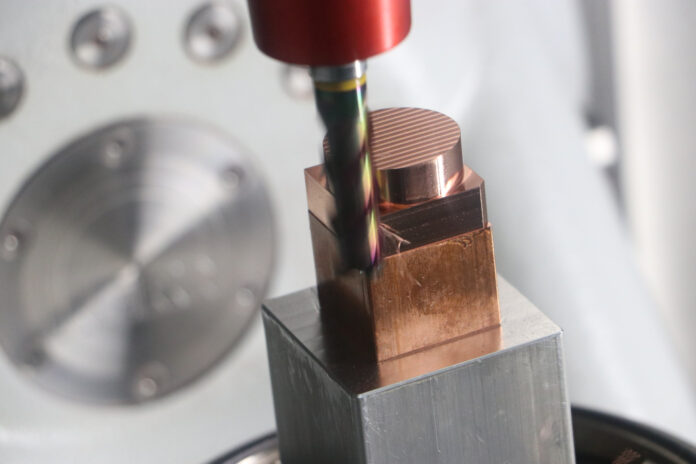
Wenn es in modernen Fahrzeugen heißt, „es werde Licht“, dann stecken nicht selten Highend-Linsen von Vema dahinter. Denn der mittelständische Familienbetrieb produziert diese Produkte in verschiedensten Ausprägungen für führende Automobilhersteller. Darüber hinaus zählen andere anspruchsvolle Branchen wie Sanitär- und Medizintechnik zum großen Kundenkreis des in Krauchenwies (Baden-Württemberg) ansässigen Unternehmens.
Vema ist ein Komplettanbieter, der sich bereits bei der Gründung vor gut 40 Jahren ein paar Grundsätze auf die Fahnen schrieb, die bis heute gelten. Werkzeugbaumeister Werner Veser, Geschäftsführer und einer der Gründer, erklärt: „Mein Gründungspartner Josef Macho und ich waren uns von Anfang an einig. Erstens: Wir bieten Beratung, Werkzeug-/Formenbau und Kunststoffspritzguss aus einer Hand. Zweitens: Bei uns gibt es Präzision auf höchstem Niveau. Das hat sich damals als goldrichtig erwiesen und ist immer noch ein Garant für unseren Firmenerfolg“.
Was also in 1982 als Zweimannbetrieb in einer Garage begann, ist jetzt ein Familienunternehmen mit 75 Mitarbeitern, das sich 2012 mit dem Einstieg des Gründersohnes Christian Veser neu aufstellte. Gemeinsam mit seinem Vater setzte der Wirtschaftsingenieur den Bau neuer Hallen auf der grünen Wiese um, führte digitale Prozesse ein und sorgte durch verschiedene Maßnahmen für maximale Energieeffizienz in seinem Unternehmen.
„Wir haben auf allen Hallen Photovoltaik installiert und nutzen die Abwärme unserer Maschinen zur Warmwasserbereitung, um nur ein paar Beispiele zu nennen“, sagt Christian Veser und ergänzt: „Wir investieren aber auch in allen anderen Belangen in moderne Technologien.“ So hilft etwa eine Ultraschallreinigungsanlage dabei, die gut 600 selbstverwalteten Formwerkzeuge sauber und einsatzbereit zu halten.
Mit Kern Micro HD langgehegten Traum erfüllt
Mit einer anderen Investition erfüllte sich Werner Veser im Jahr 2022 einen langgehegten Traum, wie er lächelnd erzählt: „Ich schau mir schon seit 20 Jahren auf Messen die Bearbeitungszentren von Kern an, konnte mich aber aufgrund der nicht gerade günstigen Preise nicht zum Kauf durchringen. Jetzt habe ich gemeinsam mit meinem Sohn neu kalkuliert, und wir sind sicher, dass sich die Investition in unser Highend Fünfachszentrum Kern Micro HD lohnt.“
Entscheidend dafür seien vor allem die extrem hochwertigen Ergebnisse in puncto Oberflächenqualität und Genauigkeit, die sich mit der Kern Micro HD erzielen lassen. Ein Beispiel verdeutlicht, warum diese Kriterien so wichtig sind. Vema produziert für führende Pkw-Hersteller Kunststofflinsen, die in Scheinwerfern oder anderen Beleuchtungseinheiten im Interieur und Exterieur zum Einsatz kommen. Für einen optimalen Ein- und Ausfall des Lichts sind zum einen teure Kunststoffe mit hohem Transmissionswert (Lichtdurchlässigkeit) von 95 Prozent notwendig. Zum anderen braucht es – vor allem in Scheinwerferlinsen – perfekte Oberflächen.
Diese im Kunststoff abzubilden, ist wiederum nur mit Formeinsätzen möglich, die ihrerseits hochgenau sind und vor allem an den relevanten Stellen mit höchster Oberflächenqualität aufwarten. Ein Anspruch, der bis vor einem Jahr ausschließlich durch händisches Polieren erfüllt werden konnte.
Hundertprozentige Polierqualität direkt aus der Maschine
Richtig glücklich war der Seniorchef mit den früheren Prozessen nie: „Davon abgesehen, dass ich niemanden kenne, der gerne von Hand poliert, sind an unseren Formen manche Stellen schwer zugänglich, so dass das nicht immer auf den ersten Rutsch passte.“ Zudem ist es beim Polieren wichtig, zwischen den Linsen polierte scharfe Kanten zu erzeugen, um beim späteren Einsatz in Fahrzeugen einen perfekten Lichtstrahl zu gewährleisten. Eine weitere Herausforderung, die mitunter mehrmalige Nacharbeit erfordert.
„Seitdem wir die Kern Micro HD mit dem MHT-Mediumverteiler im Einsatz haben, gibt es diese Probleme nicht mehr. Jetzt kommen stets perfekte Bauteile in polierter Oberflächenqualität direkt von der Maschine, ohne jegliche Nacharbeit. So konnten wir die Durchlaufzeiten um 20 bis 30 Prozent reduzieren – bei besserer Qualität.“
Bevor Kern den Zuschlag bekam, haben Werner Veser und sein Mitarbeiter Luca Bornhorst – angehender Werkzeugbau-Meister – viele Anbieter verglichen. Aber: „Keiner konnte unsere gewünschten Probewerkstücke mit vergleichbarer Oberflächenqualität herstellen wie Kern“, sagt Bornhorst. Dabei sei die Micro HD auch im Hinblick auf die erreichbare Präzision einzigartig. „Nach den ersten ‚Probeschüssen‘ auf unseren Kunststoffspritzgießmaschinen kommt es natürlich vor, dass die Ergebnisse nicht exakt passen.“
An manchen Stellen ist der Kunststoff minimal zu dünn oder zu dick. Ergo gilt es, einzelne Bereiche der Formen nachzuarbeiten, um die aufwändigen Tests im Lichtlabor zu bestehen. „Dabei sprechen wir von ein oder zwei hundertstel Millimeter am gespritzten Teil. Wir spannen die Form also wieder auf und fräsen sie nach. Mit unserer Kern geht das aufs µm genau. Das stimmt am Ende immer, zu hundert Prozent“, freut sich der Meister in spe.
Veser ergänzt dazu, dass ihm auch die Steuerung der Maschine wichtig war. Alle Fräsmaschinen im Unternehmen haben eine Heidenhainsteuerung. Das heißt, jeder Mitarbeiter ist in der Lage die Fräsmaschinen zu bedienen. Das bringt Planungssicherheit im Unternehmen.
Kern Micro HD und MHT-Mediumverteiler harmonieren perfekt
Die Entscheidung für eine Micro HD war also nach zahlreichen Tests und Vergleichen bereits auf der Zielgeraden. Einzig ein wichtiges Kriterium konnte Kern bis dato noch nicht erfüllen: die Integration des MHT-Mediumverteilers.
Vema hatte mit diesem Minimalmengenschmiersystem in der Vergangenheit schon sehr gute Erfahrungen gemacht und wollte auf die Vorteile auch in Zukunft nicht verzichten. Neben der Standzeiterhöhung der Fräswerkzeuge wirkt sich der Mediumverteiler auch signifikant auf die erreichbaren Oberflächenqualitäten aus. Ganz zu schweigen vom „grünen Abdruck“ des Unternehmens. Denn es benötigt keine Emulsion oder Bearbeitungsöle im Werkzeugbau.
Basis des Minimalmengenschmiersystems von MHT, das technisch und physikalisch anders funktioniert als herkömmliche Minimalmengenschmiersysteme, ist ein passgenauer Düsenkörper, mit dem jede Werkzeugaufnahme versehen ist. Eine mit 16 kleinen Luftdüsen versehene rote Hülse dreht sich beim Fräsvorgang nicht mit und sorgt so dafür, dass sich die mit Aerosolen leicht vermischte und mit einem Druck von 6 bar ausgestoßene Luft über das gesamte Werkzeug zieht und an allen Schneiden permanent für eine optimale Schmierung und Kühlung sorgt. Gleichzeitig werden zuverlässig alle Späne weggeblasen.
Für Kern und MHT Grund genug, sich gemeinsam an einen Tisch zu setzen und an einer Lösung zu arbeiten. Vema-Chef Werner Veser erinnert sich und zeigt sich noch heute beeindruckt von der guten Zusammenarbeit: „Beide Unternehmen sind enorm innovativ und immer offen für neue Technologien. Dementsprechend gut ist das gemeinsame Arbeiten gelaufen.“ Trotz einiger technischer Herausforderungen – insbesondere mit dem automatisierten Werkzeugwechsel – ist es den Technikern von Kern und MHT gelungen, eine Lösung zu entwickeln, die perfekt funktioniert.
Mannlos im Dreischichtbetrieb
Da die Kern Micro HD sämtliche Formeinsätze sowie die benötigten Kupferelektroden in einer Aufspannung und verlässlicher Qualität fertigt, hat die Automatisierung auch in diesem Bereich Einzug gehalten. Früher mussten sich die Werkzeugbauer wegen der fehlenden Grundgenauigkeit und Reproduzierbarkeit der Fräsmaschinen immer an das richtige Maß heranarbeiten, mit entsprechend hoher Ausschussquote. „An eine autonome Fertigung war somit nicht zu denken“, bekräftigt Werner Veser: „Heute ist das anders.“
Das interne Werkzeug -und Werkstückwechselkabinett mit 90 Werkzeugen und 30 Werkstücken, ermöglichen es zudem nicht nur komplexe Formen – mit teils 60 Stunden Laufzeit – Tag und Nacht zu bearbeiten. Auch viele kleine Bauteile fertigt die Micro HD im 24/7-Betrieb. Sollten die 30 Werkstückrohlinge künftig nicht mehr ausreichen, ist auch dafür eine Lösung vorbereitet. Denn das Highend-Bearbeitungszentrum verfügt bereits über eine automatische Tür, an die ein externer Werkstückwechsler einfach angedockt werden kann.
Kontakt: