziel eine Kombination von Werkzeugtransfertischen, Bearbeitungs- und Spanneinheiten sowie Spindeln installiert. Wenn erforderlich lassen sich damit auf derselben Plattform auch ganz unterschiedliche Teile bearbeiten. Dies gilt auch für ausgesprochen komplexe mehrachsige Präzisionsbearbeitungen.
Oben am drehbaren Teil des in zwei Typen verfügbaren Grundkörpers, befinden sich die acht bis 24 Stationen umfassenden Transfertische. Auf ihnen werden die Werkstücke von Station zu Station weitertaktet. Um diese Taktzeiten zu verkürzen, wurde besonderer Wert auf Optimierung der Masse gelegt. Die Transfertische lassen sich sowohl mit fixer, vertikaler Werkstückeinspannung als auch mit vertikalem und horizontalem Motor ausrüsten. Alle Tischarchitekturen sind kombinierbar. Den gewählten Kombinationen entsprechend ergeben sich die vier Kabinendurchmesser 1,8 Meter, 2,6 Meter, 3.6 Meter und 4 Meter.
Der Maschinen-Grundkörper der Type 1 hat einen Transfertischdurchmesser von 1000 Millimetern. Auf ihm finden bis zu 24 Stationen mit Dreiachs-Spanneinheiten der Größe 1 Platz. Die Werkstücke werden von einem Torquemotor mit Tischindexierzeiten von 0,5 bis einer Sekunde durchgetaktet. Der Tisch verfügt über keine Energieversorgung.
Beim Maschinen-Grundkörper der Type 2 kann der Anwender aus Transfertischen der Durchmesser 1300 und 1600 Millimeter wählen. Auf dem Tisch mit 1300 Millimetern finden bis zu 16 Stationen mit Dreiachs-Spanneinheiten der Größe 2 Platz. Beim 1600-Millimeter-Tisch sind es bis zu 24 Stationen, ebenfalls mit Dreiachs-Spanneinheiten der Größe 2.
Beide Varianten können auch über eine Energieversorgung auf dem Tisch verfügen, zum Beispiel für die Antriebsmotoren von Spanneinheiten. Auch hier taktet ein Torquemotor die Werkstücke von Bearbeitungsstation zu Bearbeitungsstation. Eine hochpräzise Hirthkupplung sorgt für besondere Präzision und Stabilität. Wegen des größeren Durchmessers und der größeren zu bewegenden Masse benötigt die Indexierung hier 1,5 bis 2,5 Sekunden.
Die Spannstationen können sowohl mit vertikalen Motoren als auch mit hydraulischen Werkstückeinspannungen ausgerüstet werden. Die Spanneinheiten verfügen über alle erforderlichen Achsen für Drei-, Vier- und Fünf-Achs-Bearbeitungen. Dem jeweiligen Fertigungsschritt entsprechend, können die Werkstücke rotiert, geschwenkt, per Elektro- oder Hydraulikmotor indexiert oder auch einfach in einer bestimmten Position festgehalten werden.
Andere von einem Motor angetriebene Spanneinheiten können das Werkstück für Dreh- oder Fräsoperationen rotieren lassen. Wieder andere sind dazu ausgelegt, das Werkstück während der Bearbeitung besonders stabil zu fixieren. Die Schwenkachsen für Fünfachs-Bearbeitungen verfügen über schnell austauschbare Spanninterfaces.
Schnelles Umrüsten durch Nullpunkt-Spannsystem
Dem Anwender steht ein komplettes Set von Bearbeitungseinheiten in verschiedenen Größen zur Auswahl, welche über alle MultiX-Typen austauschbar sind. Als Montageeinheit mit der Box sind sie über das Nullpunkt-Spannsystem bei der Rekonfiguration sofort präzise positioniert. Wie bereits bei den Grundkörpern erwähnt, gibt es ein Set mit drei Größen von Bearbeitungseinheiten:
- Auf den Transfertischdurchmesser 1000 Millimeter passen bis zu 24 Stationen der Größe 1, oder bis zu 12 Stationen der Größe 2 oder bis zu acht der Größe 3.
- Auf dem Durchmesser 1300 Millimeter lassen sich bis zu 16 Stationen der Größe 2 oder bis zu 12 der Größe 3 unterbringen.
- Der Transfertisch mit Durchmesser 1600 Millimeter lässt sich mit bis zu 24 Stationen der Größe 2 oder mit bis zu 16 Stationen der Größe 3 ausrüsten.
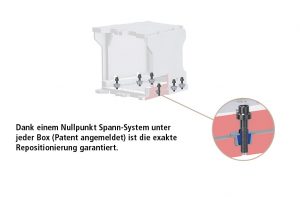
Zur Rekonfiguration ist lediglich der Austausch der bis zu drei Bearbeitungseinheiten umfassenden Boxen erforderlich. An der Unterseite der Boxen befindet sich das Nullpunkt-Spannsystem. Seine Präzision ist ein wesentlicher Aspekt bei der schnellen und kostensparenden Rekonfiguration der Maschine, die nun nicht mehr im Herstellerwerk, sondern beim Anwender vorgenommen wird. Dies trägt erheblich zur Investitionssicherheit bei.
Vertikal-, Horizontal- oder Universal-Dreiachs-, Zweiachs- oder Monoachs-Bearbeitungseinheiten stehen in mehreren Größen zur Auswahl. Zusammen mit der umfangreichen Palette von Spindeln, kann damit eine Vielfalt von Dreh-, Fräs- oder Bohroperationen kombiniert werden.
Zur Auswahl gehören Motorspindeln, Hochleistungselektrospindeln, Doppel- und Mehrfachspindeln, aber auch Spindeln mit U-Achse oder Winkelköpfe und anwendungsspezifisch gestaltete Achsen. Mit der richtigen Kombination von Bearbeitungsspindeln sowie Spann- und Bearbeitungseinheiten können auch Teile mit komplizierten Geometrien durch Dreh-, Fräs- und Entgratprozesse hergestellt werden.
Automatische Werkzeugwechsler ATC (Automatic Tool Changers) sind für Transfermaschinen ein Alleinstellungsmerkmal (USP Unique Selling Point). Es gibt ATC mit vier in die Spindel integrierten Werkzeugen oder mit acht auf einer horizontalen Scheibe oder mit 20 auf einer horizontalen Kette. Alle sind radial so hinter der jeweiligen Bearbeitungseinheit angeordnet, dass der Sektor dieser Bearbeitungseinheit keinen zusätzlichen Platz benötigt.
Anstelle einzelner Bearbeitungseinheiten sind auch Messtaster für die laufende Qualitätssicherung einsetzbar. Auf diese Weise können schon bei Maßabweichungen innerhalb der Toleranzgrenzen entsprechende Korrekturen erfolgen.
Je eine Station ist für die Beschickung der Maschine mit Rohlingen und die Entnahme der fertigen Werkstücke erforderlich. Dies kann per Roboter oder mit Handlingsystemen erfolgen, die Beschickung auch direkt von der Rohmaterialstange ist möglich.
Modular organisierte Steuerungssoftware
Die NC Steuerung der Maschine ist für komplexe Präzisionsbearbeitungen mit hohen Geschwindigkeiten optimiert. Werden neue Bearbeitungseinheiten montiert, sind auch die entsprechenden Bausteine für die modular organisierte Steuerungssoftware zu installieren. Über standardisierte Schnittstellen erkennt die Steuerungssoftware dann selbsttätig die neuen Bearbeitungseinheiten. Mikron weist besonders auf das modulare Softwarepaket und das komfortable Mensch-Maschine-Interface hin, sowie auf deren schnelle Adaptierbarkeit an jede Maschinenkonfiguration.
Zusätzliche Software-Optionen ermitteln laufend die Möglichkeiten zur Verkürzung der Zykluszeiten. Standardisierte mechatronische Elemente der Software unterstützen den Maschinenbediener in allen Phasen des Bearbeitungsprozesses und der Produktionsplanung.
Weitere Unterstützung erfolgt durch statistische Prozesskontrolle (SPC), automatisches Korrekturmanagement und Systemdatensicherung. Das in die Steuerung integrierte miS4.0-Modul ist ein Industrie-PC, der Daten sammelt, speichert und standardisiert. Damit hat der Anwender stets kompletten Überblick und Kontrolle über Produktion und vernetzte Maschinen.
Drei Beispiele aus unzähligen Varianten
Folgende drei Konfigurationsvarianten sollen aus der Vielzahl von Möglichkeiten der MultiX herausgehoben werden:
Die MultiX S-24 hat einen Kabinendurchmesser von 2,6 Metern. Das „S“ dieser Variante steht für Speed, also für Geschwindigkeit und Produktivität bei hochvolumiger Produktion von Kleinteilen, beispielsweise Buchsen für die Automobilindustrie. Typischerweise haben diese einen Durchmesser von 20 und eine Länge von 60 Millimetern. Sie können auf 24 Stationen durch Dreiachsen-Bearbeitungszentren im Doppelzyklus gleichzeitig von oben und unten bearbeitet werden. Zur Drehbearbeitung verfügt diese Variante über rotierende Spannzangen.
Die MultiX P-16 hat einen Kabinendurchmesser von vier Metern. Das „P“ (Power) weist auf die besondere Eignung für die Hochvolumenproduktion faustgroßer also grösserer Teile, typischerweise mit Durchmesser 40 und Längen von 80 Millimetern hin. Das können zum Beispiel Pumpengehäuse für die Kraftstoff-Direkteinspritzung bei Verbrennungsmotoren sein. Gemäß den Dimensionen der Werkstücke und Bearbeitungseinheiten geschieht hier die Indexierung mittels höchst steifer und wiederholgenauer Hirth-Verzahnung.
In jeder der 16 Stationen sind Dreiachsen-Bearbeitungseinheiten am Werk. ATC – Automatische Werkzeugwechsler sorgen dafür, dass in den mit Hohlschaftkegeln HSK-63, -40 oder -32 ausgerüsteten Spindeln immer das richtige Werkzeug steckt. Bearbeitungen von unten erfolgen durch verfahrbare Mehrspindelköpfe, da sonst während des Werkzeugwechsels die Hohlschaftkegel verunreinigt würden.
Die MultiX C-8, ebenfalls mit Kabinendurchmesser vier Meter, wurde sowohl für höchste Flexibilität als auch für Massenproduktion konfiguriert, also zum Beispiel für Lohnfertigungsbetriebe oder Auftragsfertigungen. Die typische Teilegröße von 80 Millimetern Durchmesser und 80 Millimetern Länge eröffnet umfassende Möglichkeiten für ein breites Werkstückspektrum.
Auf ihren acht Stationen können Teile von Baugruppen, aber auch ganz unterschiedliche Teile zur gleichen Zeit bearbeitet werden. Die gleichzeitige Bearbeitung unterschiedlicher Teile spart Umrüstzeiten. Bei diesem Beispiel ist die Maschine mit vier horizontalen Spanneinheiten für das Drehen von Teilen ausgerüstet sowie mit vier Fünfachs-Fräseinheiten mit HSK-63, -40 oder- 32.
Grundrisse für bestmögliche Platznutzung
Es gibt die Kabinendurchmesser 1,8 Meter, 2,6 Meter, 3,6 Meter und 4 Meter. Wie die beschriebenen Beispiele zeigen, ergibt sich der Durchmesser aus der Anzahl und Größe der gewählten Werkstückspann- und Bearbeitungseinheiten. Drei Layoutvarianten der etwa dreieinhalb Meter hohen Maschine ermöglichen dem Anwender die bestmögliche Nutzung seiner Platzverhältnisse. Bei der klassischen ist der Schaltschrank rückseitig angeordnet. Deshalb hat die etwa dreieinhalb Meter hohe Maschine einen nahezu quadratischen Platzbedarf.
Bei der kompakten Layoutvariante ist der Schaltschrank in zwei hintereinander angeordneten Modulreihen auf der rechten Seite der Maschine untergebracht. Deshalb ist der einem Rechteck ähnliche Grundriss auf dieser Seite kürzer als bei der erweiterten Layoutvariante, bei welcher alle Schaltschrankmodule nebeneinander angeordnet sind. Diese Variante ist zwar schmaler als die beiden anderen, erstreckt sich aber länger nach der rechten Seite. Die erweiterte Variante findet hauptsächlich Anwendung bei der Stangenbeladung, die entlang des Schaltschrankes über dem Späneförderer ergonomisch angeordnet wird.
Mikron auf der EMO 2019 in Halle 17, Stand C67.
Kontakt: