Die Forderung nach Gewichtseinsparung im Automobilbau hat längst über die traditionellen Alu-Komponenten im Bereich Motor- und Getriebebau hinweg Fahrwerks- und Strukturkomponenten erfasst. Besonders im Bereich Achsträger bieten moderne Aluminium-Bauteile enorme Vorteile. Die Masse des Achsträgers kann bei gleicher Stabilität verringert werden. Durch die Gewichtsverringerung stellen sich nicht nur die angestrebten Verbesserungen hinsichtlich Kraftstoffverbrauch und CO2 Einsparungen ein, auch das Fahrverhalten wird positiv beeinflusst.
Die Stabilität des Achsträgers verbessert den Bodenkontakt, das geringe Gewicht erhöht den Komfort und die Dynamik. Dies sind wichtige Argumente, weshalb moderne, fortschrittliche Automobilhersteller seit Jahren Fahrwerks- und Strukturkomponenten aus Aluminium verwenden.
und
Kontaktbereich der Schneiden bei Z = 4
Die Verwendung von Aluminium-Bauteilen hat auch in den Produktionsstandorten von BMW in Dingolfing eine lange Tradition. So stand auch die Bearbeitung eines Hinterachsträgers aus Aluminium für diverse Baureihen im Fokus der Fertigungs-verantwortlichen bei BMW im Werk Dingolfing.
Acht Anbindungen am Hinterachsträger (vier Schwingenanbindungen und vier Querlenkeranbindungen) wurden zusammen mit Firma Ingersoll analysiert und optimiert.
Aufgrund der gemeinsamen Istzustands-Analyse wurde seitens Ingersoll ein Aktionsplan mit folgenden Vorgaben erstellt:
- Reduzierung der Schnittkräfte
- Einbau sehr kurzer PKD-Blanks
- Reduzierung der effektiven Schneide
- Wechselseitige hoch-positive / negative Einbaulage der Schneiden, um einen sehr weichen Initialkontakt zu realisieren
- Ausgleich der axialen Schnittkräfte durch den positiven und negativen Einbau
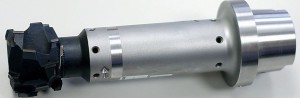
Um die Möglichkeit zur Reduzierung der effektiven Schneidenzahl zu untersuchen, wurden zwei Varianten mit Z = 4 und Z = 3 erarbeitet.
Untersucht wurde der Kontaktbereich der vorgeschlagenen Werkzeuge.
Nach Erörterung der Ist-Situation wurde entschieden, ein Testwerkzeug mit Z = 3 zu fertigen.
Weiterhin sollten bei dem Testwerkzeug die Spanräume möglichst weit geöffnet werden, um einen Spänestau im Spanraum zu verhindern.
Einsatz des Testwerkzeuges bei BMW
Wie im gemeinsamen Gespräch beschlossen, hat Ingersoll ein Testwerkzeug mit 3 effektiven Schneiden produziert. Das Werkzeug wurde für die Verwendung von Minimalmengenschmierung ausgelegt.
Das Werkzeug konnte Mitte 2013 zum ersten Male eingesetzt werden. Schon zu diesem Zeitpunkt war ein positives Fräsverhalten erkennbar.
Die nach einigen Monaten erreichte Standmenge überstieg dann alle Erwartungen. Es wurden in der Spitze Standmengen erreicht, die das 5 – 7fache der bisherigen Standmenge betrugen. Um eine stabile und sichere Produktion zu gewährleisten, wird in der Praxis mit den neuen Werkzeugen etwa die 3,5-fache Standmenge der bisherigen Werkzeuge als Standard erreicht.
Mit den neuen Werkzeugen konnte der Fräsprozess verbessert werden.
Neben der erwähnten Zerspanungsoptimierung bringt die enorme Standmengenverbesserung zudem eine Ersparnis bei den Werkzeugkosten.
Kontakt: