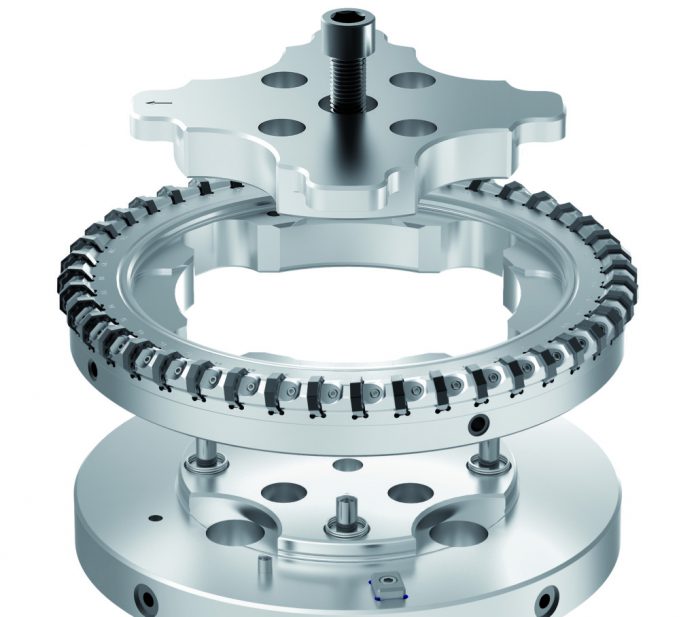
Guss ist überall. Die Turbinen großer Windkraftanlagen werden aus Guss gefertigt. Ebenso Motorblöcke, Getriebegehäuse und die Gehäuse von Turboladern. Auch die Pumpen, die Trinkwasser ins Haus fördern und die Hydraulikventile, mit denen die Leistung von Baumaschinen z.B. an die Baggerschaufel gebracht wird. Ohne Gusseisen wäre all dies nicht möglich. Die Entwicklungen von Kennametal ermöglichen kostengünstige wie effiziente Bearbeitung von Gusswerkstoffen und zugleich erlauben sie eine einfache Handhabung.
Ein wichtiger Schritt in diese Richtung wurde schon vor etwas mehr als einem Jahr vollzogen. Im Jahr 2016 stellte Kennametal die Fräserbaureihe Mill 16 vor. Diese Generation von Planfräsern wurde dezidiert entwickelt, um hohe Zerspanraten bei Gusseisen zu erzielen – mit höchster Produktivität und geringsten Kosten pro Schneide beim Schruppen und Vorschlichten.
Stark Erweitertes Portfolio
Die Mill 16-Plattform wurde aufgrund ihres Erfolges nun erweitert – um Grundkörper-Typen, Fräsgeometrien und für größere Durchmesser Fräser in geteilter Ausführung, die die Traglast an der Spindel reduziert.
Mit diesen Erweiterungen eignet sich das Mill 16-Portfolio für buchstäblich jede Applikation beim Fräsen von Komponenten aus Guss: Von Fräsern mit Keilklemmung in enger Teilung, mit denen auf leistungsstarken Maschinen hohe Produktivität erreicht wird, bis zu Fräsern mit eingeschraubten Wendeplatten in mittlerer und weiter Teilung für Maschinen mit begrenztem Leistungsspektrum, sowie von der Zerspanung von kleinen bis zu sehr großen Komponenten.
Das geteilte Gehäusedesign wurde für die Hochleistungsbearbeitung entwickelt, mit Fräsern mit Keilklemmung in Durchmessern von 300 bis 500 mm. Dabei muss sich der Anwender keine Sorgen wegen des Gewichtes machen, mit dem er die Maschinenspindeln belastet: Der größte geteilte Gehäusetyp der Mill 16-Plattform wiegt 20,4 kg. Das ist nur ein Drittel des Gewichtes, das vergleichbare Wettbewerbsfräser auf die Waage bringen. Dennoch erreichen die Planfräser eine maximale Drehzahl von 2800 U/min.
Und es gibt noch weitere gute Nachrichten. Alle Planfräser nutzen das gleiche innovative Design mit 16 effektiven Schneidkanten pro Wendeschneidplatte, das die Voraussetzungen für niedrige Kosten pro Schneide schafft.
Das erweiterte Mill 16-Portfolio deckt alle Anwendungen beim Schruppfräsen und der Semi-Schlichtbearbeitung von Guss ab. Wie aber sieht es mit der Endbearbeitung, d.h. dem Schlichten, aus?
KCFM: Feinschlichten mit gleichbleibend hohen Qualitäten
Aus der Sicht eines Motorherstellers sind glatte, feinstbearbeitete Oberflächen entscheidend. Ist dies nicht gegeben, können Leckagen auftreten, die zu aufwändigen Garantiefällen und unzufriedenen Kunden führen. Dasselbe gilt für andere Bauteile wie Getriebe, Hydraulikventile und Pumpengehäuse, bei denen stets eine glatte Oberfläche für die Dichtungen vorausgesetzt werden. Der dabei häufig zum Einsatz kommende Werkstoff Guss stellt sich für die Bearbeitung als eine echte Herausforderung dar.
Der Markt bietet heute verschiedene Optionen für die Schlichtbearbeitung von Guss, und mit den meisten lässt sich auch die gewünschte Oberflächengüte erzeugen.
Die Reproduzierbarkeit dieser Qualität steht aber auf einem anderen Blatt. Dies ist einer der „pain points“ aus Anwendersicht: Die Gewährleistung eines konstanten, verlässlichen Prozesses für das Schlichten von Guss.
Sobald die Schneiden nur leichten Verschleiß aufweisen, tritt schon eine Verschlechterung der Oberflächenqualität auf. Das führt zu einem erhöhten Druck auf das Werkzeug, was wiederum zu Vibrationen führt, und in der Folge sind Rattermarken sichtbar. Die Folge: Erhöhte Stillstandszeit durch häufigen Austausch der Schneiden.
Die hochpositiven Aufsteckfräser der Serie KCFM – Kennametal Cast Iron Finishing Milling – und die PCBN-Sorte KBK50 (PCBN = polykristallines Bornitrid) wurden exakt für diese Einsatzfälle entwickelt.
Anwender können nun mehr Teile pro Schneide bearbeiten und dabei eine gleichbleibende Qualität erzeugen. Das führt zu niedrigeren Bearbeitungskosten pro Bauteil. Außerdem reduzieren sich die Bearbeitungszeiten deutlich, weil PCBN im Vergleich zu Hartmetall-Wendeschneidplatten dreifach höhere Schnittgeschwindigkeiten erlaubt.
KCFM bietet noch mehr Optionen als nur PCBN
Die Kombination aus Keramik Sorte KY3500 zum Vorschlichten mit Schlichtschneiden der Sorte KBK50 ist eine produktive und zugleich kostensparende Lösung für Anwender die nicht ausschließlich PCBN-Wendeschneidplatten in ihrem Werkzeug einsetzen möchten.
PCBN und Keramikwerkstoffe sind die perfekte Lösung für Bearbeitungsprozesse unter stabilen Bedingungen in der Großserienproduktion.
In vielen Fällen muss die Schlichtbearbeitung aber unter eher instabilen Bedingungen erfolgen. Dazu gehören Faktoren wie die Aufspannung des Werkstücks, begrenzte Spindeldrehzahlen oder große Auskragungen.
Die Antwort darauf ist die Hartmetallsorte KC514M – eine TiAlN-PVD-Beschichtung, die sowohl zäh und verschleißfest ist. Sie wurde für leichte bis mittlere Bearbeitung entwickelt und kann mit oder ohne Kühlschmierstoffe eingesetzt werden.
Kontakt: