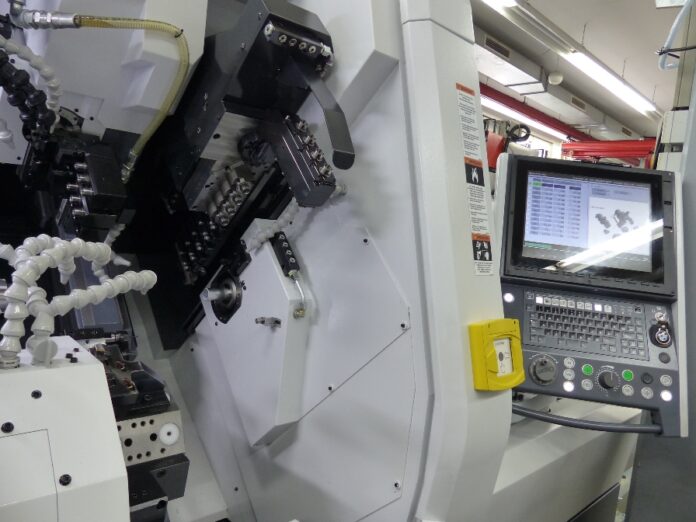
Es sind überwiegend Kleinserien aus anspruchsvollen Materialen wie Inconel, hochlegierten Stählen oder hochfestes Luftfahrt-Aluminium, auf die man sich beim Unternehmen Robert Höhne im bayrischen Wagenhofen konzentriert. Für dieses Teilespektrum wurde im letzten Jahr 2021 in einen Langdrehautomaten mit Revolver von Citizen investiert. Ein Maschinenkonzept, das für das Produktportfolio nahezu maßgeschneidert ist.
Langdrehautomaten eignen sich zwar vor allem bei entsprechend hohen Stückzahlen. Bei Höhne nutzt man die Technologie aber, weil zahlreiche Bauteile auf einem Kurzdreher nur schwierig zu fertigen sind. Nun verfügt die Maschine von Citizen über die LFV-Technologie (oszillierende Bewegungen für Spanbruch). Das war für die Zerspanungsspezialisten in Wagenhofen ideal, denn als klassischer Einschicht-Betrieb setzt man zusätzlich auf zwei mannlosen Schichten.
Allein mit dem Spanbruch war es allerdings nicht getan, denn man setzt auch Werkzeuge mit Durchmessern zwischen ein und drei Millimeter ein. Nun sind Langdrehautomaten für gewöhnlich mit taktilen Messsystemen ausgerüstet. Bei diesen Werkzeugdurchmessern besteht allerdings die Gefahr, dass es beim Abtasten zu Haarrissen kommt. Ein weiteres Problem ist die Tatsache, dass bei den zahlreichen Achsen an der Maschine, für jede Achse ein System notwendig wäre. Abgesehen davon, dass man keinen Platz für diese Messsysteme hat, wäre eine mechanische Überprüfung auch ein nicht vertretbarer Zeitaufwand.
Und so war Geschäftsführer Robert Höhne auf der Suche nach einer entsprechenden Werkzeugüberwachung und wurde beim Unternehmen UTTec 2022 in Winnenden fündig: „Unser Ziel war es, die Maschine auch unter schwierigen Bedingungen mannlos und prozesssicher zu fahren. Zudem wollte ich meine Mitarbeiter an der Maschine mit der Information unterstützen, wann ein Werkzeug zu wechseln ist. Eine Grundvoraussetzung für die Überwachung war allerdings, dass ich die Daten für unser eigenes M-/BDE-System Toolflakes nutzen kann, denn hier sind Taktzeiten, Werkzeugstandzeiten, Standzeit-Monitoring etc. hinterlegt.“
Die ersten Versuche hat UTTec dann auf einer baugleichen Maschine (ein Motor treibt bis zu 12 Spindeln mit Werkzeugen an) gestartet und selbst bei sehr geringen Lasten waren diese Versuche erfolgreich.
Die „ideale Notbremse“ bringt bares Geld
Die Nutzung der notwendigen Daten für das M-/BDE-System war kein Problem. Das Überwachungssystem UT-Tm-Basic hatte die Schnittstelle bereits integriert und UTTec stellt die Daten über eine JSON-Datei zur Verfügung. So lassen sich einfach und problemlos aktuelle Schnittdaten einpflegen, um exakte Aussagen über Kräfte zu definieren.
Das bzw. die Probleme lagen für UTTec vielmehr in anderen Bereichen. Das waren zunächst die kleinen Werkzeuge und damit verbunden die geringen Lasten. Einen Bohrer von 1,00 mm über einen Mehspindelbohreinheit zu erfassen war bis dahin kaum möglich. Ein weiteres Problem waren die Platzverhältnisse an der Maschine.
Alles Probleme, die Uwe Schröter, Geschäftsführer UTTec aber als interessante Herausfor-derung sah: „Wir hatten unsere Entwicklungen in der Kleinstzerspanung schon vor diesem konkreten Einsatz forciert. Darauf aufbauend haben wir ein neues Modul entwickelt, damit wir keinen externen Sensor einsetzen müssen. Wir messen jetzt in der Basis die Wirkleistung, tasten die Motorströme hochfrequent mit einem separaten Signalverarbeitungsprozessor ab, bereiten sie auf und führen das Ergebnis direkt in eine neue Messkarte.“
„Die Abtastung ist im Regelfall wesentlich genauer, als feldbusbasierte Drehmomentmessungen. Sie ist schneller, ermöglicht feinfühliger zu messen und wir können über unser Modul die Daten abgreifen. Durchmesser von 1,00 mm, evtl. auch darunter, kann UTTm oft erfassen. Das heißt, wir haben damit eine steuerungsneutrale Lösung für Langdrehautomaten geschaffen, die es meines Wissens nach bislang so einfach nicht gab.“
Nun steht Industrie 4.0 dafür, möglichst viele Daten aus der Fertigung zu sammeln und vollautomatisch auszuwerten. Mit einer taktilen Messung ist das nicht möglich. Unabhängig davon, benötigt man für solch einen Messvorgang zwischen 3 und fünf Sekunden. Im Zu-sammenhang mit Industrie 4.0 sprechen für Robert Höhne allerdings noch weitere Aspekte, für offene Systeme:
„Selbst ein qualifizierter Mann an der Maschine hört es nicht unbedingt, wenn solch ein Bohrer bricht. Das ist solch ein System die ideale Notbremse. Andererseits kann man über die Schnittkraft Grenzen setzen und klar definieren, wann eine Warnung erfolgt. Entscheidend ist aber doch, dass man damit ein Hilfsmittel hat, um mit der optimalen Strategie zu noch höherer Prozesssicherheit und Wirtschaftlichkeit zu gelangen.“
Apropos Wirtschaftlichkeit. Die Taktzeiten sind auf Grund der geringen Losgrößen in Wagenhofen nicht ganz so wichtig. Aber wenn man wie beim Unternehmen Robert Höhne durch die Überwachung die Spindellaufzeiten um 30 bis 50 % in den mannlosen Schichten erhöhen kann, ist das auch bares Geld.
Kontakt: