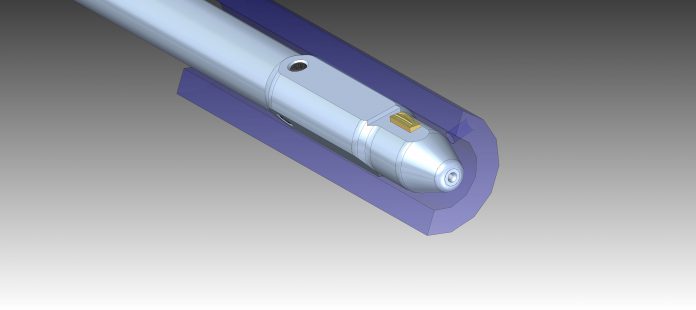
Einer der größten europäischen Automobilhersteller produziert an seinem Getriebestandort in Deutschland Antriebs- und Zwischenwellen für ein 6-Gang-Handschaltgetriebe für das höherwertige mittlere Verkaufssegment. Die fehlende Prozesssicherheit bei der Entgratung der Querbohrungen und der resultierende Kostendruck veranlassten die Verantwortlichen, nach alternativen Lösungen zu suchen. Als Entgratspezialist und möglicher Partner war die HEULE Werkzeug AG beim Automobilgiganten bereits ein Begriff, aber das von HEULE vorgeschlagene Funktions-/Werkzeugprinzip völlig unbekannt.
Der bisherige Entgratprozess von mehreren Radialbohrungen Ø3.0 mm mit einem modifizierten Tieflochbohrer über die Hauptbohrung konnte die Qualitätsanforderungen nicht erfüllen. Einerseits drückte das starre Werkzeug die verbundenen Bohrkappen z.T. zurück in die Querbohrungen, andererseits lösten sich beim anschließenden Härteprozess die Gratwurzeln. Solche verbleibenden Bohrkappen können die Funktion des Getriebes stören oder diese sogar verhindern. Zur Absicherung der Qualität integrierte der das Werk eine 100%-Kontrolle in die Fertigung, dessen Eliminierung sich der Kunde nun zum Ziel machte, um die Prozesssicherheit zu erhöhen.
Gleich mehrere Unternehmen wurden parallel angefragt, eine Alternativlösung anzubieten. Bereits vor der ersten Projektbesprechung hatte HEULE Gelegenheit, ihre Entgrat-, Fas- und Senklösungen einem grösseren Personenkreis am Standort in Deutschland vorzustellen. Zu diesem Wissen kamen laut dem Projektverantwortlichen die durchwegs guten Erfahrungen mit der Entgratung von Getriebewellen an den asiatischen Fertigungsstandorten hinzu.
Konsequenter Projektablauf zielführend
„Beim nächsten Projekt würde ich die Getriebewellen gleich selber vorbeibringen“, meinte der Projektverantwortliche zur Frage des noch offenen Besuchs bei HEULE. Trotz hohem Zeit- und Erfolgsdruck war die Erkenntnis als auch die Akzeptanz beim Automobilhersteller vorhanden, den Entwicklungsschritten den entsprechenden Zeitbedarf zuzugestehen.
Waren doch die Versuche mit dem ersten Werkzeugprinzip zwar vielversprechend, erfüllten aber die Kundenanforderung noch nicht ganz.
Diese ersten Entgratresultate betrachtend meinte HEULE Entwicklungsleiter Harry Studer: „Jetzt verändere ich dieses Durchdringungsmesser so, wie ich es schon länger machen wollte“. Diese manuelle Anpassung des Schneidprinzips führte zu Resultaten, die überzeugten. Jetzt galt es, diese manuelle Messeroptimierung im maschinellen Schleifprozess prozesssicher nachzustellen, um Messer zu erhalten, die das Entgratresultat wiederholen konnten. Diese und auch die folgenden Entwicklungsschlaufen erledigte HEULE immer in der Terminvorstellung des Kunden. Es bewährte sich der Entscheid, die Versuche im HEULE-Entwicklungscenter zu fahren und nicht auf der Fertigungslinie des Kunden.
Schälender Schnitt entfernt die Bohrkappen
Die Kundenforderung, das Entgratwerkzeug in das bestehende Maschinenkonzept zu integrieren, gab bei HEULE den Ausschlag, diese Aufgabe mit der neuen X-BORES-Technologie lösen zu wollen. Das in Asien bewährte COFA-Werkzeug konnte aufgrund der fehlenden Radialspindel nicht eingesetzt werden. Eine Nachrüstung der Maschine mit dieser Spindel kam aus verschiedenen Gründen nicht in Frage.
Konkret kam SNAP-X zur Anwendung – eines der vier Funktionsprinzipien der X-BORES-Technologie. Das SNAP-X-Messer ist mit rechts- und linkslaufender Schneide ausgebildet. Diese hat ein konvexe, der Querbohrung angepasste Form. Sie dringt – geometrisch begrenzt durch den Radius der Schneidkante oder die Länge des Messers – in die Querbohrung ein. Durch die Konstellation der beiden Kreissegmente (Querbohrung und Schneide) ist das Messer in der Lage, sich kontinuierlich aus der Querbohrung herauszuarbeiten und führt dabei gleichzeitig die im Schälschnitt wirkende Entgratarbeit durch.
Basierend auf dem bewährten SNAP-Prinzip wird das Messer durch Federkraft an die Bohrungswand gedrückt. Für eine saubere Entgratung der beiden Radialbohrungsflanken wird im Rechtslauf in die Hauptbohrung eingefahren und im Linkslauf wieder herausgefahren. An den Positionen der Radialbohrungen wird die Drehzahl belassen und der entsprechende Arbeitsvorschub eingestellt. Die Wege zwischen den Bohrungen werden im Eilgang verfahren.
Messerwechsel ohne Stillstandzeit
Nebst der prozesssicheren Entgratung, welche die Eliminierung der 100% Kontrolle erlaubt, war für den Kunden auch die sichere, fehlerfreie Handhabung des Werkzeugs ein wichtiger Aspekt. „Uns hat das sehr einfache und simple Werkzeug, mit praktisch null Fehlerpotential, einen Messerwechsel direkt in der Maschine ermöglicht“, meinte der Fertigungsverantwortliche überzeugt. Auch dieser Umstand hat die bisherige Lösung übertroffen. Das Entnehmen des Werkzeugs und das Wechseln außerhalb hätte deutlich mehr Zeit in Anspruch genommen. Durch die Kombination der taktzeiterfüllenden Bearbeitungsparameter und der robusten, beschichteten Hartmetallmesser konnte die Standzeit unter Serie-Bedingungen verdoppelt werden. Dies hat die Stillstandzeit für den Messerwechsel proportional halbiert, was wiederum die Linienausbringung positiv beeinflusst hat.
Erfolgsfaktor Entwicklungspartnerschaft
Durch die gegenseitig unterzeichnete Geheimhaltungserklärung konnte offen und direkt kommuniziert werden. Auf die Frage, was auch zum Erfolg der vorliegenden Entgratlösung führte, meinte der Projektverantwortliche: „Man spürt das HEULE will – alle Projektbeteiligten suchten eine Lösung für den Kunden“. Hier kam die Firmenphilosophie von HEULE zum Tragen: alle Projektbeteiligten waren mit der Thematik durch und durch vertraut und konnten durch tiefes Fachverständnis und Entgratungs-Knowhow überzeugen. Auch das bei HEULE neu installierte Key Account Management erwirkte in enger Zusammenarbeit zwischen Kunde, HEULE-Vertretung und HEULE-Entwicklung ein klar abgestimmtes Vorgehen, ein sauberes und detailliertes Erfassen der Anfrage, das Erarbeiten der richtigen Fragen und einen reibungslosen Informationsfluss.
Die beiden Werkzeuge der Antriebs- und Zwischenwelle verrichten seit mehreren Monaten zuverlässig ihren Dienst. Was HEULE besonders freut ist die Aussage von dem Projektverantwortlichen des Automobilherstellers: „Wir wünschen uns bei Themen wie beispielsweise Entgratung und Prozessoptimierung weitere Berührungspunkte – zukünftige Kontakte sind sicher.“
Kontakt: