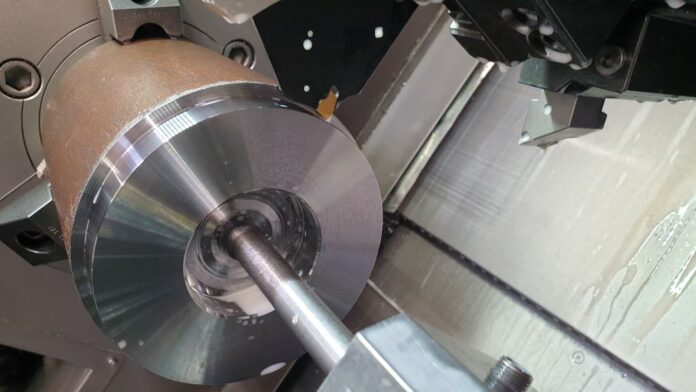
Der Lohnfertiger aus dem nordrhein-westfälischen Wipperfürth bearbeitet unterschiedliche Materialien, setzt aber einen klaren Fokus auf Edelstahl. Der Grund hierfür ist, dass Jürgen Müller im Verpackungsmaschinenbau arbeitete, bevor er sich 2009 selbständig machte. Aus diesem Bereich kamen auch die ersten Auftraggeber des jungen Unternehmens, für die bis heute Bauteile gefertigt werden. Inzwischen sind weitere Kunden aus dem Maschinenbau hinzugekommen, darunter auch weitere, bei denen die Lebensmittelindustrie eine besondere Rolle spielt. Nach seiner Ausbildung stieg Julian Müller ebenfalls in das Familienunternehmen ein, das aktuell elf Mitarbeiter zählt.
Zwar steht auch ein Fräszentrum zur Verfügung, doch werden hauptsächlich Drehteile hergestellt. Im Maschinenpark gibt es dafür zwei Zyklen-Maschinen von Weiler und eine ganze Reihe von Okuma-Maschinen, die JMD für unterschiedliche Werkstückgrößen angeschafft hat. Angefangen mit der kleinen Okuma LB2000, über eine LU3000, zwei LB3000 bis hin zur Okuma LB4000 kann damit ein Teilespektrum von 2 mm Passstiften bis zu Durchmessern von 420 mm bearbeitet werden, die maximale Bearbeitungslänge liegt bei einem Meter. Die gefertigten Stückzahlen reichen von der Einzelfertigung bis zu 5000 Teilen, wobei sich die gängigsten Losgrößen in der Serienfertigung zwischen 10 und 500 Stück, in der normalen Fertigung zwischen 1 und 10 Teilen bewegen.
Das Spektrum umfasst von Flanschen jeglicher Art, über Führungslager bis zu Außendurchmessern von 130 mm und Längen von bis zu 700 mm, bis hin zu Antriebswellen mit maximaler Länge von 2,50 Metern, die in zwei Aufspannungen bearbeitet werden. Außerdem Distanzscheiben, die JMD in verschiedenen Abmessungen meist in größeren Stückzahlen fertigt. In der Regel werden dabei hohe Genauigkeiten und sehr glatte Oberflächen verlangt. Häufig benötigte Materialien sind am Lager verfügbar, womit der Lohnfertiger seinen Kunden kurze Lieferzeiten von einem Tag oder sogar noch am selben Tag bieten kann.
Empfehlung aus dem Netzwerk
Das kleine Unternehmen aus Wipperfürth ist gut in der Region vernetzt, was ihm die Möglichkeit gibt, Bauteile komplett mit Oberflächenbehandlungen wie Nitrieren, Eloxieren, Brünieren oder Glasstrahlen anbieten zu können. Als Probleme beim Fräsen des Chrom-Nickel-Werkstückstoffes 1.4301 auftraten, erhielt Julian Müller den Tipp von einem erfahrenen Zerspanungspartner und Lohnfertiger im Bereich Frästechnik, sich an INGERSOLL zu wenden.
Übermäßiger Verschleiß und Plattenbrüche machten ihm zu schaffen. Er nahm Kontakt zu Jochen Cramer auf, der als Handelsvertreter für INGERSOLL tätig ist und sofort eine Lösung parat hatte: einen Eckmesserkopf mit 50 mm Durchmesser mit sehr weichschneidenden BOMT-Wendeschneidplatten, die sich als ideal für die Anforderungen erwiesen.
Die guten Erfahrungen sorgten dafür, dass JMD anschließend auch INGERSOLL Werkzeuge zum Drehen einsetzte, um 1.4301 und den häufig verwendeten Werkstoff 1.4404 zu bearbeiten. Als Jochen Cramer die neuen Kataloge vorstellte, unter anderem das neuartige Stechwerkzeug WinCut, konnte niemand ahnen, dass bereits eine Woche später Bedarf dafür entstehen würde: Ein größerer Auftrag für Distanzscheiben mit einem Außendurchmesser von 130 mm und einer Bohrung von 60 mm, die aus dem vorvergüteten Werkzeugstahl 30CrNiMo8 gedreht und anschließend abgestochen werden sollten.
Mit dem Werkzeug, das Müller bisher zum Abstechen derartiger Teile verwendet hatte, war er alles andere als zufrieden. Weil die Bauteile eine gewisse Balligkeit aufwiesen, wurden sie mit Aufmaß abgestochen und in einer weiteren Aufspannung plangedreht.
Manchmal wurden Bauteile auch nur vorgestochen und anschließend abgesägt, da die maximalen Nutztiefen der vorhandenen Stechschwerter nicht mehr hergaben, ehe ein zweites Mal aufgespannt wurde. Die Spanabfuhr und die erreichten Standzeiten der HM-Wendeschneidplatten waren ebenfalls nicht zufriedenstellend.
Ideale Bauteile für das neue Abstechsystem
Mit ihrer großen Abstechtiefe waren die Distanzscheiben für Julian Müller die idealen Bauteile, um das neue Abstechsystem WinCut von INGERSOLL zu testen. INGERSOLL bietet das Werkzeug in drei unterschiedlichen Größen für Abstechdurchmesser bis 52 mm, 82 mm und 120 mm sowie mit zwei verschiedenen Breiten an. Für den Auftrag benötigte JMD die größte Ausführung, was dem Fertiger zugleich Flexibilität für künftige Bauteile bietet.
In Absprache mit INGERSOLL Anwendungstechniker Christopher Hees wählte Julian Müller die breitere Variante mit 3 mm. Damit liegt die Schnittbreite immer noch unter jener des Vorgängerwerkzeugs, mit 4 mm. Bei den zur Verfügung stehenden Wendeschneidplatten entschied sich Müller letztendlich für die schärfere SFJ, um ohne hohen Druck einen weichen Schnitt im Edelstahl zu bekommen und Schwingungen zu vermeiden.
In der Maschine zeigte sich noch ein weiterer Vorteil: Ohne die bislang vorhandene Störkante des breiteren Stechhalters kann jetzt mit einer guten Planflächenanlage sehr nah am Futter gearbeitet werden. „Dadurch erzeugen wir auch eine höhere Stabilität am Stechwerkzeug und können einen Millimeter schmaler abstechen, was sich positiv auf den Prozess ausgewirkt hat“, kommentiert Christopher Hees.
Die durch die Dreiecksform des mit dem Halter fest verschraubten Blades erzielte Kraftverteilung macht sich in der Stabilität des Abstechprozesses ebenfalls deutlich bemerkbar.
Auf Anhieb exzellente Qualität
„Das ist ganz anders als bei einem normal geklemmten Schwert“, betont Julian Müller, der von den Ergebnissen mit WinCut auf Anhieb begeistert war. Bei den Distanzscheiben bekam er in einer Aufspannung sofort perfekte Bauteile mit einer exzellenten Oberflächenqualität. Der Wegfall einer zweiten Aufspannung ist mit der damit verbundenen Zeiteinsparung ein großer Vorteil für die Produktion. Das Abstechen lief absolut vibrationsfrei und es zeigte sich, dass auch beim Stechen von Konturen wesentlich bessere Oberflächen erzielt werden.
Das Stechsystem von INGERSOLL löste auch Probleme mit Spänen, die zuvor bei den Edelstählen immer wieder mal aufgetreten waren. Hier zeigt sich eine weitere Stärke des WinCut Werkzeugs mit Innenkühlung. Das Kühlmittel wird durch Halter und Schwert aus zwei Richtungen zur Schneidplatte geleitet. Die gezielte Freiflächenkühlung von unten dient dazu, Späne aus dem Arbeitsraum herauszuspülen.
Eine zweite Düse kühlt die Schneide von oben. INGERSOLL hat die gewundenen Kühlkanäle per 3D-Druck in die Schwerter integriert, die am Standort Vaihingen-Horrheim produziert werden.
„30CrNiMo8 als Werkstoff ist eine Herausforderung, aber wenn man erst einmal weiß, wie das am besten funktioniert, macht die Zerspanung richtig Spaß“, lautet das Fazit eines mit dem Service von INGERSOLL rundum zufriedenen Julian Müller. „Das war eine gute Investition, besonders für die Zukunft.“ Das WinCut Abstech-system will er künftig auf weiteren Maschinen einsetzen.
Kontakt: