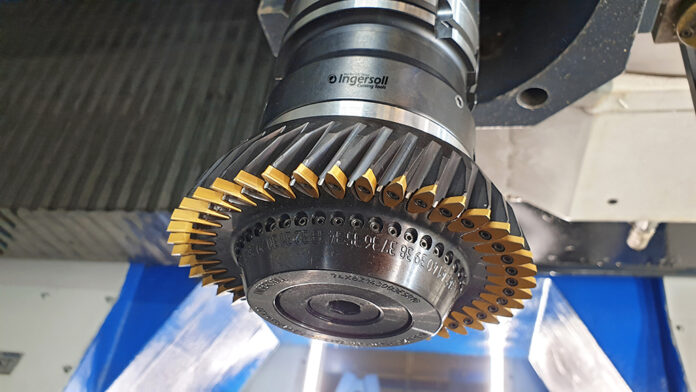
Als die Entscheidung über die Anschaffung einer Maschine anstand, fiel die Wahl nicht ohne Grund auf eine Schleifmaschine. Zum Portfolio der IBO gehören auch Wälzlager, deren Laufbahnen hochgenau geschliffen werden müssen. Die erforderliche Genauigkeit von 5 µm ist mit anderen Fertigungstechnologien nicht realisierbar. IBO wählte daher mit dem vertikalen Schleifzentrum Kehren RP 8 eine Maschine, auf der nicht nur verschiedene Arten des Schleifens, sondern auch Drehen, Bohren und Fräsen möglich sind.
IBO stellt Lager im Durchmesserbereich von 200 mm bis 1200 mm her. Die besondere Stärke des Unternehmens sind schlanke digitale Prozesse, um solche Teile binnen kürzester Zeit auslegen zu können, was durch eine eigene Digitalfirma unterstützt wird. Von der Anfrage für ein bestimmtes Teil bis zur Fertigung des Lagers dauert es bei IBO gerade mal drei bis vier Tage, während Mitbewerber dafür sechs bis acht Wochen brauchen. Dahinter steckt ein ausgeklügeltes Konfigurationsmanagementsystem in CAD, das Modelle anhand von Parametern aufbaut.
Ein Laufringlager für viele Zwecke
Pro Jahr werden in Kirchheim rund 1.200 verschiedene Teile produziert. Meist geht es dabei um Kleinserien von 10 bis 20 Stück. Weil dieses Volumen nicht auf einer einzigen Maschine zu bewältigen ist, ist der Fremdvergabeanteil relativ hoch. Gelegentlich werden von einem Bauteil aber auch höhere Stückzahlen verlangt. Das war bei einem Laufringlager der Fall, das in unterschiedlichen Bereichen verbaut wird.
Den Gepäckscanner am Flughafen bewegt es einmal um das Gepäckstück auf dem Band. Im Computertomographen ermöglicht es einen ganz ähnlichen Bewegungsablauf um den Patienten herum. Hinzu kommen Anwendungen in der Wehrtechnik, für die IBO seit 2013 ebenfalls tätig ist. Hier wird das Laufringlager für den Seitenrichtantrieb an Waffenstationen eingesetzt, wo es als Schnittstelle zwischen feststehendem und drehendem Element fungiert.
Das Bauteil besteht aus hochfestem Aluminium, wie es auch in der Luft- und Raumfahrt eingesetzt wird. Der Laufkreisdurchmesser, auf dem später der Wälzkörper läuft, misst 660 mm. Die Innenverzahnung besteht aus 189 Zähnen des Moduls 3. Insgesamt erreicht das Bauteil eine Stückzahl von rund 500, was bei IBO schon als Großserie gilt. Nicht zuletzt strenge Audits durch die Kunden machten die Produktion bei IBO im Haus erforderlich.
Florian Lemberger, Technischer Geschäftsführer der IBO, fragte bei INGERSOLL an, wie die Innenverzahnung auf der vorhandenen Maschine am wirtschaftlichsten hergestellt werden kann. „Ich habe ganz bewusst offen gefragt und keine Vorgaben gemacht, denn INGERSOLL kennt seine Werkzeuge schließlich am besten“, erläutert er. Michael Bum, Technischer Berater bei INGERSOLL, machte sich daraufhin mit dem zu fertigenden Bauteil vertraut und hat die Produktionsumgebung vor Ort begutachtet. Zügig unterbreitete er einen Vorschlag: Wälzschälen ist die schnellste und wirtschaftlichste Lösung.
Bei der auch als „Power Skiving“ bezeichneten Technik wird durch einen Achskreuzwinkel das Werkzeug schräg zum Werkstück angeordnet. Durch die Schrägstellung findet ein Abtrag statt: Die Zähne des Werkzeugs arbeiten sich schräg hinunter, beschreiben eine Ellipse und schaben dabei aus dem Rohling Material heraus. Eine breitere Anwendung findet das Wälzschälen erst, seit Bearbeitungszentren und Universalmaschinen mit voll synchronisierten Spindeln und verfahrensoptimierter Software die Anwendung dieser hochkomplexen Technologie ermöglichen.
INGERSOLLS Premiere auf der Schleifmaschine
INGERSOLL ist seit 2014 mit Werkzeugen für das Wälzschälen am Markt und hat seither schon viele Projekte zusammen mit Maschinenherstellern umgesetzt. In den vergangenen Jahren wurden Werkzeuge von Modul 2 bis Modul 12 mit Wendeschneidplatten hergestellt. Für kleinere Durchmesser bis etwa 60 mm bietet Ingersoll VHM-Wälzschälräder von Modul 0,4 bis 2,5 an.
Auf einer Schleifmaschine wurden die Werkzeuge aus Haiger allerdings noch nie eingesetzt. Michael Bum war zuversichtlich, dass das im Zusammenspiel von Drehtisch als C-Achse und der in Z-Richtung verfahrenden Schleifspindel klappen könnte. Bevor INGERSOLL ein Sonderwerkzeug für die konkrete Anwendung auslegte, musste aber zunächst abgeklärt werden, ob tatsächlich alle Voraussetzungen dafür gegeben sind. Dafür wurde der Maschinenhersteller Kehren mit ins Boot geholt.
Mit Sonderwünschen von IBO war man dort bereits vertraut, da sämtliche Bearbeitungen auf der RP 8 ausgeführt werden. Die Anfrage nach dem Wälzschälen sorgte allerdings zunächst für Stirnrunzeln. „Auf einer unserer Schleifmaschinen wurde das Wälzschälen noch nie eingesetzt. Ich musste mir das erst mal auf YouTube anschauen, um einen Eindruck davon zu bekommen“, räumt Peter Ediger ein, Leiter Anwendungstechnik bei Kehren. Schließlich konnte er grünes Licht geben: „Die Maschinenausstattung ist dafür nicht unbedingt prädestiniert, aber man kann es damit machen.“
Zugute kam dem Projekt, dass es um die Zerspanung vom Aluminium ging. Im Gegensatz zu Frässpindeln sind Schleifspindeln für hohe Laufleistungen, hohe Drehzahlen und hohe Genauigkeit optimiert, aber nicht dafür, hohe Zerspankräfte aufzunehmen. Beim Schleifen wirken radiale Kräfte auf die Spindel, wofür die Lagerung entsprechend ausgelegt ist. Fräsprozesse erzeugen axiale Kräfte. Bei härteren Materialien hätte man wohl auf eine andere Spindel umsteigen müssen.
Ohne generische Kopplung geht’s nicht
Ganz entscheidend für das Gelingen waren darüber hinaus besondere Ausstattungsmerkmale der Maschine von Kehren. Während die Rundtische vieler anderer Schleifmaschinen mit Riemenantrieben oder Getrieben ausgestattet sind, werden hier sowohl der Tisch als auch die Spindel mit einem Torquemotor angetrieben.
Zusammen mit den verbauten Sensoren sind die Direktantriebe eine Voraussetzung dafür, dass die Bewegungen für das Wälzschälen synchronisiert werden können. Bei einer Umdrehung der Schleifspindel muss der Rundtisch im Verhältnis der Zähnezahl des Werkzeugs bezogen auf die Zähnezahl des Werkstücks bewegt werden. Steuerungshersteller Siemens bezeichnet diese Synchronisation als „generische Kopplung“.
Mit Unterstützung des Werkzeugherstellers gelang Peter Ediger die Programmierung des ungewohnten Verfahrens. Ausdrücklich würdigt er die gute Zusammenarbeit: „Von INGERSOLL haben wir sehr gute Informationen zu den Anforderungen für die Verzahnung und zum Werkzeug bekommen. Anhand dessen konnte ich den Zyklus erstellen. Ausgesprochen nützlich waren Tipps, wie man das eine oder andere am besten löst.“
Bei INGERSOLL ist Markus Grebe, Produktmanager Formwerkzeuge, bestens mit den Details vertraut. Um die verlangte Qualität für die Verzahnung zu erreichen, hat er sich für eine degressive Zustellung in 14 Schritten entschiedenen. Am Anfang wird mit einer größeren Zustellung zerspant, die dann immer weiter reduziert wird.
Markus Grebe erläutert, warum das Wälzschälen nicht in einer Zustellung erfolgen kann: „Beim Eintritt des Werkzeugs haben wir einen positiven Spanwinkel, beim Austritt einen negativen. Dieses Verhältnis ändert sich bei jeder Zustellung. Damit ergeben sich bei jeder Zustellung andere Eingriffsverhältnisse und Eingriffslängen. Das macht die Sache spannend.“
43 Schneiden für 189 Zähne
Tools für das Wälzschälen sind grundsätzlich Sonderwerkzeuge, die an das jeweilige Bauteil und die Verzahnungsbreite angepasst sind. Sowohl die Werkzeugaufnahme als auch die Wendeschneidplatten werden nach Maß gefertigt. Das Werkzeug für die 189 Zähne am Laufringlager von IBO hat INGERSOLL mit 43 Schneiden ausgelegt. Für die Schneidplatten wurden rhombische Rohlinge verwendet, die bei INGERSOLL in Haiger profilgeschliffen und beschichtet wurden. Damit der Maschinenbediener alle notwendigen Parameter für Werkzeug und Bauteil eingeben kann, liefert INGERSOLL auch eine Kollisionsdarstellung mit.
Bei IBO drückte die Zeit: Um den Prozess zum Laufen zu bringen, blieben am Ende gerade mal 48 Stunden Zeit. Michael Bum und Markus Grebe begleiteten die Tests vor Ort, bei denen Schnittwerte, Zustellungen und Vorschübe variiert wurden, um zu einem optimalen Ergebnis zu kommen. Im besonderen Fokus standen dabei die jeweils erzeugten Zahnflanken. Um zum gewünschten Ergebnis zu kommen, reichte ein Probeteil aus.
„Die Maschine machte, was sie soll. Letztendlich ging es nur um ein paar wenige Stellschrauben, an denen wir noch drehen mussten“, berichtet Michael Bum. Beim Test wurde auf Anhieb eine Rundlaufgenauigkeit von 5/100 mm erreicht, die nächsten Teile erfüllten bereits die vorgegebene Verzahnungsqualität 8 nach DIN3961. Die Fertigung einer Verzahnung dauert rund 20 Minuten.
Der Kunde ist von den Ergebnissen sehr angetan. „Das Knowhow von IBO liegt zwar in erster Linie im Engineering, aber die beste Zeichnung würde nichts nutzen, wenn wir ein Lager nicht auch liefern können“, sagt Florian Lemberger. Er freut sich darüber, die Durchlaufzeit in der Produktion selber in der Hand zu haben und damit flexibler zu sein. „Ein Erfolgsgarant war, dass sich drei Firmen gefunden haben, die sehr kompetent zusammenarbeiten konnten. Die Zusammenarbeit mit diesen leistungsstarken Partnern hat richtig Spaß gemacht.“
Florian Lemberger kann sich vorstellen, das Wälzschälen auch für weitere Produkte einzusetzen. Betriebswirtschaftlich sinnvoll wäre die Anschaffung eines Sonderwerkzeugs nach seiner Kalkulation ab Produktionszahlen von etwa 75 Stück. Unter Umständen lassen sich mit den bereits vorhandenen Fräser sogar weitere Verzahnungen mit etwas mehr Zähnen herstellen. Möglicherweise kann das Trägerwerkzeug für andere Bauteile eingesetzt werden, wenn lediglich die Konturen der Schneidplatten darauf angepasst werden. Bei IBO verlässt man sich hier ganz auf die Beratung von INGERSOLL.
Kontakt: