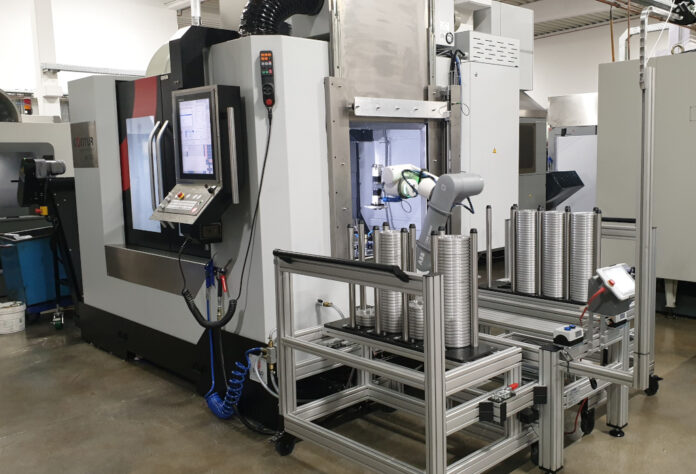
Bei der Firmengründung 1994 stellte das Unternehmen Präzisionsteile für den allgemeinen Maschinenbau und die Lebensmittelindustrie her. Seit Dennis Moos und Andreas Ruhs 2013 die Geschäftsführung übernahmen, wurde das Branchen-Spektrum breiter und Metec beliefert auch Verpackungsindustrie, Luftfahrt, Optikmaschinenbau, Medizintechnik und Wasserkraftwerke mit Prototypen und Kleinserien.
Typische Stückzahlen liegen in der mit Zerspanungsmechanikern besetzten Frühschicht zwischen 1 und 5. Schwerpunkt ist die Zerspanung von Aluminium, aber auch Edelstahl, Titan, Kunststoffe und weitere Materialien werden bearbeitet. In der Spätschicht kommen dann Serienaufträge auf die Bearbeitungszentren, welche durch Maschinenbediener bestückt werden.
Dennis Moos und Andreas Ruhs erweiterten auch das Geschäftsfeld Motorsport und Kfz-Tuning. Neue Kunden findet Metec hier immer wieder mal direkt an der Rennstrecke. „Je präsenter wir da sind, desto größer ist die Mundpropaganda“, berichtet Ruhs. „Mittlerweile kommen viele Hersteller zu uns, weil sie auf diesem Weg erfahren haben, dass wir uns auf bestimmte Teile spezialisiert haben und dass wir wissen, worauf es ankommt. Im Tuningbereich haben wir eine besondere Expertise aufgebaut.“
Neben Bremsen für den Rennsport hat Metec hier bereits Getriebegehäuse, Kupplungsdeckel, Schalteinheiten, Achsteile und ein breites Spektrum an Fahrwerksteilen hergestellt. Ausgestattet werden unter anderem Fahrzeuge, die an Rennserien wie dem Langstreckenpokal, GT3, GT4 oder der DTM teilnehmen.
Mitunter werden für den Rennsport auch mal schnell Teile übers Wochenende gefertigt. Das Unternehmen verfügt über eine große Fertigungstiefe. Neben zerspanten Dreh- und Frästeilen liefert es auch hochstabile Bauteile aus Carbon, Glasfaser oder Kevlar aus dem 3D-Drucker. Gängige Oberflächenbehandlungen wie Schleifen, Glasperlenstrahlen, Gravieren und Laserbeschriftungen gehören ebenfalls zum Programm.
Hohe Qualität in kurzer Zeit
Schnelle Reaktionszeiten sind dem Hersteller wichtig. „Wenn es sich nicht gerade um sehr große Stückzahlen handelt, können wir alles sofort abdecken“, versichert. Andreas Ruhs. Basis dafür ist ein gut bestücktes Materialager, das auf einer Fläche von 600 Quadratmetern stets verschiedene Rohstoffe bereithält. Im Zusammenspiel mit dem gut aufgestellten Maschinenpark gewährleistet dies eine schnelle und flexible Fertigung.
In der Werkshalle stehen fünf Drehmaschinen und 17 Fräszentren. Auf jeden der Facharbeiter in der Produktion kommen damit zweieinhalb Maschinen. So hat Metec praktisch immer eine Maschine frei, um bei Bedarf schnell zu reagieren. Hilfreich für die Fertigung von Einzelteilen ist dabei, dass jeder dieser Mitarbeiter auch programmieren kann.
Lange Zeit hatte Metec seine Werkzeuge bei einem einzigen Lieferanten bestellt. „Das war vielleicht der Bequemlichkeit geschuldet“, vermutet Dennis Moos. Seit 2013 ist die Firma dazu übergegangen, Werkzeuge ins Haus zu holen, die optimal für die jeweiligen Anwendungen geeignet sind.
Auf INGERSOLL wurde man aufmerksam, als das Unternehmen einen Serienauftrag für Flugzeugbauteile aus Titan erhielt. Immer wieder kommt es vor, dass ein Kunde nach gut gelungenen Musterteilen auch die weitere Produktion an den Fertiger vergibt. Bei dem Bauteil ging es um das Fräsen tiefer Taschen mit kleinem Radius. „Bei dem nicht einfachen Werkstoff Titan brauchten wir die passende Technologie und den Partner zur Unterstützung“, berichtet Moos.
Kevin Richstein, technischer Berater bei INGERSOLL involvierte hier auch das TechCenter des Unternehmens in Haiger. Mit der dort gefundenen Lösung konnte Metec die Bearbeitung eines Bauteils von zweieinhalb Stunden mit den schon vorhandenen Werkzeugen auf weniger als eine Stunde verkürzen.
Die Zufriedenheit mit Werkzeug und Betreuung sorgte dafür, dass nach und nach immer mehr Werkzeuge von INGERSOLL ins Haus geholt wurden. Inzwischen stammen etwa 25 Prozent der Werkzeuge von INGERSOLL. Bei Metec unterstreicht man die einfache Kommunikation mit dem Werkzeughersteller und den schnellen Service.
Spurverbreiterung in Serie
Für ein Großauftrag aus dem Bereich Autotuning war erneut die Expertise des TechCenters gefragt. Spurplatten sind klassische Tuningteile. Sie dienen zur Spurverbreiterung eines Fahrzeugs und sind in ihrer klassischen Ausführung einfache Aluminiumscheiben mit fünf Löchern. Auf Drehmaschinen mit angetriebenen Werkzeugen für die Bohrungen hat Metec für einen Kunden KW Automotive bereits Zehntausende davon hergestellt.
Ganz neue Spurplatten hat der Felgenhersteller BBS, seit 2021 Tochterunternehmen der KW Automotive, auf der Essen Motor Show 2022 unter dem Produktnamen „BBS unlimited“ vorgestellt. Als Nabenadaptersystem dienen sie dazu, Leichtmetallräder an nahezu alle gängigen Fahrzeuge zu montieren. Zuvor musste der Felgenhersteller für jede Automarke unterschiedliche Versionen auf den Markt bringen, weil die Lochkreisvarianten der Fahrzeuge untereinander abweichen.
Das neue System nutzt lediglich unterschiedliche Spurplatten als Adapter für verschiedene Autos, Felgen können markenübergreifend benutzt werden. Möglich macht das ein Kreis von zehn Löchern – fünf für die Felge und versetzt davon weitere fünf für die Montage am Fahrzeug. Die Radnabenadapter für das BBS unlimited System sind hochwertige Präzisionskomponenten, die im Gegensatz zu Wettbewerbsteilen einen passgenauen sowie sicheren Sitz garantieren.
Verglichen mit dem, was Metec sonst herstellt, sind diese Bauteile relativ einfach. Neue Herausforderungen stellte allerdings die Stückzahl dar. Nachdem einige Musterteile gefertigt waren, bestellte BBS gleich 120.000 Exemplare davon. Zusammen mit einem Auftrag von KW Automotive über 90.000 der einfachen Scheiben kommt Metec nun auf insgesamt 180.000 bis 230.000 Spurplatten jährlich.
Zwei effiziente Werkzeuge zum Fräsen
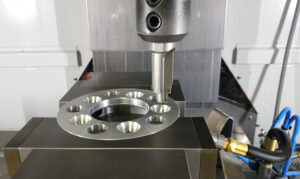
„In die neuen Spurplatten werden hinterher noch Muttern eingepresst, weshalb wir an diesen Artikel mit anderen Werkzeugen arbeiten müssen“, erläutert Ruhs die Ausgangssituation. „Weil diese Bearbeitung auf einer Drehmaschine zu lange dauern würde, sind wir mit diesem Bearbeitungsabschnitt auf die Fräsmaschine gegangen.“
Mit einem Stufenbohrer und einem 60-Grad-Senker stellte INGERSOLL für die effiziente Bearbeitung zwei Sonderwerkzeuge zur Verfügung. Bei der Auswahl der Wendeschneidplatten war das Wissen der Anwendungstechniker im Tech-Center gefragt. Aufgrund des sehr langspanenden Aluminiums, wurden Wendeplatten mit sehr positivem Spanbrecher und sehr guter Spanabfuhr verwendet.
Das war entscheidend für die Prozesssicherheit, da Metec die Produktion der Spurplatten für BBS automatisierte. Zunächst war deren Fertigung auf mehreren Fräsmaschinen angelaufen, in welche Mitarbeiter die auf dem CNC-Drehzentrum vorbearbeiteten Rohlinge per Hand einlegten. Damit hat Metec maximal ca. 300 Bauteile pro Tag geschafft. Um die Produktivität zu erhöhen, wurde kurzerhand eine weitere Fräsmaschine angeschafft und mit einem Roboter versehen.
Vieles konnte Metec dabei in Eigenregie ausführen. Vor seiner Zeit als Geschäftsführer in Eschenburg-Eibelshausen hatte Ruhs mehrere Jahre lang mit Robotern bestückte Fertigungsstraßen in der Automobilindustrie programmiert und in Betrieb genommen, was ihm bei diesem Projekt zugutekam. Auch die Peripherie hat Metec selber gestaltet, wobei sich das Augenmerk vor allem auf die Entfernung von Spänen aus dem Bearbeitungsraum richtete.
24 Stunden Fertigung nonstop
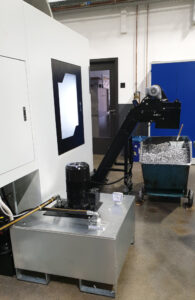
Durch die Prozessoptimierung und das Vereinen mehrerer Werkzeuge in einem Stufenbohrwerkzeug FMQ015080JFR10, konnten die Nebenzeiten durch Werkzeugwechsel erheblich reduziert werden und Fertigungskapazitäten freigesetzt werden. Das Sonder-Stufenbohrwerkzeug von INGERSOLL wurde mit Standardwendeplatten SHLT060204N-PH und SCLT050204N-PH aus der QuadDrillPlus-Serie in der Qualität IN2005 bestückt.
Mit der gewählten Schneidstoffqualität und optimaler Spanabfuhr konnte der bisher eingesetzte Gesamtvorschub vom Marktbegleiter mit 350 mm/min auf 550 mm/min deutlich übertroffen werden. Durch die Standzeiten kann die Serienproduktion trotz Schnittwerterhöhung der eingesetzten Wendeplatten sehr prozesssicher und zuverlässig stattfinden. Zudem wurden die Schwingungen beim Einsatz der bisher verwendeten Werkzeuge mit der Umstellung auf das INGERSOLL Werkzeugbohrsystem egalisiert, was die Qualität der Bearbeitung erhöhte.
Außerhalb des Arbeitsraums gibt es zwei Puffer für die Bestückung des Roboters, die maximal 420 Scheiben mit einer Stärke von 14 mm aufnehmen können. Damit arbeitet die Maschine mit dem Roboterarm achteinhalb Stunden mannlos. Wird dieser Puffer am Ende der zweiten Schicht nochmal gefüllt, kann 24 Stunden am Tag nonstop produziert werden. Damit sind Stückzahlen von 900 bis 1.200 Scheiben möglich.
„Mit den Werkzeugen, die wir zusammen mit der Anwendungstechnik von INGERSOLL eingefahren haben, sind wir überhaupt erst in die Lage versetzt worden, mit nur einer Maschine diese Stückzahl zu bedienen“, sagt Ruhs. Der Prozess und der Werkzeugeinsatz verlaufen dabei sehr sicher. Die Werkzeuge überzeugen mit sehr guten Standzeiten und hoher Maßhaltigkeit bis zum Schluss. In den automatisierten Prozess muss kein Bediener eingreifen. „INGERSOLL sieht sich als Partner für die gesamte Prozesskette und legt großen Wert darauf, den Kunden Automation näher zu bringen“, unterstreicht Kevin Richstein.
Mit den positiven Erfahrungen im Rücken sieht sich Metec in der Lage, jederzeit weitere automatisierte Maschinen in Betrieb zu nehmen, um bei Bedarf Serien zu bearbeiten. Auch in der bestehenden Fertigung wird noch eine weitere Automatisierung erwogen, denn die Produktion der einfachen Spurscheiben erfolgt momentan noch per Handbeladung auf der Drehmaschine.
Kontakt: