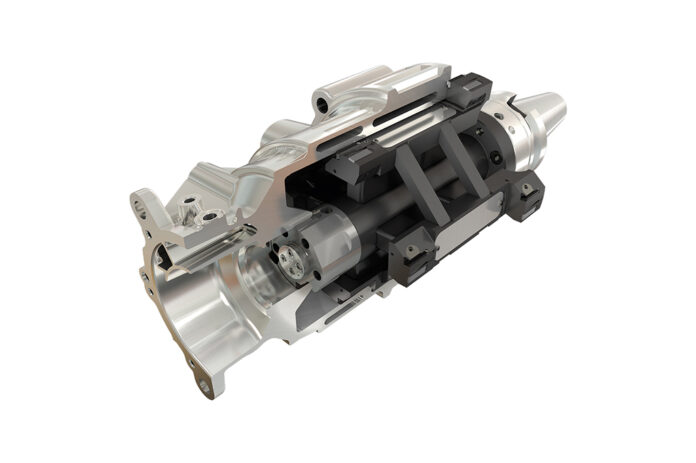
Der Klimawandel und der Umweltschutz haben weltweit zu einer Reihe von Gesetzen geführt, die die Automobilhersteller verpflichten, den Ausstoß klimaschädlichen Kohlendioxids (CO2) ihrer Fahrzeuge zu verringern. Der Technologiewandel „Downsizing“ ist allgegenwärtig und notwendig in der Automobilindustrie um dem neuen Leistungsanspruch gerecht zu werden.
Effizientere, meist turboaufgeladene Motoren sind ein zwischenzeitlicher Stand, um bei geringerem Kraftstoffverbrauch gleiche oder höhere Leistung zu erzielen. Vor dem Hintergrund endlicher fossiler Brennstoffe, sowie zukünftig strengerer Emissionsreglementierungen, vollzieht sich aktuell ein stark spürbarer Wandel hin zu alternativen Antriebstechnologien um den bekannten Verbrenner ganz oder teilweise zu ersetzen – beispielsweise durch elektrische Lösungen.
Der rasante Anstieg in der Entwicklung, Herstellung und Implementierung batterieelektrischer Fahrzeuge (BEV) zeigt: Elektrofahrzeuge sind eine gegenwärtige und zukunftsfähige Lösung. Nicht nur die Automobilindustrie steht vor grundlegenden Veränderungen – die komplette Wahrnehmung von Autos und Verkehr in der Gesellschaft ist im Wandel.
ISCAR hat Technologien und Trends stets im Blick. Die Ingenieure entwickeln kontinuierlich neue Werkzeuge und verbessern bestehende Linien weiter. Deshalb kann ISCAR die Unternehmen bei der Umstellung auf Produkte für die E-Mobilität mit cleveren, innovativen und effizienten Bearbeitungs-Lösungen für ihre Komponenten unterstützen.
Komplettbearbeitung des Stator-Gehäuses
Im Vergleich zum Verbrennungsmotor besitzt der Elektromotor viel weniger bewegliche Teile. Für die Hersteller heißt das: kürzere Produktionszeiten und geringere Kosten. Eine der Hauptkomponenten eines Elektromotors ist das Motorgehäuse aus Aluminium. Um die Vorgaben hinsichtlich Gewicht, Haltbarkeit, Duktilität, Oberflächengüte, Präzision und geometrischer Toleranzen zu erreichen, ist ein besonderer Ansatz erforderlich. Die teilweise hohle Form stellt eine zusätzliche Herausforderung dar. Bei der Bearbeitung sind niedrige Schnittkräfte notwendig, um die Anforderungen an Oberflächengüte und Zylindrizität zu erfüllen.
Dank ISCARs Komplett-Bearbeitungsstrategie können Hersteller die notwendigen Arbeitsschritte von kostspieligen Standardverfahren auf der Drehmaschine auf ein wirtschaftliches Bearbeitungszentrum verlegen. Damit erreichen sie weniger Ausschuss und optimieren ihre Fähigkeit, Teile innerhalb der erforderlichen Toleranz zu fertigen.
Reibbearbeitung des Hauptdurchmessers
Die größte Herausforderung bei der Bearbeitung des Aluminium-Statorgehäuses ist das Aufbohren und Reiben des Hauptdurchmessers. Ursachen hierfür: Die verwendeten Maschinen verfügen meist nur über eine geringe Leistung, das darauf eingesetzte Werkzeug besitzt einen großen Durchmesser und kragt lang aus. Es gilt also, das Gewicht des Werkzeugs und die entstehende Spindelbelastung zu minimieren und gleichzeitig die Stabilität zu erhalten. Deshalb verwendet ISCAR sowohl für den Werkzeugkörper als auch für die geschweißte Rahmenkonstruktion exotische Materialien wie Titan und Kohlefaser.
Bei der Konstruktion der Werkzeuge setzen die ISCAR-Ingenieure zudem auf die Finite-Elemente-Methode (FEM). Damit können sie Parameter wie Schnittkräfte, Verschiebungsfeld während der Bearbeitung, Eigenfrequenz und maximale Verformung schon bei der Konstruktion der Reibwerkzeuge berücksichtigen. So lassen sich Komplikationen bei dieser anspruchsvollen Anwendung vermeiden.
Lagersitzbearbeitung nach der Montage
Ein Elektromotor erzeugt sein maximales Drehmoment aus dem Stand. Das bedeutet, statt eines komplexen Getriebesystems, reicht für ein normales Elektrofahrzeug ein einfaches Untersetzungsgetriebe aus. Dieses sitzt zwischen dem Statorgehäuse und der Getriebeabdeckung.
Um den Rundlauf zwischen dem Lagersitz des Stators und der Getriebeabdeckung sicherzustellen, muss das Reiben der beiden Komponenten im gleichen Bearbeitungsschritt erfolgen. Speziell dafür hat ISCAR „Push and Pull“-Reibwerkzeuge mit einstellbaren PKD-Schneiden im Portfolio. Damit kann der Anwender die geforderten geometrischen Toleranzen auch bei unterschiedlichen Innendurchmessern am Aluminiumteil einhalten.
Drehen des Rotors
Der Rotor eines Elektromotors besteht aus vielen gestapelten Elektrostahl-Platten. Um Stromverluste zu reduzieren, werden Laminierungsplatten anstelle eines soliden Körpers verwendet. Die Oberfläche des Rotors muss absolut frei von Spänen, Öl, Wasser, Staub oder Schmutz sein. Deshalb kann bei der Bearbeitung auch nur mit Luft gekühlt werden. Das macht den Prozess nicht ganz einfach. An der Schnittfläche entsteht viel Wärme, die Späne kleben an der Oberfläche und die Ansprüche an die Oberflächengüte dieses unterbrochenen Drehvorgangs sind hoch.
Dafür hat ISCAR ein kombiniertes Werkzeug mit Kühlmittelöffnungen an der Ober- und der Unterseite der Schneidkante zum Kühlen und Evakuieren der Späne entwickelt. Die beiden Rundschneideplatten sind für das Semifinishing und Finishing geeignet und erzeugen eine sehr hohe Oberflächengüte.
Batteriegehäuse Bohren
Bei einem Elektroauto ist die Batteriewanne ein integraler Bestandteil des Fahrzeugdesigns. Um das Gewicht dieser sehr großen Komponente möglichst gering zu halten, kommt hierbei meist Aluminium oder kohlenstofffaserverstärkter Kunststoff (CFK) zum Einsatz. CFK ist leichter, steifer und hat eine geringere Wärmeleitfähigkeit als Aluminium.
ISCAR hat eine breite Palette an Werkzeugen speziell für die Bearbeitung von Aluminium und CFK entwickelt. Anwender können damit alle Aufgaben produktiv und wirtschaftlich lösen. Beispielsweise bieten die SUMOCHAM-Wechselkopfbohrer eine Vielzahl von Geometrien und Schneidstoffen.
Speziell zum Bohren von Aluminium sind etwa ICN-Köpfe ausgelegt. Sie verfügen über sehr scharfe Schneidkanten und polierte Spanflächen. Für eine einfachere Spanevakuierung bei großem Überhang sind ICG-Köpfe mit Spanformern für kurze Späne ausgestattet. Zum Bohren von CFK bietet ISCAR eine spezielle ICF-Geometrie mit Diamantbeschichtung an. Mit diesem Bohrkopf sind auch typische CFK-Materialfehler wie Delamination kein Problem mehr.
Kontakt: