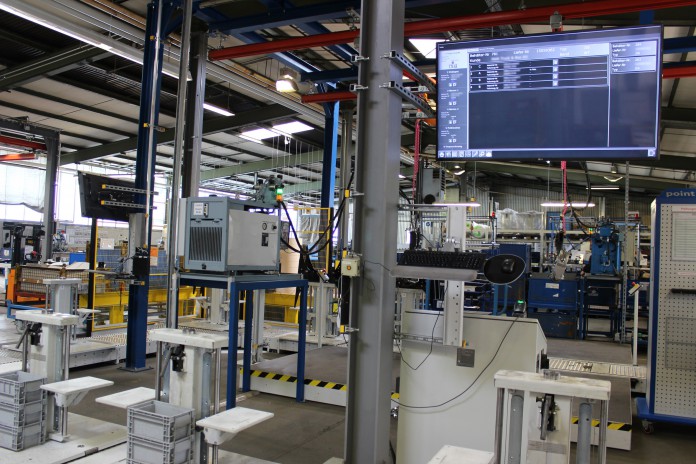
Die Hörmann Automotive Penzberg GmbH (HAP) ist ein gefragter Partner der Fahrzeugindustrie. Insbesondere Hersteller von Nutzfahrzeugen und Landmaschinen nutzen die Kompetenz und jahrzehntelange Erfahrung des oberbayrischen Dienstleisters, der aus dem MAN Omnibuswerk Penzberg hervorgegangen und heute auf die Bearbeitung von Blechen und Rohren spezialisiert ist.
Knapp 700 Mitarbeiter verarbeiten täglich im Drei-Schicht-Betrieb etwa 90 Tonnen Blech inverschiedenen Stärken und Formaten sowie 10.000 Meter Rohrmaterial. Auf modernsten Laser- und Roboterschweißanlagen sowie Rohrbiegemaschinen entstehen daraus Tag für Tag rund 40.000 Komponenten und Systeme. In erster Linie sind das einbaufertige Rahmenanbauteile, die vom Rohmaterial bis zur Beschichtung und Montage komplett in Penzberg gefertigt werden. Die Kompetenz geht aber noch darüber hinaus, wie Alexander Herz, Abteilungsleiter Logistik, erklärt: „Wir liefern unseren Kunden die gewünschten Produkte just-in-time oder just-in-sequence – mit höchster Zuverlässigkeit und Flexibilität.“
Um auch in der Montage von LKW-Querträgern auf modernstem Stand agieren zu können, investierte Hörmann Automotive Penzberg in ein Montage- und Transportsystem der Firma KNOLL Maschinenbau, Bad Saulgau, das den Umstieg von Boxen- auf Linienfertigung ermöglichte. Laut Alexander Herz erforderte das frühere Vorgehen „zu viele Einzelschritte mit hohem Handling-Aufwand. Außerdem war die Boxenfertigung zu platzintensiv, da nach der Fertigung und Montage noch eine nachgelagerte Sequenzierung der Teile erforderlich war.“
Der Hintergrund: Die HAP liefert ihrem Kunden LKW-Querträger in drei grundsätzlich unterschiedlichen Varianten: gegossen, geschweißt und genietet – in verschiedenen, vom Fahrzeug abhängigen Versionen. Die Lieferung erfolgt „just-in-sequence“. Das heißt, die Querträger müssen exakt in der geforderten Reihenfolge in spezielle Transportcontainer gepackt werden, so dass sie der Kunde ohne weitere Sortierung in seine Produktion übernehmen kann.
Die zu nietenden Querträger laufen größtenteils über das neue Montageband, wo sie bis zum Auslieferungszustand bearbeitet werden. Die gegossenen und geschweißten Varianten, die keine weitere Bearbeitung und Montage benötigen, werden am Bandende beigestellt. „Die mit der Montageanlage von KNOLL gelieferte Prozessleittechnik übernimmt die Sequenzierung aller Querträger. Auf einem großen Monitor wird die geforderte Reihenfolge angezeigt, so dass ein Mitarbeiter die Transportboxen entsprechend befüllen kann. Dadurch hat sich der Sequenzierungsaufwand deutlich verringert“, freut sich Logistikleiter Herz.
Modulares Montage- und Transportsystem
Das von HAP eingesetzte Transportsystem wurde von KNOLL ursprünglich für den Eigenbedarf zur Montage von Filteranlagen entwickelt. Seit einigen Jahren vertreibt das Maschinenbauunternehmen das System als eigenständiges Produkt. Je nach Anforderung stehen drei verschiedene Förderbänder zur Verfügung: das Staurollen-Förderband TS-S, das auf einer geradlaschigen Kette aufbauende TS-G-Band und die Zugkette TS Z. KNOLL bietet dazu eine umfangreiche Ausstattung an, von Wagensystemen, einstellbaren Stoppern über Drehstationen, Indexiereinheiten, höhenverstell- und drehbaren Scherenhubtischen bis zu individuellen Umhausungen. Durch den durchgängig modularen Aufbau, der neben den mechanischen auch elektronische Elemente und Bussysteme einschließt, lässt sich das Transportsystem in jeder Größe und Ausprägung konfigurieren.
Überzeugend in Preis und Leistung
Erste Bekanntschaft mit dem KNOLL Montage- und Transportsystem machten die HAP-Verantwortlichen auf der Fachmesse Motek 2012. Aus einem anschließenden Benchmark mit den Systemen anderer Anbieter ging das KNOLL TS als Sieger hervor. „Entscheidend waren die Modularität und Ausbaufähigkeit des Systems“, erläutert Alexander Herz. „Auch das Angebot, System und Prozessleittechnik von KNOLL aus einer Hand geliefert zu bekommen, war für uns von großer Bedeutung. Zudem stimmte das Preis/Leistungsverhältnis.“
So erhielt KNOLL Ende 2013 den Auftrag, das Montagesystem für die zu nietenden LKW-Querträger zu projektieren. Andreas Fuchs, Schichtmeister Montage und Lack, schildert die Zusammenarbeit als ausgesprochen konstruktiv und fachlich kompetent: „Ergänzend zu unseren Vorstellungen brachte KNOLL Ideen ein, die sich für uns als klarer Mehrwert herausstellten. Beispielsweise die Arbeitsplatzgestaltung mit Holzpodesten, die einen Höhenausgleich zum Band herstellen. Diese Zusatzeinrichtung steigert die Ergonomie und kommt bei unseren Mitarbeitern hervorragend an.“
Seit Herbst 2014 ist das Transportsystem in Penzberg installiert. Es besteht aus einer platzsparenden, rechteckigen Anordnung von Transportbändern und verschiedenen Arbeitsstationen. Für die geraden Strecken kommt das Transportsystem mit Staurolle (TS-S) zum Einsatz; die vier Drehstationen an den Ecken sind mit einer geradlaschigen Kette (TS-G) ausgeführt. Die Bänder haben eine Spurbreite von 800 mm und sind 230 mm hoch.
RFID-Kennzeichnung gewährleistet prozesssicheren Durchlauf
Die Werkstückträger bestehen aus Transportplatten, die in der Regel auf dem Bandsystemverbleiben. Sie sind mit einem RFID-Tag versehen, das in der ersten Station mit der Auftragsnummer beschrieben wird. Sie kennzeichnet das zu ladende Bauteil und die auszuführenden Tätigkeiten. An jeder der folgenden Arbeitsstationen wird das RFID-Tag ausgelesen und der jeweilige Auftrag bzw. die erforderlichen Arbeiten über das installierte Prozessleitsystem aufgerufen.
Die zweite Station ist der sogenannte „Supermarkt“. Hier wird der auf dem Werkstückträger befindliche Montagebock mit allen benötigten Teilen bestückt. Anschließend fährt der Wagen weiter zu zwei nacheinander angeordneten Bearbeitungsstationen, auf denen der Querträger mittels großer Nietzangen einmal von rechts und einmal von links vernietet wird.
Als nächstes folgt die Qualitätssicherung. An dieser Station findet eine optische 100 %-Prüfung statt, die derzeit noch von einem Mitarbeiter ausgeführt wird. Anfang 2016 wird eine roboterunterstützte Messstation installiert, die mit einem Kamerasystem ausgestattet ist. Danny Zinßler, Mitglied des Projektierungsteams von KNOLL, ergänzt: „Wir werden dann das Transportband mit der bereits bestellten Hebe-Indexiereinheit ergänzen, die den Werkstückträger abhebt und über Indexier-Dorne in eine definierte, wiederholbare Position bringt. Während jetzt noch der Mitarbeiter den IO-Zustand mit einer Zustimmtaste quittieren muss, erfolgt dann die Freigabe automatisch, da die Messzelle mit der Steuerung kommuniziert.“
Sollte ein Fehler festgestellt werden, fährt der Werkstückträger zurück auf einen Nacharbeitsplatz. Währenddessen stoppt die Sequenz, um eine falsche Reihenfolge zu vermeiden. Erst wenn der Querträger ordnungsgemäß montiert ist, fährt er weiter zum Entnahmeplatz, wo ihn der Mitarbeiter entsprechend der geforderten Sequenz in den Transportbehälter packt. Dort wird auch der RFID-Tag auf null zurückgesetzt, so dass der Werkstückträger für einen erneuten Umlauf zur Verfügung steht.
Prozessleitsystem unterstützt Bediener und Abläufe
Das KNOLL Montage- und Transportsystem wird über eine SPS gesteuert. Zusätzlich bietet KNOLL ein Prozessleitsystem an, das auf einem separaten Server installiert ist. Es eröffnet dem Anwender zahlreiche Möglichkeiten, wie zum Beispiel die Ankopplung an ein ERP-System oder zusätzliche visuelle Bedienerunterstützung. Danny Zinßler erklärt: „Das Prozessleitsystem besitzt unter anderem eine neutrale Schnittstelle, über die beliebige ERP-Systeme angekoppelt werden können.“ Alexander Herz hat dieses Angebot gerne angenommen: „Ein eigenes Prozessleitsystem als Bestandteil des Gesamtkonzeptes haben nicht viele Hersteller von Transportsystemen im Portfolio. Die Tatsache, dass das Prozessleitsystem direkt von KNOLL kommt hat die Abstimmung bei der Inbetriebnahme erheblich vereinfacht.“ HAP nutzt die Anbindung ihres ERP-Systems zum Beispiel zur Steuerung der Sequenzen. Es stellt die entsprechenden Informationen dem Prozessleitrechner zur Verfügung, der sie weiterverarbeitet und an die Montageanlage ausgibt.
Zwingend erforderlich für die sequenzgenaue Steuerung ist das RFID-Identifikationssystem, das KNOLL als Standardbaustein anbietet. Es ermöglicht auch, den Mitarbeiter mit zusätzlichen Informationen zu unterstützen. So ist an jedem Arbeitsplatz ein Monitor installiert, auf dem nach dem Identifizieren des Werkstückträgers automatisch der dazugehörende Fertigungsauftrag erscheint und individuell definierte, grafisch aufbereitete Informationen abrufbar sind. Schichtmeister Andreas Fuchs erklärt: „Wir stellen dem Mitarbeiter neben Text auch Fotos, Zeichnungen und 3D-Modelle zur Verfügung, denen er die benötigten Informationen auf einfache Weise entnehmen kann. Durch die RFID-Identifikation und das Prozessleitsystem haben wir zudem die Absicherung, dass der Bediener nicht aus Versehen einen falschen Auftrag erwischt.“
Platz und Zeit gespart
Die Hauptersparnis, die durch die neue Anlage eingetreten ist, betrifft jedoch Platz und Zeit. Alexander Herz fasst zusammen: „Wir haben es geschafft, den Flächenbedarf für die gesamte Produktfamilie auf ein Viertel zu reduzieren. Zudem konnten wir unsere Lagerbestände um fast 50 Prozent senken. Das war ein Riesenerfolg, da wir die frei gewordenen Flächen für andere Fertigungsumfänge nutzen können. Auch der Zeit- und Reaktionsfaktor ist beachtlich. Das gleiche Produktionsprogramm stemmen wir heute in eineinhalb Schichten, wofür wir früher drei Schichten benötigt haben.“
Nun macht sich Logistik-Fachmann Herz daran, die Kapazität des Montage- und Transportsystems komplett auszunutzen und die freigewordenen eineinhalb Schichten zu füllen: „Unser Ziel ist es, noch eine weitere Montagekomponente in mehreren Schritten auf dem Band fertigen zu können“, erklärt Alexander Herz. „Die erforderlichen Umbaumaßnahmen sind überschaubar“, ergänzt Danny Zinßler. „Schließlich ist das KNOLL Transportsystem TS modular aufgebaut und jederzeit und ohne großen Aufwand erweiterbar.“
Die wesentlichen Fakten zum KNOLL Transportsystem
• Lastbereich 150 – 5000 kg/m
• Fahrbare Montage- und Kommissionierwagen möglich
• Hohe Biegesteifigkeit durch robuste Stahlkonstruktion
• Flexibles Baukastensystem, beliebig erweiterbar
• Positionieren und Vereinzeln der Wagen auf dem gemeinsamen Förderband
• Ebenerdig oder mit Aufständerung aufstellbar
• Manuelles Aufbringen und Entnehmen der Wagen völlig ohne Hilfsmittel
• Trägersystem mit z.B. seitlich nach unten überstehenden Rollen möglich
• Keine baulichen Vorbereitungen für Installation erforderlich
• Montagearbeitsplätze höhenverstell- und drehbar für optimale Montagevoraussetzungen
Kontakt: