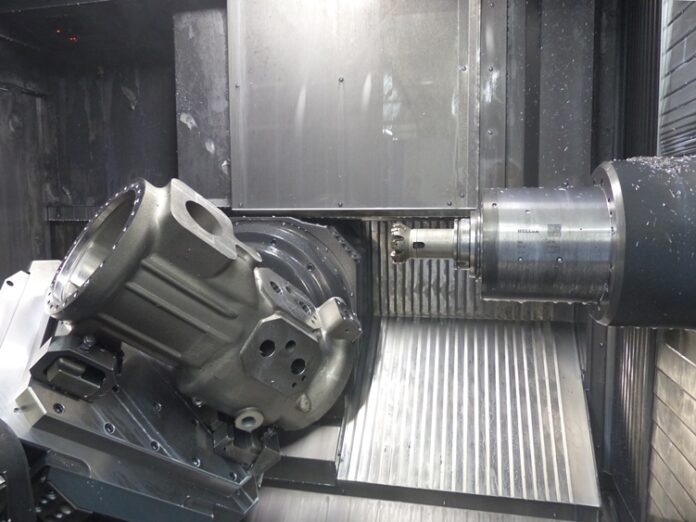
1982 investierte das Unternehmen Bock in Frickenhausen in das erste Bearbeitungszentrum von HELLER. Qualität, Zuverlässigkeit sowie der Service haben überzeugt. Deshalb setzt man seither kontinuierlich auf die Maschinen. Besonders umfangreich investierte man zwischen 2009 und 2011. So wurde u.a. auch der Fertigungsstandort in Tschechien mit vier Bearbeitungszentren von HELLER ausgestattet.
Nun zählt das Unternehmen BOCK mit zu den weltweiten Technologie- und Innovationsführern bei der Entwicklung umweltschonender, ökonomischer Lösungen im Bereich Kälte- und Klimatechnik. Durch zahlreiche Neuentwicklungen stellte man deshalb 2020 für die Fertigung der neuen Verdichter-Gehäuse die 4-Achs-Bearbeitung in Frage.
Für Produktionsleiter Steffen Schmid war zu dem Zeitpunkt schnell klar, dass sich mit der 5-Achs-Bearbeitung das neue Produktportfolio wesentlich wirtschaftlicher darstellen lässt: „Der große Vorteil bei fünf Achsen ist die Komplettbearbeitung in einer Aufspannung. Denn wenn man nochmal umspannen muss, läuft man Gefahr, dass sich das Werkstück verzieht oder sich auch Spannungen im Guss lösen. Und man ist mit nur einer Aufspannung natürlich wesentlich schneller.“
Damit war die Entscheidung für die 5-Achs-Bearbeitung eigentlich schon gefallen. Obwohl man nun mit den Bearbeitungszentren von HELLER bisher äußerst zufrieden war und ist, heißt das aber nicht, dass beim Unternehmen Bock nicht vor jeder Neuinvestition intensive Benchmarks durchgeführt werden. Im konkreten Fall der 5-Achs-Bearbeitung war der stufenweise Aufbau einer Fertigungsanlage mit einem ersten Bearbeitungszentrum, einem Automationssystem und evtl. einem zweiten Bearbeitungszentrum geplant.
Um es kurz zu machen: das modulare Gesamtkonzept von HELLER hat überzeugt. Auf Grund der hohen Anforderungen stand man intensiv im Austausch und HELLER hat die Gehäuse in Nürtingen in zahlreichen Tests gefertigt. So wurde dann 2021 das erste 5-Achs-Bearbeitungszentrum HF 5500 der 2. Generation nach Frickenhausen geliefert. Eingesetzt wird das Bearbeitungszentrum (bislang) allerdings noch nicht zum Simultanfräsen. Vielmehr geht es den Verantwortlichen in Frickenhausen um das 2+3 Achs-Fräsen, für schräge Flächen und Bohrungen. Und eben die Komplettbearbeitung.
Enorme Zeiteinsparungen generiert, Qualität deutlich erhöht
Die hohen Anforderungen waren für René Greising, Geschäftsführer der HELLER Gebietsvertretung Hans P. Greising GmbH aber das geringere Problem: „Die HF 5500 war zunächst ja als Stand-alone-Maschine im Gespräch, ein Jahr später sollte das Fastems Automationssystem angeschlossen werden.“
„Einerseits bewegt man sich bei der Genauigkeit in der H6-Welt. Wegen der unterschiedlichen Aufmaße in der Guss-Bearbeitung war andererseits aber auch ein hohes Drehmoment gefordert. All das stellt HELLER sicher nicht vor große Herausforderungen. Es war mehr die Tatsache, dass die Bearbeitungszentren HF der zweiten Generation noch nicht im Markt eingeführt waren und wir für die Fa. Bock eine effiziente Bearbeitungslösung wollten.“
HELLER hat damit aber das Ziel eines universelleren Einsatzes auch in der Einzelteilfertigung erreicht. Und konnte die neue Generation auch mit den bekannten Genen wie Produktivität, Genauigkeit und Zuverlässigkeit verbinden. Die HF 5500 bei Bock ist mit der HELLER eigenen DC-Spindel mit HSK-A 100, 12.000 min-1 und 400 Nm ausgerüstet. Die Toleranzen, selbst beim Honen der Zylinderbohrungen, hält man problemlos.
Nach dem Einfahren aller Gehäusetypen wurde die Anlage mit dem Automationssystem von Fastems mit 10 Plätzen ergänzt. Die Verdichter-Gehäuse aus fünf Baureihen in Losgrößen zwischen drei und fünf Stück aus Sphäro- und Grauguss werden aktuell im Dreischichtbetrieb (nachts mannlos) gefertigt. Und dies ohne Probleme, selbst wenn man sich häufig an der Obergrenze des Drehmoments bewegt.
Neben der höheren Qualität überzeugen in Frickenhausen aber vor allem die zusätzlichen Kapazitäten, die man mit der Anlage generiert hat. Neben den Hauptzeiten sind das vor allem die Einsparungen beim Rüsten. Dazu Steffen Schmid: „Wir hatten vorher für jeden Gehäusetyp eine separate Aufspannvorrichtung. Einmal abgesehen davon, dass dieses Rüsten sehr viel Zeit in Anspruch nahm, haben wir jetzt durch die Komplettbearbeitung nur noch eine universelle Vorrichtung, mit der wir alle Typen spannen können.“
Diese zusätzlichen Kapazitäten sieht der Sprecher der Geschäftsführung Dr. Marcus Albrecht allerdings auch als zwingend erforderlich: „Auf dieser Anlage werden alle unsere Produkte der Zukunft gefertigt. Wir sind aktuell mitten in der Hochlaufphase, aber bei der aktuellen Nachfrage nach den CO2-Kompressoren sehen wir schon, dass diese Investition notwendig war, um die ambitionierten Wachstumsziele von Bock in zu realisieren. Unabhängig davon führen wir neue Technologien zunächst hier in Frickenhausen ein. Und erst wenn wir funktionierende, stabile Prozesse haben, setzen wir das in unseren weltweiten Fertigungsstandorten um.“
Unter diesen Gesichtspunkten denkt Dr. Albrecht auch schon jetzt in Frickenhausen über die Endausbaustufe der Anlage mit einem weiteren HELLER Bearbeitungszentrum nach.
Kontakt: