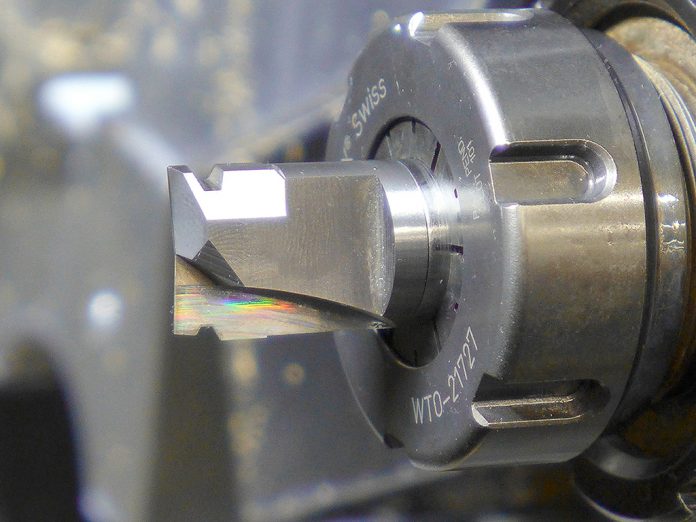
Stiebel Eltron GmbH & Co.KG ist eine international ausgerichtete Unternehmensgruppe und gehört weltweit zu den Markt- und Technologieführern in den Bereichen „Haustechnik“ und „Erneuerbare Energien“.
Der Schutz natürlicher Ressourcen hat in den letzten zwei Jahrzehnten einen zunehmend hohen politischen Stellenwert erreicht. Aber auch in der öffentlichen Wahrnehmung, besonders durch Demonstrationen und Aktionen, hat sich die Aufmerksamkeit der Bevölkerung auf das Thema „Erneuerbare Energien“ enorm verstärkt.
Als innovationsgetriebenes Familienunternehmen verfolgt die Stiebel Eltron bei der Fertigung und Entwicklung von eigenen Produkten eine klare Linie – für eine umweltschonende, moderne und komfortable Haustechnik.
Mit über 3700 Mitarbeitern weltweit arbeitet man an effizienten und innovativen Lösungen für Warmwasser, Wärme, Lüftung und Kühlung.
Im Jahre 1976 hat Stiebel Eltron mit der Entwicklung von Wärmepumpen begonnen. Heute ist das Unternehmen einer der führenden Anbieter von Wärmepumpen für Heizung, Kühlung und Warmwasserbereitung.
Im Verlauf der kontinuierlichen Prozessoptimierung haben die Produktionsverantwortlichen der Firma Stiebel Eltron in Holzminden sich die Aufgabe gestellt, die kompletten Fertigungsprozesse in der Automatendreherei zu analysieren.
Besonders der Bereich der Kurvenautomaten sollte intensiv auf Einsparung von Produktionskosten untersucht werden. Bei den Kurvenautomaten handelt es sich um kurvengesteuerte Traub Drehautomaten, die zwar schon länger im Einsatz sind, aber bei der Produktion von Serienkleinteilen noch immer hochproduktiv arbeiten.
Die Zielvorgabe war, im Bereich der gesamten Automatendreherei Produktionskosten einzusparen.
Zusammenarbeit mit INGERSOLL Werkzeuge GmbH
Marcel Gobrecht (Stiebel Eltron Gruppenleiter Maschinenpark und CAM Programmierer) wählte für dieses Vorhaben die Unterstützung der INGERSOLL- Fachleute Wolfgang Schuppe (INGERSOLL Beratung und Verkauf) und Michael Tobisch (INGERSOLL Anwendungstechniker).
„Ich habe mit beiden Herren in der Vergangenheit einige Optimierungsprozesse sehr erfolgreich erarbeitet und umgesetzt. Deshalb fiel die Wahl wieder auf INGERSOLL, da die Betreuung einfach vorbildlich ist.“, war die Argumentation von Herrn Gobrecht zu dieser Wahl.
Erste Optimierung: Bauteil Lötbuchse
Das erste Bauteil, das gemeinsam für eine Optimierung der Produktionskosten ausgewählt wurde, war eine Lötbuchse, die besonders nach einer Umstellung des Werkstoffes Probleme bei der Zerspanung bereitete.
Die Buchse wird in einer hohen Stückzahl pro Jahr auf einem der erwähnten kurvengesteuerten Drehautomaten produziert. Der Werkstoff der Buchse ist vor einiger Zeit von der Legierung CuZn39Pb2 auf eine bleifreie Trinkwasserlegierung CuZn21Si3P umgestellt worden.
Durch den Wegfall von Pb und den Zusatz von Si verschlechterte sich nicht nur die Spanbildung, sondern auch die Standzeit des Werkzeuges reduzierte sich bei der Bearbeitung des geänderten Werkstoffes dramatisch.
Der Spanbruch war mit dem geänderten Werkstoff nicht mehr akzeptabel, die langen Wirrspäne behinderten den Abtransport der Späne und es kam zu massiven Störungen in der automatisierten Fertigung, da die langen Späne Spanstau im Späneförderer verursachten.
Die Aufgabenstellung für Herrn Michael Tobisch war also nicht nur, einen kontrollierten Spanbruch zu erzeugen, der automatisierungsfreundliche, kurze Späne produziert, sondern auch die Produktionskosten deutlich zu reduzieren.
Für die gemeinsamen Tests wurde von den Herren Michael Tobisch und Wolfgang Schuppe eine Einstechplatte der Bezeichnung TGUX2506 konzipiert. Diese Einstechplatte konnte die gesamte Außenkontur der Buchse in einem Einstecharbeitsgang herstellen. Die geplante Einstechplatte stand nach kurzer Zeit zur Verfügung und zum Test bereit.
Die gewählte Einstechplatte ist im Verhältnis zu den Abmessungen des Halters mit dem Querschnitt 12×12 zwar relativ groß, im Verhältnis zum erzielten Erfolg handelt es sich aber um ein kleines Bauteil mit großen Auswirkungen.
Die ersten gemeinsamen Einsätze waren auf Anhieb chancenreich. Es gab keine Vibrationen beim Einstechen der Außenkontur, das Maß war konstant und die Spankontrolle deutlich besser.
Aufgrund des stabilen Schneidverhaltens der neuen Einstechplatte konnte trotz der labilen Schnittbedingungen, der Vorschub bei der Bearbeitung wesentlich erhöht werden. Die Produktionsmenge stieg von 190 Teile/Stunde auf 420 Teile/Stunde.
Die Erhöhung des Vorschubes wirkte sich zusätzlich positiv auf die Spanbildung aus. Die nun produzierten kurzen Lockenspäne stellen kein Problem für den Spanförderer mehr dar.
Eine weitere, nicht in diesem Umfang erwartete, Optimierung stellte sich erst nach längerem Einsatz der neuen Einstechplatten heraus. Die erreichte Standmenge stieg von 3500 Teile auf 75.000 Teile.
Dies ist eine Steigerung auf 2140 %, die ihre Gründe sicherlich zum Teil in der ruhigen Zerspanung, aber auch zum Großteil in dem exzellenten Schneidstoff hat.
Der gemeinsame Verbesserungsschritt in der Automatendreherei war also sowohl für Herrn Marcel Gobrecht als auch für Herrn Michael Tobisch ein voller Erfolg, denn die angestrebte Optimierung (kontrollierter Spanbruch und Fertigungszeiteinsparung) wurde weit übertroffen:
- Deutlich bessere Spanbildung für den automatisierten Prozess.
- Ausbringung mehr als verdoppelt
- Standmenge um den Faktor 21 erhöht
- Schneidstoffkosten (um 98 %) auf 2 % reduziert
Auf der Basis dieses positiven Ergebnisses wurden weitere Bearbeitungen mit Konturplatten in der Automatendreherei untersucht und Konturschneidplatten von INGERSOLL angefertigt. Bisher konnten schon mehrere verschiedene Bauteile auf die neuen Konturschneidplatten umgerüstet werden, die allesamt bei den Tests deutlich bessere Ergebnisse in Bezug auf Bearbeitungszeit und Standmenge gebracht haben.
Zweite Optimierung: Reduzierte Fertigungszeit durch Kombiwerkzeug
Nach der erfolgreichen Reduzierung der Fertigungskosten bei der Lötbuchse, konzentrierte man sich im nächsten Schritt auf die Innenbearbeitung. Ausgewählt wurde eine Mutter G1/2“ aus Messing, mit jährlich hoher Stückzahlenproduktion.
Herr Marcel Gobrecht und Herr Michael Tobisch waren sich einig, dass aufgrund der jetzigen Maschinenparameter eine Verbesserung der Schnittwerte für das Messingbauteil Mutter G1/2“ so nicht mehr möglich ist.
Die Lösung konnte nur in der Reduzierung der Werkzeugwechselzeit liegen. Die Idee bei dieser Optimierung war der Einsatz eines Kombiwerkzeuges.
Die komplette Innenbearbeitung (Herstellung der Bohrung und Anbringung der beiden Fasen, sowie das Hinterstechen) sollte durch ein Werkzeug erfolgen – einem ChipSurfer in Sonderausführung, der die gesamte Innenkontur in fünf Bearbeitungszyklen (inkl. Rückstellung) fertigstellt.
Der für diese Bearbeitung ausgewählte ChipSurfer ersetzt zwei bisher eingesetzte Werkzeuge und spart einen Werkzeugwechsel, inklusive Fasoperation.
Auch diese für die Mutterbearbeitung vorgesehenen Sonderwerkzeuge wurden innerhalb weniger Wochen produziert, und die Testbearbeitungen wurden Anfang des Jahres 2019 in der Automatendreherei bei Stiebel Eltron durchgeführt.
Die bisher benötigten drei Werkzeuge für die Innenbearbeitung (Bohren für G1/2“ sowie Fasen 60° links und Fasen 60°rechts) konnten durch ein Werkzeug ersetzt werden.
Durch die Reduzierung der Bearbeitungsschritte und der Werkzeugwechsel konnte die Bearbeitungszeit um 40 % verringert werden und die Produktion deutlich gesteigert werden:
- Bearbeitungszeit 40% reduziert
- Produktivität 66 % gesteigert
- Standmenge auf 90.000 vervielfacht
Dritte Optimierung: Wendeschneidplatte ersetzt Einzelwerkzeug
Die Bearbeitung der äußeren Fasen (2×10°) an der schon erwähnten Mutter G1/2“ aus Messing erfolgte im Istzustand mit einem Sonderfaswerkzeug mit lediglich einer Schneidkante. Für Marcel Gobrecht und Michael Tobisch war klar, auch die Außenbearbeitung der Mutter muss optimiert werden, hier gehört eine Wendeschneidplatte hin.
Die erste Wahl für die Bearbeitung der äußeren Fasen war eine INGERSOLL GoldFlex-Fas-Stechwendeschneidplatte, die beide Fasen in einem Arbeitsgang anbringt. Im Gegensatz zum bestehenden Werkzeug mit einer Schneidkante, hat die gewählte Lösung vier Schneidkanten und bietet deutliche Vorteile in Bezug auf schnellen Werkzeugwechsel und Wiederholgenauigkeit.
Auch bei der Außenbearbeitung der beiden Fasen der Messingmutter konnte die gefundene Wendeschneidplattenlösung überzeugen.
Die Wendeschneidplatte bietet eine hohe Wiederholgenauigkeit sowie einen schnellen Wechsel und durch ihre 4-fach Schneide eine hohe Wirtschaftlichkeit. Zudem konnte im Testeinsatz auch eine 30 % höhere Produktivität erreicht werden.
Fazit:
Die gemeinsamen Optimierungsschritte der Zerspanungsfachleute von INGERSOLL und Stiebel Eltron in der Automatendreherei zeigen, dass durch exakte Analyse der Bearbeitungsoperationen und mit Hilfe moderner Werkzeuge maßgebliche wirtschaftliche Erneuerungen auch bei bestehenden Prozessen und mit vorhandenen Maschinen möglich sind.
Kontakt: