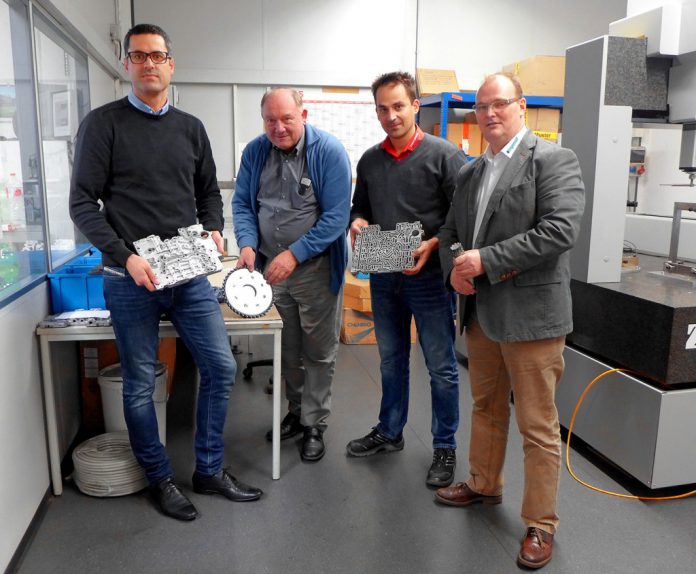
Die Firma Theilinger in Nürnberg gliedert sich in zwei Firmenbereiche – der Theilinger Automation und Papiertechnik GmbH und der Theilinger PRO GmbH. Die Theilinger Automation und Papiertechnik GmbH ist mit den Geschäftsbereichen Automation, Robotics und Paper ein mittelständisches Unternehmen, das seit 1995 mit seinen dynamischen Entwicklungen und hochqualifizierten Mitarbeitern mechanische Komplettlösungen von der Konstruktion bis zur Inbetriebnahme anbietet. Die Kernkompetenz liegt in der Automatisierung von Fertigungsprozessen der Automobil-Zulieferindustrie.
Dass das Knowhow und die Innovationskraft noch über die Planung und Lieferung von Automatisierungskomponenten hinausgehen, wird am Beispiel der Entwicklung einer Doppelspindel-Fräsmaschine, sowohl für die eigene Produktion als auch für einen Kunden, dargestellt. Der Firmenbereich Theilinger Pro GmbH ist ein höchstflexibler Zerspanungsdienstleister, der sich in der Bearbeitung von Großserien (Aluminium- Druckgussteile) für die Automobil-Zulieferindustrie einen Namen gemacht hat.
Auf den ersten Blick sind Theilinger Automation und Papiertechnik GmbH und Theilinger Pro GmbH zwei sehr unterschiedliche Geschäftsbereiche, die sich aber in der Praxis sehr sinnvoll ergänzen. Einerseits fließen die Zerspanungserfahrungen des Firmenbereiches Theilinger Pro GmbH in die Auslegung von Maschinen und Anlagen der Theilinger Automation und Papiertechnik GmbH ein und können sogar Anregung für Produktideen sein. Andererseits hilft die Innovationskraft der Entwickler und Fachleute von Theilinger Automation und Papiertechnik GmbH den Fertigungsspezialisten bei Theilinger Pro GmbH für jede gestellte Aufgabe das richtige Maschinenkonzept zu finden. So partizipieren auch zwei so unterschiedliche Firmenbereiche jeweils von der Erfahrung der Schwesterfirma.
Zwischen der INGERSOLL Werkzeuge GmbH und der Firma Theilinger bestehen langjährige vertrauensvolle Verbindungen, die seit dem Jahre 2012 auch auf die Bearbeitung von ALU-Bauteilen für den Betriebsbereich Theilinger Pro GmbH ausgeweitet wurden. Als die Firma Theilinger Pro GmbH eine Projektanfrage zur Bearbeitung von Steuerteilen für ein Automatikgetriebe erhielt, war der Wunsch der Fertigungsverantwortlichen bei Theilinger Pro GmbH, dieses Projekt mit INGERSOLL zu realisieren.
Die Anfrage beinhaltete die Bearbeitung von Ventilgehäusen und Ventilplatten; und zwar das Vorfräsen um < 1mm, um den Verzug der Bauteile zu reduzieren, bevor dann der Kunde, ein renommierter Automobilzulieferer, die Finish-Bearbeitung im eigenen Hause ausführt. Die geplante Jahresproduktion lag zu Beginn des Projektes bei ca 1.7 Mio Teile pro Jahr. Bei der Planung war schon klar, dass diese hohen Stückzahlen nur mit Sonderwerkzeugen zu bewältigen sind. Da der Beginn der Bearbeitung mit geringeren Stückzahlen allerdings schon drei Wochen später beginnen sollte, musste der Start mit lagermäßig vorhandenen Standardwerkzeugen erfolgen.
Bearbeitungsstart mit Standardwerkzeugen
Für das Konturfräsen der Anschlussseite der Ventilplatten wurde ein axial einstellbares Werkzeug der HiPos+ Serie (2J5P) mit 40 mm Durchmesser und Zeff 6 gewählt.
Mit 0,8 mm Schnitttiefe, 20-39 mm Schnittbreite, 1885 m/min Schnittgeschwindigkeit und einem Zahnvorschub von 0,14 mm konnte die Konturbearbeitung zur vollsten Zufriedenheit des Kunden durchgeführt werden. Für die Bearbeitung der Labyrinthseite fiel die Wahl auf einen einstellbaren V-Max Fräser (VK2V) mit einem Durchmesser von 125 mm und Zeff 10.
Bei dieser Bearbeitung betrug die Schnitttiefe ebenfalls 0,8 mm, die Schnittbreite 110 mm, die Schnittgeschwindigkeit 2945 m/min und der Zahnvorschub 0,16 mm. Auch die Bearbeitung der Labyrinthseite konnte mit dem gewählten Werkzeug ohne Probleme erledigt werden. Der Start der Produktion wurde, bis zur Fertigstellung der Sonderwerkzeuge, auf einer vorhandenen SW BAS03 Doppelspindel-Fräsmaschine mit HSK 63 und MMS-Zuführung organisiert.
Durch steigende Bedarfszahlen war die Ausbringung mit den Standardwerkzeugen schnell zu gering. Die bei INGERSOLL in Fertigung befindlichen Sonderwerkzeuge wurden also dringend erwartet. Um das Handling für die Sonderwerkzeuge möglichst niedrig zu halten, hatte man sich bei der Firma Theilinger für die Variante in gelöteter Ausführung entschieden. Alternativ hätte eine Ausführung mit einstellbaren PKD-Schneiden gewählt werden können, jedoch wäre dann die Einstellung vor Ort zeitaufwändiger gewesen.
Steigerung der Produktion mit Sonderwerkzeugen
Nach Fertigstellung der Sonderwerkzeuge konnten die ersten Einsätze stattfinden.Für die Bearbeitung der Konturen an der Anschlussseite der Ventilplatten wurde ein gelötetes Werkzeug mit Durchmesser 40 mm und 9 Schneiden zum Einsatz gebracht. Durch die Erhöhung der Schneidenzahl und einer größeren Schnittbreite, konnte die Bearbeitungszeit gegenüber dem Katalogwerkzeug etwa um 30 % reduziert werden. Die erreichte Standmenge betrug ca. 50.000 Bauteile.
Die Bearbeitung der Labyrinthseite mit den eigens gefertigten, gelöteten Planfräsern mit 125 mm Durchmesser und 19 effektiven Schneiden brachte ebenfalls eine enorme Zeitersparnis von über 40 % und auch hier lag die erreichte Standmenge bei 50.000 Ventilgehäusen.
Mit Highspeed-Werkzeugen zur Massenproduktion
Die vor Projektbeginn geplante Produktionsmenge von etwa 1,7 Mio. Bauteilen hatte sich sehr bald als zu niedrig erwiesen. Die Firma Theilinger wurde von ihrem Kunden gebeten, eine Jahresproduktion von etwa 5 Mio. kompletten Steuerteilen zu planen. Aufgrund der bisher gemachten Erfahrungen in Bezug auf die Bearbeitungszeit hatte man verlässliche Daten, um die Maschinenkonfiguration für diese Stückzahlen auszulegen.
Bei der Firma Theilinger wurde beschlossen, eine Sondermaschine als Doppelspindel-Fräsmaschine zu entwickeln, mit einem Werkzeugdurchmesser von 250 mm, um die sogenannte Labyrinthseite in nur einem Schnitt zu bearbeiten. Weiterhin war durch diesen Schritt die vorhandene SW BAS03 Doppelspindel-Fräsmaschine komplett für die Bearbeitung der Kontur an der Ventilplatte frei.
Zwischen Herrn Meyer-Theilinger (Geschäftsführer) und Herrn Johannes Post (Produktmanager PKD-Werkzeuge Firma INGERSOLL Werkzeuge GmbH) wurde das Werkzeug für die Doppelspindel-Fräsmaschine mit folgenden Eckdaten konzipiert:
- PKD gelötet mit Zeff = 41, um das Handling so einfach wie möglich zu halten.
- Aufsteckadaption, um vertikal montieren zu können.
- Besondere Einbringung der MMS und Verteilung innerhalb des Werkzeuges.
- Konstruktive Lösung entwickeln, um MMS von der Spindeldurchführung direkt an jede Schneide zu bringen (gemeinsam mit dem Spindelhersteller).
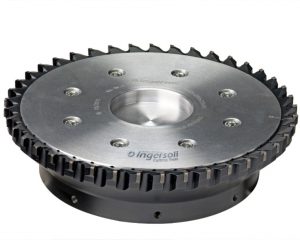
Die von der Firma Theilinger konzipierte Doppelspindel-Fräsmaschine und die speziell für diese Bearbeitung geplanten und produzierten Planfräser mit eingelöteten PKD-Schneiden von der INGERSOLL Werkzeuge GmbH konnten schon bald zum ersten Mal eingesetzt werden. Die Anwendungserfahrungen, die man gemeinsam mit den Standard- und auch mit den ersten Sonderwerkzeugen gesammelt hatte, zahlten sich nun aus. Denn sowohl die Doppelspindel-Fräsmaschine mit einzeln korrigierbaren Z-Achsen, als auch die Planfräser, mit der speziell entwickelten MMS-Zuführung, funktionierten von Beginn an tadellos.
Auch die Kapazitätsplanung der Fräsmaschinen für die erhöhte Produktionsmenge von mittlerweile etwa 5 Mio. Steuerteilen pro Jahr hat sich als vollkommen richtig erwiesen. Derzeit läuft dieses Projekt auf zwei Linien, bei denen je eine Doppelspindel-Fräsmaschine von Theilinger die Bearbeitung der Labyrinthseite in einem Schnitt ausführt, sowie eine Doppelspindel-Fräsmaschine von Heckler & Koch und eine Doppelspindel-Fräsmaschine von SW, die die Kontur an der Anschlussseite der Ventilplatte bearbeiten.
Kundenprojekt: Einspindel-Fräsmaschine für Wärmetauscher
Durch die Konstellation der Firmenbereiche Theilinger Pro GmbH und Theilinger Automation und Papiertechnik GmbH ergibt sich bei der Firma Theilinger die Möglichkeit, in der Produktion eingesetzte und bewährte Vorrichtungen und Maschinen als eigene Produkte über den Firmenbereich Theilinger-Automation und Papiertechnik zu vermarkten.
Der erste Interessent und Kunde für die neu entwickelte Doppelspindel-Fräsmaschine war die Firma MGG Netherlands in Tegelen, ein Spezialist für Alu-Sandguss. Die Firma MGG bietet ihren Kunden auch eine zerspanende Bearbeitung der Alu-Gussprodukte an und war auf die von Theilinger gebaute Doppelspindel-Fräsmaschine aufmerksam geworden. Auf der Maschine sollten die Dichtseiten der Wärmetauscher für die Warmwasserbereitung bearbeitet werden.
Durch die hohe Produktivität der Bearbeitung in einem Schnitt, reichte für die neue Aufgabe, die Kapazität einer Einspindel-Fräsmaschine. Aufgrund der positiven Erfahrung mit der INGERSOLL Werkzeuge GmbH bei der Entwicklung der Bearbeitung der Steuerteile im eigenen Hause war es bei den Fertigungsverantwortlichen bei Theilinger keine Frage, die Ausrüstung dieser Kundenmaschine mit INGERSOLL Werkzeugen zu planen.
Basierend auf den Erfahrungen mit dem gelöteten Planfräser bei Theilinger wurde der neue Planfräser mit dem gleichen Verteilsystem für die MMS ausgelegt. Auf ausdrücklichen Kundenwunsch sollte aber mit einem Wendeschneidplatten-Werkzeug gearbeitet werden. Es war bekannt, dass die Lamellen an den Wärmetauschern bei der Bearbeitung stark zum Schwingen neigen. Um Sicherheit zu erhalten, wurde deshalb zunächst eine Testbearbeitung an dem originalen Werkstück geplant.
Dem Vorschlag von Herrn Johannes Post (Produktmanager PKD INGERSOLL), die Testbearbeitungen im Tech-Center bei INGERSOLL durchzuführen, wurde von den verantwortlichen Mitarbeitern der Firma Theilinger sofort zugestimmt.
Testbearbeitungen im INGERSOLL Tech-Center
Wie schon bei den ersten Zerspanungsversuchen bei der Bearbeitung der Steuerteile, wurde auch bei den Tests im INGERSOLL Tech-Center zu Beginn auf ein Standard Werkzeug zurückgegriffen. Dabei wurde sowohl die labile Spannung für den späteren Einsatz berücksichtigt, als auch die geforderte Oberflächengüte und „Gratfreiheit“, die zur weiteren Bearbeitung notwendig ist. Weiterhin war die optimale Schnittgeschwindigkeit zu ermitteln, um der Gefahr, der zum Schwingen neigenden Lamellen zu begegnen. Nach einem Test mit verschiedenen Parametern stellte sich eine Schnittgeschwindigkeit von vc = 2000 m/min als die ruhigste heraus.
Das für die Tests eingesetzte Werkzeug war ein V-MAX Egalisier-Schlichtfräser aus der Automobil Serie mit einem Durchmesser von 315 mm. Um die labile Spannung zu berücksichtigen und mögliche Vibrationen zu vermeiden, wurde das Werkzeug nicht komplett bestückt, sondern lediglich mit 13 polierten Hartmetall-Schrupp-schneiden und 4 Breitschlichtschneiden. Bei den ersten Zerspanungsversuchen wurde als Schneidstoff für die Breitschlichtschneide Cermet gewählt, wobei sich jedoch herausstellte, dass diese Schlichtschneide zu starker Gratbildung an den Kanten des Werkstückes führte. Eine Umstellung des Schneidstoffes der Schlichtschneide von Cermet auf PKD-Bestückung brachte Abhilfe.
Nachdem die Zerspanungsversuche im INGERSOLL Tech-Center nach den angesprochenen Optimierungen zur vollsten Zufriedenheit der Firma Theilinger und des Endkunden abgeschlossen wurden, fertigte man das Produktionswerkzeug entsprechend den Zerspanungsergebnissen an. Nach Fertigstellung des Produktionswerkzeuges fand dieses bei Maschinenabnahme bei der Firma Theilinger erfolgreichen Einsatz.
Kontakt: