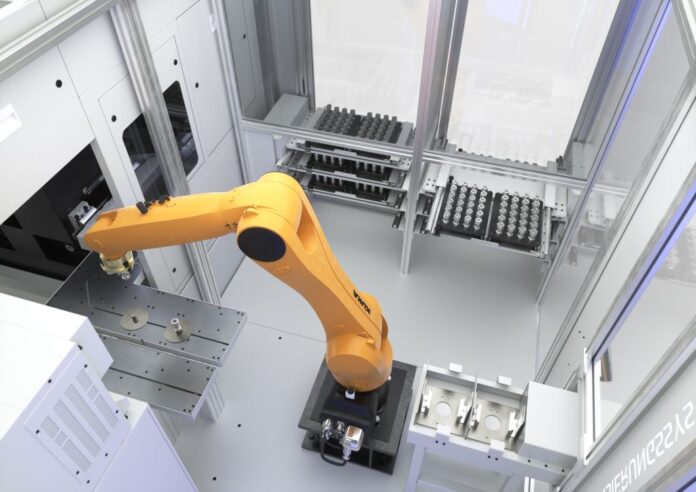
Rund 3,5 Millionen Roboter sind mittlerweile weltweit in der industriellen Produktion im Einsatz, so der „World Robotics 2022“-Report der International Federation of Robotics (IFR). Dabei zählt Deutschland zu den fünf größten Robotermärkten der Welt. Warum das so ist, zeigen aktuelle Beispiele von EMAG: Die Spezialisten kombinieren ihre Hochleistungsmaschinen mit ganz verschiedenen Roboterzellen – und sorgen so nicht nur für hocheffiziente Prozesse bei der Be- und Entladung der Maschinen, sondern integrieren auch zusätzliche Stationen rund um Qualitätssicherung, Beschriftung, Reinigung und einiges mehr.
Ganzheitliche Fertigungslösungen
Doch was ist die übergreifende Zielsetzung bei EMAG, wenn Roboter zum Einsatz kommen? „Im Zentrum stehen immer die Anforderungen des Werkstücks und des dazugehörigen Produktionsprozesses“, erklärt Jürgen Maier, Leiter der Business Unit Drehen bei EMAG. „Entscheidende Fragen sind dabei zum Beispiel, welche Losgrößen in einem bestimmten Zeitraum gefertigt werden und wie autark die Lösung arbeiten soll. In jedem Fall sind wir sehr flexibel und passen uns in vielfacher Weise an die vorhandene Produktionsumgebung oder die Platzverhältnisse an.“
Mit Abführbändern, Palettierern oder Schubladen
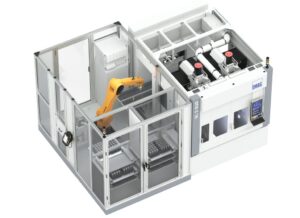
Wie unterschiedlich die individuellen Roboterlösungen von EMAG sind, zeigt ein Blick auf Details: Die Zuführung der Teile kann zum Beispiel über Förderbänder, in Paletten, auf Werkstückträgern wie zum Beispiel Körben oder sogar als Schüttgut erfolgen – mithilfe dieser Systeme „bedient“ sich der Roboter, wenn er neue Teile aufnimmt bzw. fertig ablegt, wobei jede Lösung andere Stärken und Grundbedingungen aufweist. So sind Gurt- oder Scharnierbänder beispielsweise eine ideale Variante, wenn der Teilefluss reibungslos von einer vorgelagerten Produktionslösung zur EMAG-Maschine erfolgen soll. Der Roboter kann die Teile dann einfach vom Band abgreifen und später wieder ablegen, wobei die Bänder in unterschiedlicher Weise angeordnet werden – je nach Platzsituation oder gewünschtem Teilefluss. Pneumatische Stopper sorgen für die Vereinzelung der Teile. Zudem ist es möglich, die Werkstück-Ausrichtung auf dem Band per Kamera zu erkennen. Beim Bin Picking, dem sogenannten „Griff in die Kiste“, können die Rohteile sogar komplett chaotisch, also als Schüttgut zugeführt werden. Ein 3D-Kamerasystem ermittelt dann aus einer aufgenommenen Punktewolke sowohl Position als auch Orientierung jedes einzelnen Werkstücks und berechnet daraus die jeweils optimale Anfahrstrategie für den Roboter. Diese Technologie eignet sich daher perfekt für den Einsatz ganz am Anfang der Wertschöpfungskette, da dadurch eine manuelle Vororientierung der Rohteile komplett entfallen kann.
Im Unterschied dazu setzt der Einsatz von Palettierern einen „geordneten“ Start voraus: Dabei erfolgt die Be- und Entladung des Systems zum Beispiel über einen Korb-Wagen. Er enthält übereinander gestapelte Gitterkörbe mit entsprechenden Formnestern, in denen sich die Teile befinden – also eine relativ große Menge pro Wagen, den ein Bediener einfach in eine definierte Position schiebt, von der aus der Roboter zugreifen kann. Der Wagen mit Fertigteilen befindet sich an einer anderen Position. „Es kommt bei einer solchen Lösung unter anderem darauf an, dass man die Taktzeit der EMAG-Maschine und die gewünschten Mannstunden an der Maschine miteinander in Relation setzt“, erklärt Maier.
Eine dritte Variante wäre die Beladung per Schubladensystem: Hier werden die Werkstücke in kundeneigenen Werkstückträgern über pneumatisch angetriebene Schubladen dem Arbeitsraum des Roboters zugeführt. Die Schubladen sind übereinander angeordnet, wodurch bei gleichem Footprint ein höheres Speichervolumen und somit eine höhere Autonomie erzielt wird. Im Übrigen kann der Wechsel der Werkstückträger durch den Bediener komplett taktzeitparallel erfolgen. Der Roboter kann dadurch auch bei offener Beladetür weiterarbeiten, womit Unterbrechungen in der Produktion vermieden werden.
Zahl der Roboterlösungen von EMAG nimmt zu
Für alle diese Lösungen gilt: Die Ausstattungsmöglichkeiten der einzelnen Roboterzelle sind groß. So ist es etwa denkbar, eine Statistische Prozesskontrolle (SPC) zu integrieren. Hier werden im einfachsten Fall einzelne Teile zur Qualitätssicherung regelmäßig ausgeschleust, vermessen und wieder eingeschleust. Darüber hinaus kann aber auch die Messstation selbst in die Zelle integriert werden, sodass die Messung inklusive Messwerkrückführung zur Maschine komplett automatisiert ablaufen kann.
Ebenso ist es möglich, kamerabasierte Prüfsysteme, ein Greiferwechselsystem inklusive Greiferbahnhof für die Verarbeitung eines großen Werkstückspektrums, kleine Wasch- und Reinigungsstationen, Entgratsysteme oder Laser- bzw. Gravierstationen innerhalb der Roboterzelle zu platzieren. Die jeweilige Station wird dann ebenso vom Roboter be- und entladen. Es ergibt sich also ein kontinuierlicher Teilefluss über verschiedene Technologien hinweg.
Ähnlich wichtig ist die virtuelle Inbetriebnahme – also das Erproben der Abläufe und Schnittstellen am digitalen Zwilling der Fertigungslinie. So lassen sich unvorhergesehene Fehler aufdecken und in einer frühen Entwicklungsphase beseitigen. Und: Die „reale“ Inbetriebnahme läuft später viel schneller ab.
„Insgesamt kann man sicher sagen, dass immer mehr Roboterlösungen an unseren Maschinen zum Einsatz kommen, was allerdings auch naheliegend ist“, fasst Jürgen Maier zusammen. „Die manuellen Tätigkeiten entlang der Wertschöpfungskette werden also kontinuierlich weniger. Das ist unser Ansatz, der immer mehr Kunden überzeugt.“