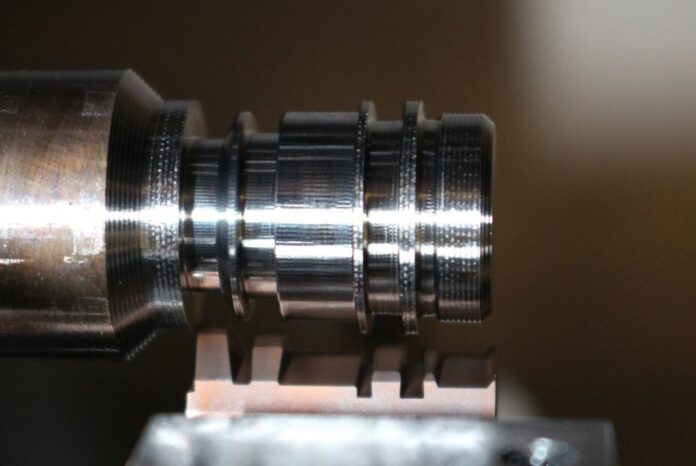
Die Günter Apelt GmbH wurde 1965 im schwäbischen Rosenfeld gegründet und hat sich in den vergangenen mehr als 50 Jahren als gefragter Hersteller von Präzisionsteilen etabliert. Die 45 Mitarbeiter drehen, fräsen, stechen und schleifen im Zweischichtbetrieb Komponenten für Kunden aus der Luft- und Raumfahrt, aus der Mess- und Regeltechnik, der Food- und Beverage-Branche sowie der Medizin- und Antriebstechnik in Deutschland und der Schweiz. „Wir fertigen hauptsächlich Bauteile mit komplexen Geometrien aus schwer zerspanbaren Materialen“, erklärt Björn Schmid, Vertriebsleiter bei Apelt. „Die große Herausforderung dabei ist, immer komplexer werdende Teile mit immer engeren Toleranzen in sehr guter Qualität zu liefern.“ Prozesssicherheit und Standzeit der eingesetzten Werkzeuge sind hierbei entscheidende Faktoren.
„Bei beiden war bei der Produktion einer Hülse für die Flugsteuerung in einem zivilen Flugzeug, die wir regelmäßig auf der Maschine haben, noch Luft nach oben“, ergänzt Viktor Reich, Ausbilder bei Apelt. Die 18 Millimeter lange Komponente wird aus Stangenmaterial 1.4545.4 mit einer Zugfestigkeit von 1.050 Newton pro Quadratmillimeter und einem Durchmesser von 20 Millimetern gefertigt. Das Apelt-Team dreht diese auf 15 Millimeter vor, bringt verschiedene Einstiche, Bünde, Absätze, Freistiche sowie Bohrungen ein und sticht die Komponente schließlich ab. Zwischen 16.000 und 18.000 Stück stellt der Lohnfertiger jedes Jahr her.
Bislang setzte das Unternehmen zum Vor- und Fertigstechen der Konturen eine 2,24 Millimeter breite Platte eines ISCAR-Mitbewerbers ein. „Allerdings hatten wir hierbei mit unregelmäßig auftretenden Ringspänen, viel Ausschuss, Standzeiten von unter 200 Teilen pro Schneide und hohen Werkzeugkosten zu kämpfen“, schildert Reich die Problematik. „Aus Sicherheitsgründen wechselten wir den Schneideinsatz jeden Morgen, und auch die Standzeit des Schlichtwerkzeugs im anschließenden Bearbeitungsschritt war beeinträchtigt.“
Sonderwerkzeug als Lösung
Bei einem der regelmäßigen Besuche von Andreas Walz, Beratung und Verkauf bei ISCAR, kam das Thema zur Sprache. „Apelt arbeitete hier mit einem aufwändigen Prozess – Vorstechen, Fertigstechen, Flanken kopieren –, der zu unbefriedigenden Ergebnissen in Qualität und Quantität führt“, erzählt Walz. „Für mich ein klarer Fall: Die Lösung heißt Profilstechen mit einer maßgeschneiderten PENTA 27-Platte.“ Diesem Vorschlag begegnete das Apelt-Team erst mit Skepsis.
„Das hatten wir vor zehn oder zwölf Jahren schon einmal mit einem Werkzeug eines Mitbewerbers und nur mäßigem Erfolg versucht“, sagt Reich. „Unter anderem waren die auftretenden Vibrationen damals einfach zu hoch. Doch seitdem ist in der Werkzeugentwicklung viel passiert, und da Andreas Walz praktisch zur Belegschaft gehört und wir auf seinen Rat vertrauen, gaben wir der Idee eine Chance.“
Erfolg auf ganzer Linie
Zusammen mit Erik Hoffmann, Produktspezialist Non-Rotating Tools bei ISCAR, und in enger Absprache mit Reich machte sich Walz an die Auslegung des passenden Schneideinsatzes. „Mit dem fünfschneidigen Präzisionsstechwerkzeug PENTA 27 lassen sich komplexe Profile mit Breiten bis zu 20 Millimetern und einer Stechtiefe von vier Millimetern in nur einer Bewegung maßgenau in wenigen Sekunden herstellen“, erklärt Hoffmann. Alle Parameter des Schneideinsatzes wie Kantenverrundung, Beschichtung und Spanleitgeometrie sind auf die Anforderungen beim Kunden maßgeschneidert.
Ausschlaggebend für die Leistung und eine einwandfreie Funktion ist das optimale Zusammenspiel von Schneidkantenpräparation, Beschichtung, Spanwinkel und Substrat. „Und beim vorliegenden Werkstückstoff spielt auch die Kühlung eine entscheidende Rolle, da bei der Bearbeitung sehr viel Wärme ins Werkzeug wandert, die der Schneide zusetzt“, ergänzt Hoffmann. Deshalb verfügt das Werkzeug über innenliegende Kanäle, die das Kühlmittel direkt in die Schnittzone transportieren. Nur das Verhältnis zwischen der Schnittbreite der PENTA 27 und dem Durchmesser des Werkstücks ließ das ISCAR-Team kurz zögern.
Es bestand die Gefahr, dass der hohe Schnittdruck bei der Bearbeitung das Werkstück wegdrücken könnte, was zu Toleranzproblemen führen würde. „Das Verhältnis von Materialdurchmesser und Schnittbreite liegt hier bei etwa eins zu eins, das ist schon grenzwertig“, sagt Hoffmann und grinst. „Aber manchmal muss man eben Risiken eingehen.“ Und das Ergebnis sollte ihm recht geben. Über die Schnellschussline, ISCARs Premium-Service für die PENTA-Linie, waren die Maßanfertigungen zusammen mit den passenden Haltern in nur drei Wochen beim Kunden. „Wir haben gemeinsam mit den Apelt-Leuten den ersten Stich gesetzt und – Bingo! Es hat gleich auf Anhieb gepasst“, erzählt Walz zufrieden.
Mit der PENTA 27 muss Viktor Reich jetzt nur noch einmal einstechen, um die angestrebten Konturen einzubringen. „Das funktioniert ganz hervorragend – rein, raus, fertig“, schildert er und zählt die Vorteile der neuen Lösung auf: „Die Ringspäne treten nicht mehr auf, die Oberflächengüten passen, wir können mit einer Schneide jetzt prozesssicher 1.700 Bauteile bearbeiten, die Ausbringung ist höher und als Leckerli nebenbei fahren wir auch noch schnellere Taktzeiten und haben geringere Werkzeugkosten.“
Kontakt: