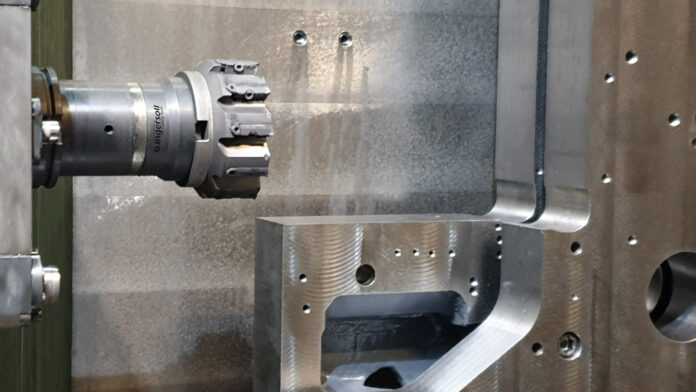
Die Manroland Sheetfed GmbH ist ein Druckmaschinenhersteller im Bereich Bogendruck. Das 1871 gegründete Unternehmen blickt auf eine lange Ingenieurstradition zurück. Die Offsetdruckmaschinen werden im Akzidenz-, Verpackungs- und Verlagsdruck eingesetzt, wobei sich die Verpackungen zunehmend zu einem Schwerpunkt entwickeln. Auch nach mehr als 500 Millionen Drucken verspricht der Hersteller hier konstante Qualität und Genauigkeit.
Manroland hat wirtschaftlich turbulente Zeiten hinter sich. Als das Unternehmen Ende 2011 in Insolvenz ging, verloren zwei Drittel der Mitarbeiter ihre Arbeitsplätze. In der Folge wurde die Firma von der privat betriebenen britischen Maschinenbaugruppe Langley Holdings aufgekauft. Dass Manroland dabei nicht zerschlagen, sondern weitergeführt wurde, sorgte in Offenbach für Erleichterung. Der neue Inhaber übernahm bereits zuvor eingeleitete Umstrukturierungsmaßnahmen. Ehemals neun Standorte wurden auf einem einzigen Werksgelände in Offenbach auf 114.000 Quadratmetern zusammengeführt.
Für die Produktion, in der heute knapp 900 Mitarbeiter tätig sind, war die Verkleinerung von Vorteil. In Offenbach ist ein moderner, integrierter Produktionskomplex mit kurzen Wegen entstanden. Angefangen mit der Herstellung der Rohteile in der eigenen Gießerei, wird über Forschung & Entwicklung, mechanische Fertigung, Elektrotechnik und Montage bis hin zum Versand der kompletten Maschinen alles selbst gemacht.
Die Fertigungstiefe bei den mechanischen Teilen ist mit über 80 Prozent sehr hoch. Die Bauteile werden im Werk gedreht, gefräst, gebohrt, verzahnt, geschliffen und gehärtet. „Weil wir alle wichtigen Teile selber fertigen, sind wir weitgehend unabhängig von Zulieferern“, erklärt Dirk Neuroth. Er ist seit 38 Jahren im Unternehmen, von denen er 21 Jahre lang Fertigungsmeister in der Großteilefertigung war. Seit drei Jahren ist er in der Produktion für die Werkzeuge verantwortlich.
Präzision eines Schweizer Uhrwerks
Mit der Präzision eines Schweizer Uhrwerks werden die kritischen Komponenten jeder Roland Druckmaschine gefertigt, schreibt das Unternehmen in einer Imagebroschüre. Vom Westentaschenformat sind die Maschinen allerdings weit entfernt. Eine Druckmaschine besteht aus etwa 6.000 verschiedenen Teilen.
Der Antriebsstrang, den Manroland komplett selbst herstellt, erinnert mit seinen Verzahnungen an ein XXL-Uhrwerk. Hier finden sich Bauteile, die auf 4 µ genau produziert werden müssen. Das Teilespektrum in der Fertigung reicht von Kleinstteilen bis zu massiven Großteilen wie Seitenwänden und Druckzylindern. Daneben hat es die Fertigung auch mit Großteilen zu tun, wie etwa den massiven Seitenteilen oder den Druckzylindern.
Dirk Neuroth sieht es als seine Aufgabe an, Fehler in der Fertigung zu beheben und Verbesserungen einzubringen: „Die Situation ist bei uns immer noch angespannt. Wir stehen schon seit 20 Jahren unter dem Druck, ständig besser werden zu müssen.“ Ihm ist es wichtig, dass auftretende Probleme nicht nur verlagert, sondern tatsächlich gelöst werden.
In der Vergangenheit seien gelegentlich vermeintlich günstige Werkzeuge angeschafft worden, was an anderer Stelle die Kosten durch längere Bearbeitungs- und Rüstzeiten hochgetrieben habe. Wenn Neuroth heute auf die Kosten schaut, hat er das Gesamtbild im Blick. Von einer Problemlösung müssen alle Bereiche profitieren, so sein Credo.
Weil die mechanische Fertigung technologisch breit aufgestellt ist, kommt auch ein entsprechend großes Spektrum unterschiedlicher Werkzeuge zum Einsatz. Seit Manroland vor etwa 30 Jahren die ersten Werkzeuge von INGERSOLL einsetzte, kamen immer mehr hinzu. Beim Fräsen ist der Werkzeughersteller aus Haiger inzwischen der wichtigste Lieferant für die Offenbacher.
Großes Vertrauen setzt Neuroth in dessen Anwendungstechniker: „Wenn wir zusammen etwas gemeinsam ausarbeiten, bringen wir das in aller Regel auch gut zu Ende und kommen zu Lösungen. Durch die Unterstützung der Anwendungstechniker vor Ort haben wir jedes Mal viel Zeit gespart.“
Die Seiten sind entscheidend
INGERSOLL war auch wieder gefragt, als sich ein Problem in der Fertigung der großen Seitenteile für die Drucktürme manifestierte. Zwischen diesen beiden Seitenteilen werden später die Walzen eingebaut, durch welche das Papier geschoben und bedruckt wird. Bei der Bogenübergabe zwischen den Druckzylindern geht es um Toleranzen im Bereich von hundertstel Millimetern.
Um diese Genauigkeit zu erreichen, kommt den Seitenflächen der Seitenteile eine besondere Bedeutung zu. Eine Druckmaschine ist aus mehreren Drucktürmen aufgebaut, die an diesen Seitenflächen miteinander verbunden sind. Für die einwandfreie Funktion der Maschine ist es unbedingt erforderlich, die Flächen hier sehr präzise zu bearbeiten.
Noch auf der Maschine wird das fertige Bauteil ein erstes Mal vermessen. In der Praxis erwies sich das als unzureichend, weil dabei nur größere Abweichungen erkannt werden. Am Schluss kommen generell alle Seitenteile zur Überprüfung in den temperierten Messraum. Ein ums andere Mal bekam der Werker von hier die Rückmeldung, dass das Bauteil nicht in Ordnung ist.
Immer wieder wurden leichte Winkelfehler und Parallelitätsfehler festgestellt. Da die Abweichungen streuten, konnten die Ergebnisse auch über Korrekturen kaum beeinflusst werden. „Alles was sich nicht wiederholt, ist schwer zu greifen und schwierig zu lösen. Man tappt da immer etwas im Dunkeln“, schildert Neuroth die Situation.
Die großen Werkstücke, die eigentlich bereits fertig sein sollten, mussten dann jeweils wieder auf einem Bearbeitungszentrum entsprechend ausgerichtet und nachbearbeitet werden. Das erforderte jedes Mal viel Zeit und hat sich als starker Kostentreiber in der Produktion erwiesen. „Das war nicht zu verantworten, da mussten wir reagieren“, sagt Dirk Neuroth.
Bruno Koch, technischer Berater und Vertriebsmitarbeiter bei INGERSOLL, kann die Unzufriedenheit bei Manroland nachvollziehen: „Es darf nicht sein, dass man programmtechnisch eingreifen muss, um eine gerade Fläche zu bekommen.“
Zusammen mit Anwendungstechniker Bernhard Müller analysierte er die Bearbeitungssituation und wurde rasch fündig. Das verwendete Werkzeug, ein Eckfräser eines anderen Herstellers, baute einen zu hohen axialen Druck auf. Das hatte zur Folge, dass Bögen gefahren werden mussten, um die Fläche gerade zu bekommen.
Der Spitzschlichter 4W5D arbeitet mit wenig axialem Druck
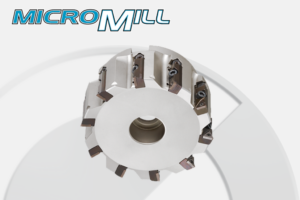
Damit war die Aufgabenstellung für INGERSOLL klar: Es galt, ein möglichst weich schneidendes Werkzeug zu finden, das wenig axialen Druck ausübt und damit prozesssicher die erforderliche Qualität am Bauteil erzeugt.
Die Wahl fiel auf den MicroMill 4W5D mit dem größeren Durchmesser von 125 mm, einem verstellbarem Schlichtwerkzeug. Der Fräser ist einstellbar, um seine zehn scharfen Hartmetallschneiden exakt zueinander auszurichten damit eine sehr genaue Oberfläche erzeugt werden kann. Mit seinen relativ kurzen Nebenschneiden wird er bei INGERSOLL auch als Spitzschlichter bezeichnet.
„Dieses Schlichtwerkzeug bietet mit der Geometrie seiner Wendeschneidplatten auch die Möglichkeit, sogar noch einen Hintergriff zu fräsen oder bei Bedarf einen Freistich oder Hinterschnitt an Schultern zu erzeugen“ machen“, erklärt Müller weitere Eigenschaften des Werkzeugs.
Zunächst ging es nicht darum, mit höherer Produktivität schneller oder günstiger zu fertigen, sondern ausschließlich um die Prozesssicherheit. Die Schnittwerte blieben daher anfangs unverändert und wurden eins zu eins übernommen. Die Schnittgeschwindigkeit von 334 m/min wurde übernommen. Der Erfolg stellte sich unmittelbar ein, die vorgegebenen Toleranzen wurden bei allen produzierten Teilen eingehalten.
Mit dem Wechsel von Hartmetall auf Cermet als Schneidstoff konnte in der Folge auch die Standzeit der Schneidplatten erhöht werden. Sie erreichte 100 Minuten und ermöglichte Manroland die problemlose Fertigung von 20 Seitenteilen.
Doppelter Vorschub, zwölffache Menge
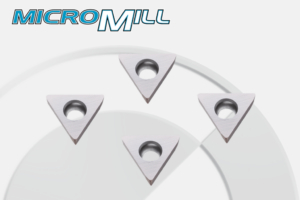
Ein weiterer großer Schritt wurde unternommen, als für das Werkzeug auch CBN-Schneiden serienmäßig verfügbar waren. Bernhard Müller setzte Wendeschneidplatten mit der Sorte IN80B ein. Sie erlaubten eine nahezu Verdopplung der Schnitt- und Vorschubgeschwindigkeit bei gleichzeitig auch noch 12-facher Standmenge mit nunmehr 350 Minuten eine wesentlich höhere Standzeit.
Damit wurde es möglich, 240 Bauteile prozesssicher mit einem Werkzeug zu produzieren, also die zwölffache Menge. Bei jährlich rund 1.100 gefertigten Bauteilen für unterschiedliche Baureihen macht sich diese Produktivitätssteigerung sehr deutlich bemerkbar.
Kubisches Bornitrid als Schneidstoff führte auch dazu, dass das Werkzeug nur noch selten eingestellt werden muss. Das entlastet die Mitarbeiter in der Werkzeugvoreinstellung und spart damit weitere Zeit. Neuroth freut sich über die gefundene Lösung und ist sehr zufrieden: „Der Anschaffungspreis des Werkzeugs war zwar höher, aber das hat sich binnen kurzer Zeit amortisiert. Durch den Einsatz des Spitzschlichters sparen wir viel Geld.“
Während im Werkzeugbereich immer wieder Neuerungen gefunden werden, wirkt der Maschinenpark etwas unzeitgemäß. Das hängt weniger mit mangelnder Investitionsbereitschaft zusammen als mit Sicherheitsdenken. Weil die großen Bearbeitungsmaschinen teilweise speziell auf das Teilespektrum von Manroland ausgelegt sind, ist es aus Sicht der Fertigung vernünftig, so eine Maschine lieber einem Retrofitting zu unterziehen als Neuanschaffungen zu tätigen. So kommt die Produktion wieder auf einen aktuellen Stand ohne das Risiko einzugehen, dass Probleme in den Prozessen auftreten oder eingefahrene Prozesse umgestellt werden müssen.
Im Rahmen von Lohnfertigung werden hier auch Bauteile hergestellt, die nichts mit Druckmaschinen zu tun haben. Die Gießerei produziert beispielsweise auch Klavierrahmen, die gelegentlich auf den Großmaschinen nebenan gleich mechanisch bearbeitet werden.
Kontakt: