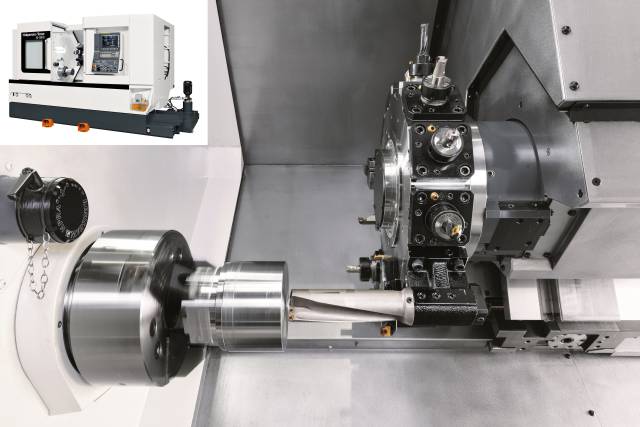
Das 40 Mitarbeiter starke Unternehmen Neiko GmbH & Co. KG aus Herten dürfte deutschlandweit die erste Adresse für die Herstellung von Sonder-Rohrverbindungsteilen für den Kraftwerks- und Anlagenbau sein. Voraussetzung dafür sind ein außergewöhnliches Materiallager, bestens ausgebildete Mitarbeiter und ein hochflexibler Maschinenpark. Letzterer wurde zur Jahreswende um gleich drei CNC-Maschinen ergänzt. Alle von der Hommel Gruppe und dank der aktuellen Verschrottungsprämie 2020 auch noch außergewöhnlich preisgünstig.
Als sich Günter Neises mit der Neiko GmbH & Co. KG am 1. April 1993 selbstständig machte, gab es nicht wenige, die das für einen echten Aprilscherz hielten. Und objektiv gesehen, gab es durchaus einiges an Rahmenbedingungen, die einem erfolgreichen Unterfangen diametral entgegenstanden. Zum einen befand sich die deutsche Industrie 1993 in einem echten Konjunkturtal und zum anderen fehlten Günter Neises einige elementare Voraussetzungen um erfolgreich wirtschaften zu können.
Seine Geschäftsidee – Vertrieb von Sonderteilen für den Kraftwerks- und Anlagenbau – verlangte beispielsweise eine ganze Reihe von Zertifizierungen, Qualitätshandbüchern und Zulassungen, die normalerweise erst nach Monaten und Jahren zugeteilt werden. Hier halfen dem gelernten Maschinenbautechniker sein über lange Jahre als Baustellenleiter erworbenes Know-how und seine anerkannte Kompetenz zwar zu einer schnellen Lösung.
Doch bald musste er eine weitere Schwachstelle in seinen Überlegungen erkennen: Es fehlte an den ,richtigen‘ – sprich qualitätsbewussten und flexiblen – Zulieferbetrieben. Nur logisch, dass er nach gut einem Jahr sein Unternehmen neu ausrichtete und daran ging, eine eigene Fertigung aufzubauen. Heute, nach wenig mehr als 25 Jahren, spricht vieles dafür, dass es genau diese Entscheidung war, die aus dem 70 qm-Büro im Souterrain seines Wohnhauses ein international be- und anerkanntes Unternehmen formte.
Günter Neises zu den Anfängen: „Meine Vorstellung, uns ausschließlich als Vertriebsunternehmen von Sonderbauteilen für Rohrverbindungen zu etablieren, scheiterte vor allem daran, dass es damals an einer geeigneten Zulieferstruktur fehlte. Wir haben uns von Beginn an auf jene Bauteile spezialisiert, die eben nicht fertig in irgendwelchen Regalen liegen, sondern die genau nach den Spezifikationen der Betreiber hergestellt werden.“
„Das betrifft vor allem konkrete Vorgaben in Sachen Werkstoffe. Mit normalem Baustahl ist es da nicht getan. Die Idee, alles selbst zu machen, war also eine schon fast zwangsläufige. Dazu brauchten wir ein breites Vorratslager an unterschiedlichsten Werkstoffen und Durchmessern und einen Maschinenpark, auf dem auch exotische Materialien sicher und genau bearbeitet werden können.“
Stephan Neises, seit 01.01.2016 Geschäftsführer, erklärt: „Wenn aufgrund eines defekten Teiles ein Kraftwerk stillsteht, verliert der Betreiber Hunderttausende Euro pro Tag. Also braucht es einen Partner, der möglichst schnell ein Ersatzteil in der geforderten Qualität liefern kann. Neiko ist dieser Partner. Wir verfügen über ein sehr breitgefächertes Materiallager und können so nahezu alle Bauteile aus den Originalwerkstoffen herstellen und sorgen zudem dafür, dass bei Auslieferung alle nötigen Zulassungen und Bestätigungen vorliegen.“
Und weiter: „Wie mein Vater schon angedeutet hat, sind die meisten Werkstoffe hochtemperaturbeständig und sollen hohen Drücken und aggressiven Medien standhalten. Das ist nicht nur eine Herausforderung für unseren Lagerbestand an sich, sondern stellt auch höchste Anforderungen an unseren Maschinenpark.“ Und weiter Stephan Neises, der im Übrigen sogar einmal der jüngste Maschinenbaumeister Deutschlands war: „Aufgrund der hohen Anforderungen haben wir es meist mit Speziallegierungen zu tun, die nicht nur schwierig zu beschaffen, sondern auch entsprechend schwierig zu bearbeiten sind.“
Das macht Investitionen in Werkzeugmaschinen nicht gerade einfach. Dazu Günter Neises: „Wir haben neben hohen Anforderungen an die Steifigkeit auch zusätzlich kaum Teile, die in nennenswerter Stückzahl laufen. Das heißt, wir können im Normalfall beim Maschinenkauf nicht auf ein bestimmtes Anforderungsprofil zurückgreifen, sondern benötigen Maschinen, die auf ein breites Teilespektrum ausgelegt sind. Natürlich achten wir auch darauf, dass wir die neuesten Bearbeitungstechnologien bei uns im Hause haben und so innovative Bearbeitungsstrategien nutzen können, die uns früher nicht zur Verfügung standen.“
Stabilität und Flexibilität allein reichen aber nicht aus, wie Stephan Neises betont: „Daneben ist für uns der Service eine absolut ausschlaggebende Größe und speziell der gute Service ist beispielsweise ein Kriterium, das sehr für unseren bevorzugten Maschinenlieferanten Hommel spricht. Wir haben ja auch andere Hersteller bei uns im Haus und da ist schon festzustellen, dass manche davon bei einem Schadensfall unter Service vor allem den Austausch ganzer Baugruppen verstehen.“
„Bei Hommel können wir sicher sein, dass die Reparatur im Vordergrund steht. Zudem verbindet uns mit dem Hommel-Geschäftsführer Gisbert Krause ein jahrzehntelanges Miteinander. Er hat uns schon vor seiner Tätigkeit bei Hommel immer fair und kompetent beraten.“
Trotzdem wird bei anstehenden Investitionen in Werkzeugmaschinen grundsätzlich auch immer bei anderen Firmen angefragt und deren Angebote denen von Hommel gegenübergestellt. Dieses Mal waren die Hommel-Angebote aber nicht nur technisch überlegen, sondern konnten dank der Verschrottungsprämie 2020 auch auf der preislichen Seite kräftig punkten.
Gisbert Krause erklärt: „Unsere Grundüberlegung war, dass bei vielen Firmen noch richtig alte Maschinen in dunklen Ecken stehen, die nicht mehr wirklich in die Produktion integriert sind. Wir sind deshalb auf unsere Herstellerpartner zugegangen und haben sie gebeten uns dabei zu unterstützen, diese alten Maschinen durch Neumaschinen zu ersetzen. Unterstützen meint, dass wir von unseren Partnern einen zeitlich begrenzten Preisnachlass bekommen, den wir als Verschrottungsprämie an unseren Kunden weitergeben, ganz ähnlich wie seinerzeit die PKW-Verschrottungsprämie.“
„Für unseren Kunden bringt diese Aktion auf der einen Seite eine merkliche Ersparnis und gleichzeitig eine Modernisierung des Maschinenparks mit sich. Gegenüber unseren Herstellerpartnern müssen wir diese Verschrottung dokumentieren, denn schließlich kostet das sie und uns auch einiges an Geld. Im Gegensatz zu klassischen Rabattaktionen ist das eine Vorgehensweise, die zum einen zeitlich begrenzt ist und zum anderen erst nach der normalen Preisverhandlung greift. Das heißt, erst wenn die Maschine fertig verhandelt ist und ein endgültiger Preis feststeht, kommt die Verschrottungsprämie ins Spiel und bringt dem Kunden einen zusätzlichen Nachlass von bis zu acht Prozent.“
Stephan Neises: „ Wir haben die Sonderaktion zum Anlass genommen, unseren Maschinenpark intensiv zu durchleuchten und sind so zu der Überzeugung gekommen, dass es Sinn macht, gleich drei Werkzeugmaschinen auf einen Schlag zu kaufen. Das sind zwei Dreh-/Fräszentren SC-300II von Nakamura-Tome und ein vertikales Bearbeitungszentrum MV 184 P von Quaser. Wobei eine der beiden Nakamuras mit einem Robotersystem von RoboJob aufgerüstet wurde und die andere eine um 500 mm verlängerte Spitzenweite hat. Ansonsten sind die Maschinen identisch. Die Idee dahinter ist, die robotergestützte Maschine für einfachere Serienteile zu nutzen und die zweite für entsprechend komplexere Werkstücke.“
Wobei die Idee, einen Roboter beizustellen, von Gisbert Krause an das Neiko-Management herangetragen wurde. Dazu Stephan Neises: „Bei Hommel ist es im Gegensatz zu so manch anderem Wettbewerber so, dass im ersten Schritt gemeinsam definiert wird, wie die Maschine sinnvollerweise ausgerüstet sein sollte, um unsere Anforderungen weitestgehend abzudecken und nicht welche Maschine aus dem Katalog am ehesten für uns geeignet ist. Das heißt, mit Hommel erarbeiten wir eine spezifische Ideallösung und bekommen auf dieser Basis eine passende Maschine präsentiert. Andere bieten uns eine Maschine an, und damit hat es sich. Wir lassen uns jedoch gerne beraten, denn so können wir von dem Wissen der Hersteller profitieren.“
Wobei die robotergestützte Lösung letztlich auf einen ganz konkreten Anwendungsfall hin ausgerichtet wurde: „Durch den Rückbau der Kernkraftwerke hat der Bedarf an ultradichten Transportbehälter stark zugenommen. Wir liefern für die Castoren Trägerteile und Deckel, wobei wir für die Herstellung der Deckel eine neue Halle gebaut und in eine Spezialmaschine investiert haben, die Werkstücke bis zu einem Gewicht von 25 Tonnen bei einer Maximallänge von acht Metern und einem Durchmesser von 2,2 m bearbeiten kann.“
Die Trägerkomponenten laufen künftig über die robotergestützte Nakamura-Tome. Da Neiko hier mit ungewöhnlichen Stückzahlen rechnet, macht sich eine automatisierte Lösung schnell bezahlt. Günter Neises: „Bislang werden diese Teile auf zwei Maschinen bearbeitet, künftig kommen diese Werkstücke einbaufertig von der Nakamura-Tome.“
Noch einmal Günter Neises: „Wir haben die Nakamura-Produkte schon länger auf dem Schirm. Man braucht bei Probebearbeitungen nur einmal die Hand auf die Maschinen legen und auf eventuelle Vibrationen achten. Die Nakamuras sind hier eine Klasse für sich. Aber bislang hatten wir keinen wirklichen Bedarf an weiteren Dreh-/Fräszentren. Da hat uns die Hommel-Verschrottungsprämie in Verbindung mit den Castor-Aufträgen einen entscheidenden Schub gegeben.“
Wobei, wie Stepan Neises betont, es noch weitere grundsätzliche Überlegungen gab, zusätzliche Maschinen zu ordern. „Wir halten ganz bewusst immer Maschinenkapazitäten vor und versuchen gar nicht die einzelnen Systeme bis an die Grenze auszulasten, denn für uns ist es wichtiger, immer bei Bedarf auch auf unsere Zentren zugreifen zu können. Wenn der Kunde anruft, er bräuchte innerhalb weniger Stunden einen bestimmten Flansch und wir haben das Material auf Lager, dann können wir das angeforderte Teil herstellen, ohne andere Arbeiten unterbrechen zu müssen.“
„Wir haben einige Maschinen, die für diese Schnellschüsse reserviert sind. Wir garantieren unserem Kunden, dass er seine Teile in dem kürzest möglichen Zeitraum bekommt und wir sind stolz darauf, dass unser Name in der Branche inzwischen für uneingeschränkte Lieferzeit und hohe Qualität steht.“ Und: „Das führt so manches Mal zu eigentlich kuriosen Abläufen, wenn beispielsweise trotz einem vorhandenen Mini-Auftragspolster von wenig mehr als einer Woche auch an Sams- und Sonntagen gearbeitet werden muss.“
Zum Schluss noch kurz zu den Maschinen: Die Nakamura-Tome SC-300 II ist standardmäßig mit Fräsantrieb und Y-Achse ausgestattet und ausgelegt für einen Drehdurchmesser bis 360 mm und einer Drehlänge von 600 mm (respektive 1.100 mm). Sie bietet bei einer Spindelleistung von 22 kW ein Drehmoment von 500 Nm. Ausgerüstet mit einer Fanuc 0i CNC können auf dem Revolver bis zu 12 rotierende Werkzeuge genutzt werden. Was die schon angesprochene Stabilität angeht, so lässt sich das mit Flachführungen in allen Achsen und ein Maschinengewicht von über neun Tonnen belegen. Zudem sind die Maschinen für Materialien bis zu einem Härtegrad von HRC 62 prädestiniert.
Das vertikale Hochleistungs-Bearbeitungszentrum Quaser MV 184 P besticht vor allem durch die hochdynamischen volldigitalen Achsantriebe mit bis zu 40 m/min Eilgang. Das bei Neiko mit einer Siemens 828 D ausgerüstete Zentrum (alternativ stünden auch eine Heidenhain TNC 640 oder eine Fanuc 31i zur Auswahl) bietet Verfahrwege von 1.020x610x610 mm (X,Y,Z) und deckt einen Drehzahlbereich bis 12.000 min-1 (optional bis 15.000 min-1) ab. Mit 30 Werkzeugen stehen zudem für die bei Neiko anstehenden Aufgaben ausreichend Werkzeuge zur Verfügung. Auch hier lohnt sich ein Blick auf das Maschinengewicht. Mit fast 7.400 kg bei Außenmaßen von gerade einmal 291x330x286 cm steht die Quaser MV 184 P für einen grundsoliden und stabilen Maschinenbau.
Kontakt: